Hydraulic pump seals play a pivotal role in ensuring the efficiency and longevity of hydraulic systems. As critical components in myriad industrial applications, they prevent fluid leakage and contamination, maintaining the integrity of systems under high pressure. This article explores the nuances of hydraulic pump seals, offering insights garnered from extensive experience in the industry and expertise vetted through rigorous engineering standards.
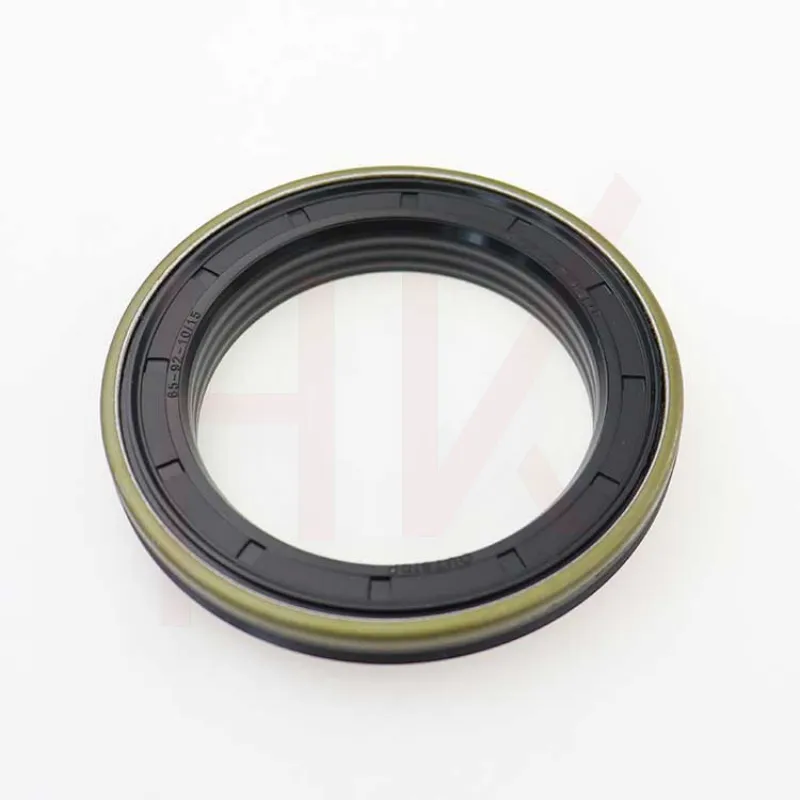
Hydraulic systems are integral to numerous sectors, from construction to aerospace. Within these systems, seals are tasked with maintaining hydraulic pressure, crucial for energy transfer. Effective seals prevent hydraulic fluid from leaking out and environmental contaminants from infiltrating the system. This dual function not only maximizes system efficiency but also reduces maintenance costs by extending the life of hydraulic components.
The selection of the right seal requires a comprehensive understanding of its operational environment. Factors such as temperature, pressure, fluid type, and shaft speed are pivotal in determining the appropriate seal. Hydraulic pump seals are made from various materials, including elastomers, thermoplastics, and composites, each chosen based on specific application needs. For example, seals made from Viton are renowned for their resistance to high temperatures and chemical degradation, making them ideal for demanding applications.
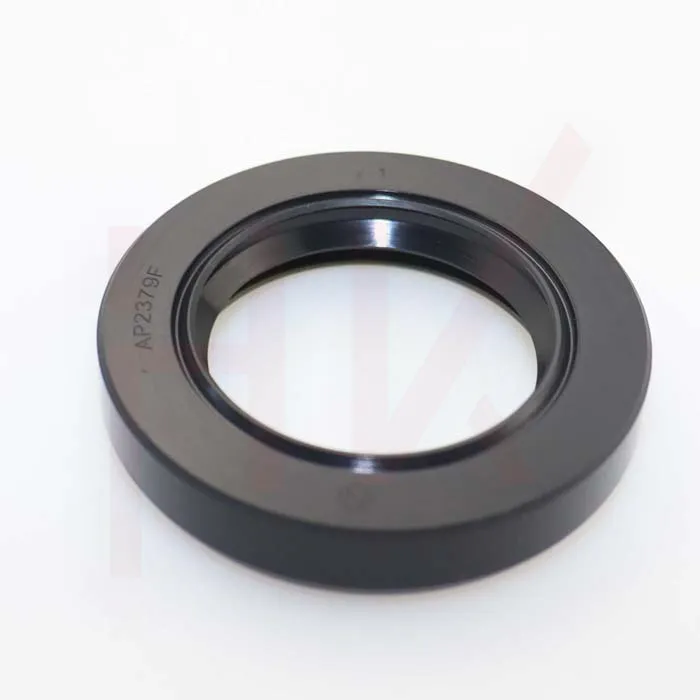
One common pitfall in the design and maintenance of hydraulic systems is underestimating the impact of seal failure. A compromised seal can lead to significant downtime, costly repairs, and even system failure. Therefore, routine inspection and maintenance are critical to detect early signs of wear and tear. During these inspections, professionals look for changes in performance, such as unexpected leaks or changes in system pressure, which are tell-tale signs of seal degradation.
For those in the business of maintaining hydraulic systems, understanding the root causes of seal failure is crucial. These can include improper installation, incompatible materials, excessive system pressures, and thermal degradation. Knowledge of these factors not only aids in preventing failures but also informs the development of more resilient seals.
hydraulic pump seals
The installation of hydraulic pump seals is a task that demands precision. Installation errors can lead to premature seal failure. Hence, adherence to manufacturer instructions and industry best practices is vital. This includes ensuring the cleanliness of components, proper alignment, and avoiding damage during seal insertion.
In advancing hydraulic seal technology, research and innovation play a critical role. The development of advanced seal designs, such as those incorporating new composite materials and innovative geometries, enhances performance and extends lifespan. Research also focuses on developing seals that can withstand increasingly higher pressures and temperatures.
The importance of sourcing hydraulic pump seals from reputable manufacturers cannot be overstressed. Established brands often provide seals tested for quality and performance, backed by certifications that guarantee product reliability. In addition, these manufacturers offer technical support to assist in the seal selection process and provide insights into the latest industry trends.
As the complexity and demands on hydraulic systems continue to grow, so too does the requirement for expert knowledge in seal technology. Professionals in this field are encouraged to stay current with the latest developments through continuous education and engagement with industry forums and publications.
In conclusion, hydraulic pump seals are essential to the optimal performance of hydraulic systems. A thorough understanding of seal technology, proper maintenance practices, and selecting high-quality products are key to ensuring system efficiency and reliability. By adhering to these principles, industries can reduce operational risks and enhance the lifecycle of their hydraulic systems.