Metal clad wiper seals, often underappreciated in the world of engineering and manufacturing, play a pivotal role in protecting hydraulic and pneumatic systems. These components might seem simple, yet they carry the weight of ensuring optimal performance and longevity of machinery through their exceptional sealing capabilities.
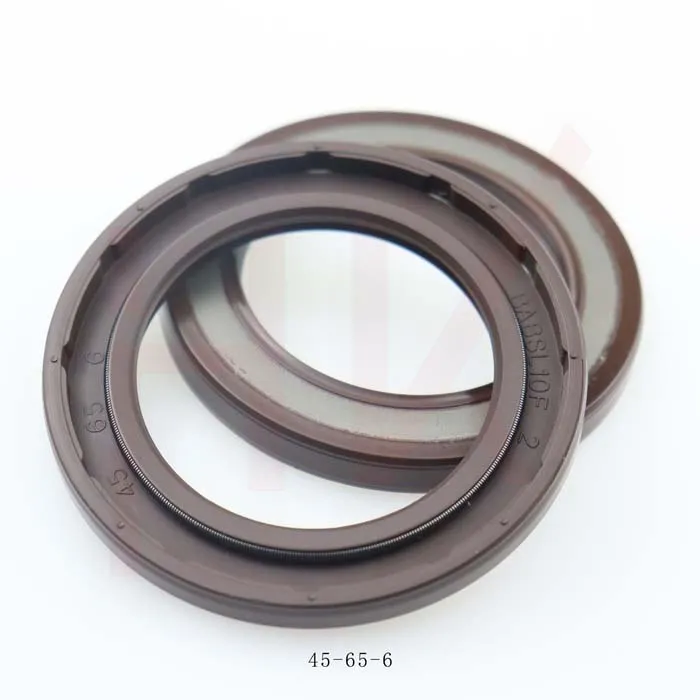
Having spent over two decades as a mechanical engineer specializing in fluid dynamics and seal technology, I've witnessed firsthand the transformative impact of high-quality wiper seals. These components are the silent guardians of industrial equipment, designed to prevent contaminants from entering hydraulic cylinders. By maintaining the integrity of the internal environment, they ensure machines perform efficiently, reducing downtime and maintenance costs.
Expertise in the selection and application of these seals is crucial. Manufactured with a robust metal exterior for enhanced durability, metal clad wiper seals are particularly known for their resistance to harsh environmental conditions. This construction ensures they withstand extreme temperatures, chemicals, and physical wear better than their non-metal counterparts. For industries such as mining, construction, and aerospace, where equipment failure can result in significant financial losses and safety hazards, these seals are indispensable.
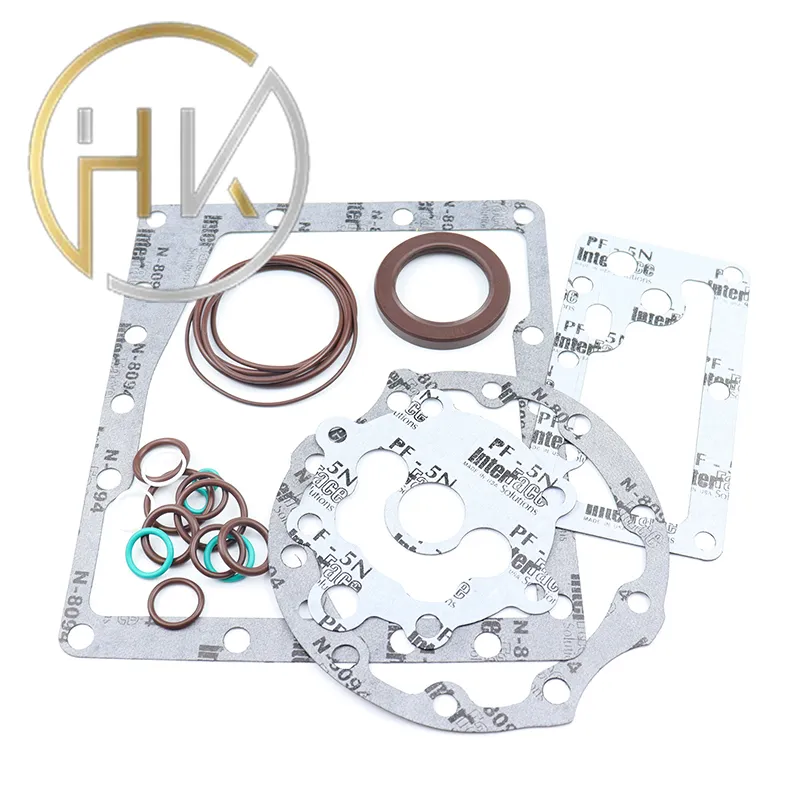
A crucial consideration when selecting wiper seals is the material compatibility. Not all seals are created equal, and understanding the compatibility with hydraulic fluids and environmental conditions is key to their effectiveness. Metal clad wiper seals are versatile, often crafted from high-grade stainless steel which complements the synthetic rubber or polyurethane used for sealing. This combination not only enhances the mechanical strength but also provides excellent fluid resistance, thereby elevating the seal's performance.
metal clad wiper seals
When we talk about authoritativeness in the niche of sealing technology, it’s important to reference industry standards and testing protocols. Metal clad wiper seals typically adhere to rigorous standards such as ISO and ASTM specifications, which define their expected performance under various stress conditions. This adherence to recognized standards imparts a sense of reliability and trust for engineers and procurement professionals. Choosing components certified by such bodies is not merely a recommendation; it’s a requisite for ensuring safety and efficiency.
In terms of trustworthiness, continuous innovation and stringent quality control processes practiced by reputable manufacturers underline the credibility of metal clad wiper seals. Companies dedicated to excellence in seal technology often invest in research and development to meet the evolving requirements of modern machinery. This focus on innovation translates into improved seal designs featuring reduced friction, longer lifespans, and enhanced protection against particle ingress.
Sharing a real-world experience, a leading mining operation reported a significant reduction in hydraulic failure-related downtime after transitioning from standard rubber wiper seals to metal clad alternatives. The robust construction of the metal clad seals withstood severe abrasive environments, a testimony to their superior performance and longevity. This adoption not only improved the reliability of the equipment but also lowered the maintenance frequency and associated costs, offering a substantial return on investment.
In conclusion, metal clad wiper seals are integral to the optimal operation and maintenance of sophisticated machinery across diverse industries. Their robust construction, compliance with international standards, and proven track record in challenging conditions mark them as indispensable components. As industries move towards more demanding applications, the reliability and efficiency of these seals continue to be crucial, ensuring industrial operations remain seamless and efficient. With a firm commitment to quality, innovation, and performance, metal clad wiper seals represent an investment in industrial reliability and efficiency.