Hydraulic pump seals are pivotal components in the world of hydraulic systems, serving as unsung heroes that ensure optimal performance and longevity. Their crafting and application require a blend of engineering expertise, material science, and practical know-how to meet industry demands. Understanding the role and maintenance of these seals can be the difference between a smoothly running system and frequent costly repairs.
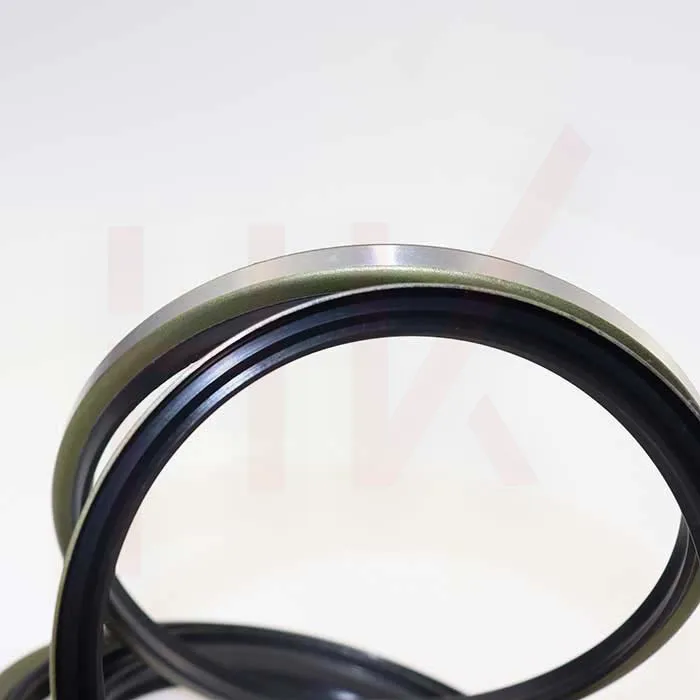
Hydraulic seals are designed to contain hydraulic fluid and convert fluid power into linear motion, playing a crucial role in preventing leaks from pumps and ensuring they function correctly. They are typically made from various materials, including PTFE, rubber, and polyurethane, each chosen based on the application requirements such as pressure, temperature, and fluid type.
The expertise required in creating effective hydraulic pump seals involves knowledge of these materials and their interaction with different hydraulic fluids under various operating conditions. Engineers must consider potential chemical reactions, abrasive wear, and thermal expansion when selecting the appropriate seal. For example, seals used in high-temperature environments need materials that can withstand thermal degradation without losing their elasticity or structural integrity.
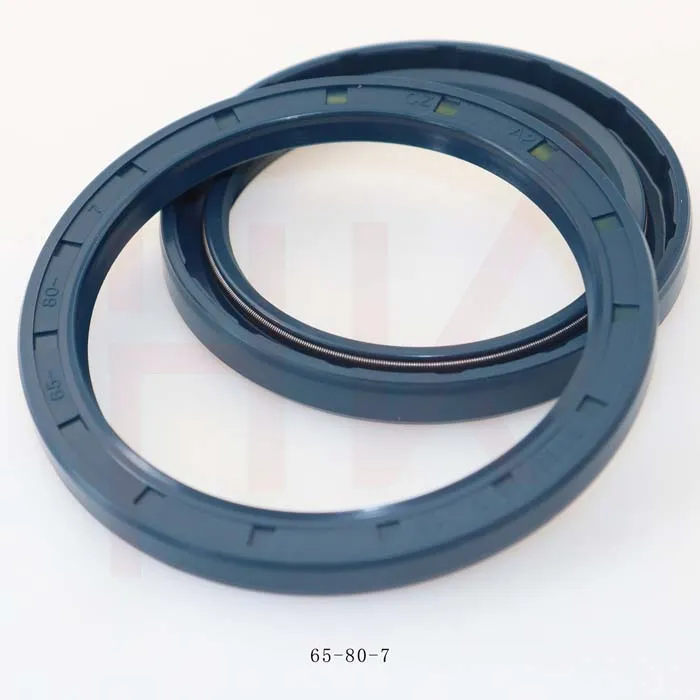
Authoritativeness in the field of hydraulic seals often comes from manufacturers who have invested years into research and development to innovate in seal technology. These companies, such as Parker Hannifin and SKF, not only offer a vast range of seals but also provide application-specific guidance to ensure that the correct seal is used for a given hydraulic pump system. Their expertise aids in reducing downtime and extending the lifespan of machinery, which is why industry professionals consistently turn to these established brands for reliable solutions.
hydraulic pump seals
Experience with hydraulic pump seals also brings an understanding of common failure modes, such as extrusion, wear, and thermal deterioration. Proper installation and maintenance are critical to extending a seal's service life and, by extension, the machinery's operating efficiency. Regular inspections and system monitoring can prevent seal failure by identifying signs of wear and damage. For instance, professionals often look for visual indicators like cracks or deformation, which suggest that a seal is approaching failure and needs replacement.
To enhance trustworthiness, providers of hydraulic seals often certify their products through rigorous testing standards. Certifications from organizations like ISO or industry-specific bodies validate that a seal can perform under specified conditions. This testing includes assessments for strength, durability, and resilience to chemical exposure, ensuring that the seals meet or exceed industry benchmarks.
One of the latest trends in the domain of hydraulic pump seals is the adoption of environmentally friendly materials. With increasing regulatory pressure and industry awareness about sustainability, engineers are seeking biocompatible and recyclable materials for seal construction. These innovations do not compromise on durability or performance, but rather enhance the seal’s ability to function in eco-sensitive applications.
In conclusion, hydraulic pump seals, while small components in hydraulic systems, are integral to ensuring efficiency and reliability. Expertise in material selection and application, combined with authoritative guidance and reliable manufacturing practices, creates a robust foundation for high-performing hydraulic systems. As industries evolve, constant advancements in seal technology and materials will continue to meet the growing demands for operational efficiency and environmental responsibility. Understanding these complex dynamics and applying them effectively distinguishes industry leaders from the rest, cementing their place as trusted partners in mechanical system operations.