A hydraulic cylinder is a crucial component in many industrial and heavy machinery applications, providing the strength and precision necessary for smooth and efficient operations.
Among the various parts of a hydraulic cylinder, seals play a vital role in maintaining the cylinder's performance and longevity. Failure to replace hydraulic cylinder seals at the appropriate time can lead to system inefficiencies, increased maintenance costs, and even equipment failure.
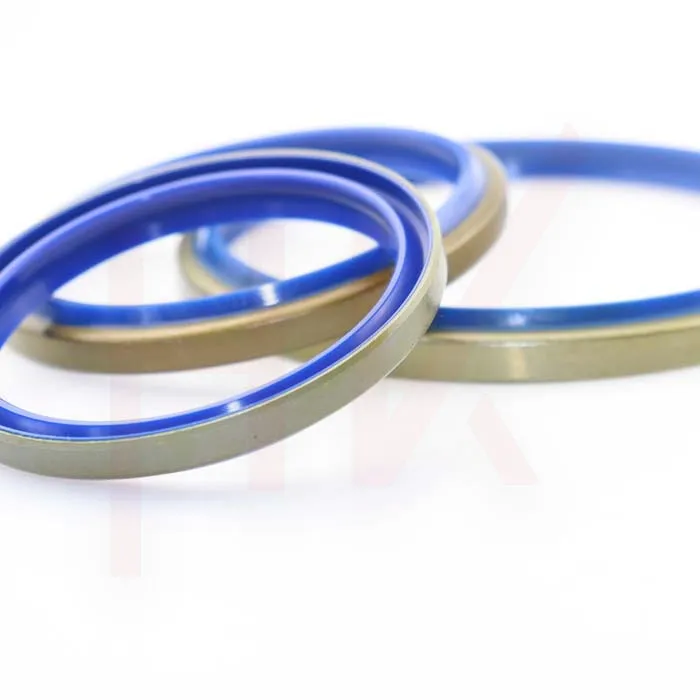
Understanding the significance of seal replacement begins with recognizing the common signs of wear. Hydraulic seals are subjected to extreme pressure and friction, which can lead to hardening, cracking, or complete breakdown over time. Indicators such as fluid leaks, pressure loss, or sluggish cylinder movement can serve as early warnings that a seal replacement is imminent.
Having a robust strategy for hydraulic cylinder seal replacement not only minimizes downtime but also enhances the long-term efficacy of the machinery. The first step involves selecting the appropriate seal type for the specific operational conditions. Factors such as pressure ratings, temperature variations, and the type of hydraulic fluid used all play into determining the right seal material, be it nitrile, Viton, or polyurethane.
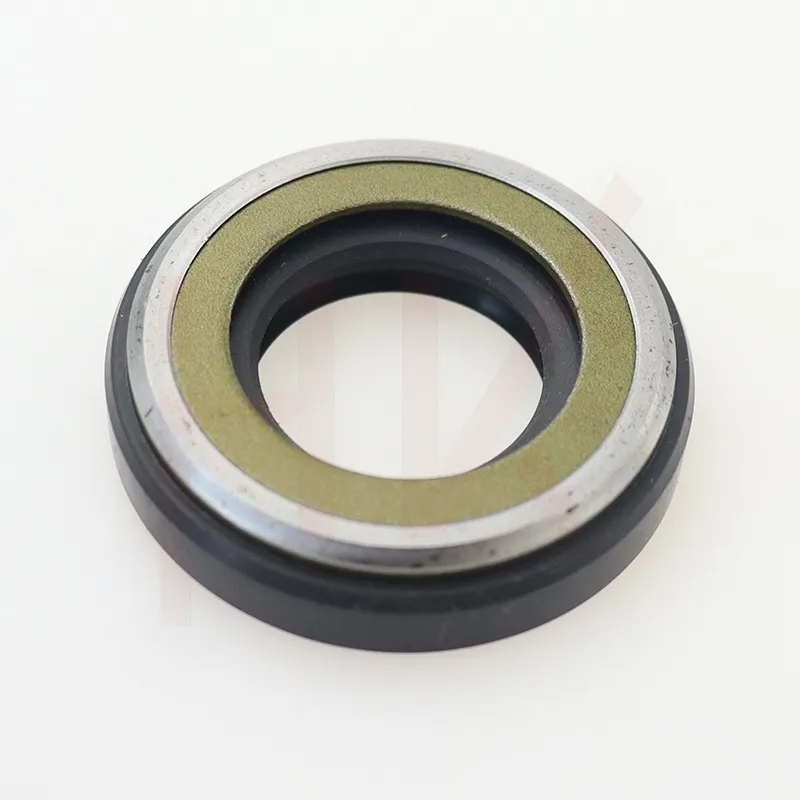
Specialized tools and techniques are paramount to achieving a successful seal replacement. From the precise removal of the old seals without damaging the cylinder bore to the careful installation of the new components, attention to detail is non-negotiable. Each step should adhere to OEM specifications to ensure the correct fit and function of the replacement seals, safeguarding against potential operational failures.
hydraulic cylinder seal replacement
Investing in high-quality seals is an investment in the machinery itself. Premium seals, although they may come with a higher upfront cost, can significantly reduce the frequency of replacements and the risk of catastrophic failures. Partnering with a reputable supplier known for their stringent manufacturing and quality assurance standards further bolsters the reliability of the replacement seals.
Additionally, adopting a proactive maintenance schedule can alleviate the burden of unexpected equipment repairs. Regular inspections can spot early signs of seal deterioration, allowing for preemptive action. Documenting the service history of each hydraulic cylinder can also provide invaluable insights into seal longevity and performance trends, allowing for more precise predictive maintenance.
For business owners and maintenance managers, investing in the training of personnel who handle seal replacements can yield significant returns. An informed technician not only executes the replacement process with higher precision but also contributes to the troubleshooting of related hydraulic system issues, driving overall operational efficiency.
In conclusion, hydraulic cylinder seal replacement is a critical aspect of machinery maintenance that demands careful consideration and execution. By embracing a strategic approach that includes selecting the right seals, employing professional techniques, investing in quality components, and maintaining a proactive maintenance regimen, organizations can achieve optimal performance and extended service life from their hydraulic systems. The commitment to understanding and implementing best practices in seal replacement translates directly into operational advantages and competitive business growth.