Hydraulic motor seals play a pivotal role in the performance and durability of hydraulic motors, which are ubiquitous in heavy machinery, automotive applications, and industrial equipment. These seals are indispensable components that ensure the system's integrity by preventing leakage and contamination. Understanding the intricacies of hydraulic motor seals can significantly enhance their application efficiency and longevity.

First and foremost,
experience with diverse hydraulic motor systems reveals the critical importance of choosing the appropriate seal type for specific applications. Factors such as pressure ratings, temperature fluctuations, and fluid compatibility need careful consideration. For instance, applications involving high pressure and extreme temperatures require seals made from robust materials like PTFE or polyurethane, which offer enhanced resistance to wear and chemical degradation.
Furthermore, expertise in material science proves invaluable when selecting hydraulic motor seals. Each seal material provides unique benefits; nitrile rubber, for example, offers excellent resistance to oil and is cost-effective for moderate conditions, whereas fluorocarbon elastomers can withstand higher temperatures and abrasive environments. Knowledge of these materials allows engineers and technicians to select the optimal seal for maximizing motor efficiency and service life.
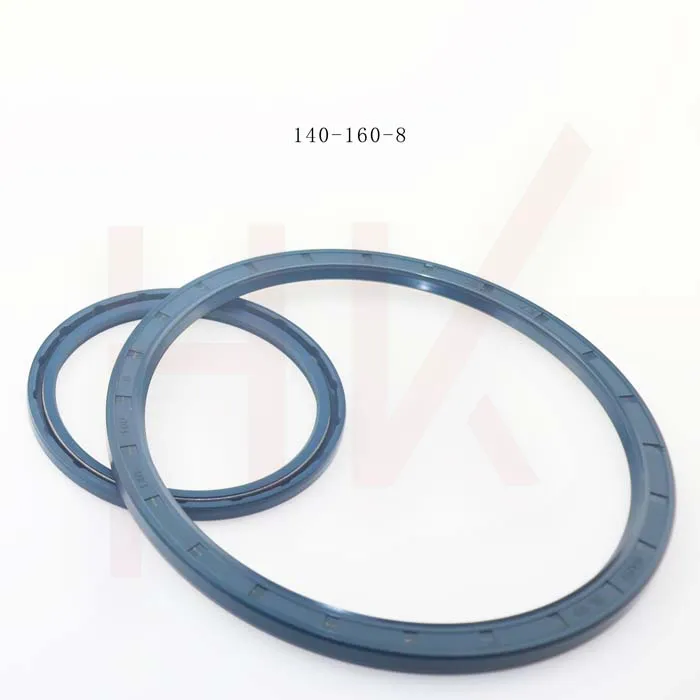
The use of hydraulic motor seals also emphasizes authoritativeness in maintenance protocols. Consistent monitoring and timely replacement of seals can avert catastrophic failures and downtime. Periodic inspections can identify wear patterns indicative of seal or system fatigue, which, if addressed promptly, can save significant costs. Implementing a proactive maintenance schedule based on authoritative guidelines from manufacturers ensures operational reliability and extends the motor's operational life.
hydraulic motor seals
Trustworthiness is another essential facet when dealing with hydraulic motor seals. Quality assurance through rigorous testing and adherence to industry standards fortifies confidence in seal performance. Collaborating with reputable manufacturers who provide certifications and warranty support assures end-users of the product’s reliability and operational integrity. Trust is further bolstered by transparent documentation that details installation procedures and maintenance best practices, empowering users with the necessary knowledge to correctly handle these critical components.
Advanced technologies like computer-aided design (CAD) and finite element analysis (FEA) have enabled the development of innovative sealing solutions tailored to specific hydraulic systems. These methodologies ensure that seals meet exacting specifications and operate under precisely simulated conditions. The synergy between advanced design technologies and real-world application enhances system efficiency and reliability, affirming a commitment to quality and innovation in seal manufacturing.
In conclusion, hydraulic motor seals require a nuanced understanding backed by experience, expertise, authority, and trustworthiness. From selecting the correct material and design to maintaining through rigorous protocols, every step is crucial for optimal performance. Investing in high-quality seals and adhering to best practices not only ensures efficient hydraulic motor operation but also substantially reduces maintenance costs and system failures, making them indispensable in any hydraulic-driven system.