The evolution of machinery and vehicles has always been closely tied to the efficiency and reliability of their moving parts. Among these components, the hub oil seal plays a pivotal role that often goes unnoticed despite its importance in ensuring the longevity and performance of equipment. For anyone deeply involved in the maintenance or manufacture of mechanical systems, understanding the intricacies of hub oil seals can enhance operational efficiency and reduce downtime dramatically.
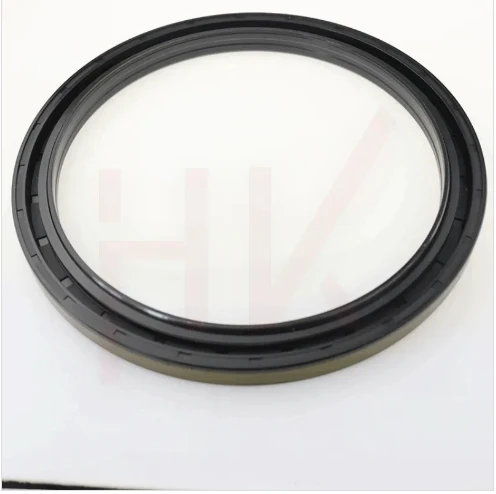
Hub oil seals are specifically designed to prevent the leakage of lubricating oil from the hubs of various machinery and vehicles. Without these seals, the oil meant to lubricate the internal components could escape, leading to increased friction, overheating, and eventual failure of parts. Duration between maintenance cycles would drastically shorten, affecting the overall cost-efficiency of any operation relying on such machinery.
Experience has shown that the key to an effective hub oil seal lies in its material composition and design. Typically constructed from high-performance rubber or other elastomers, these seals must withstand extreme temperatures, pressures, and exposure to various chemicals. For instance, seals in automotive applications must handle rapid temperature changes, offering reliable performance from cold starts to high running temperatures without degrading. Similarly, industrial machinery might demand seals that resist aggressive chemicals while maintaining integrity over prolonged periods.
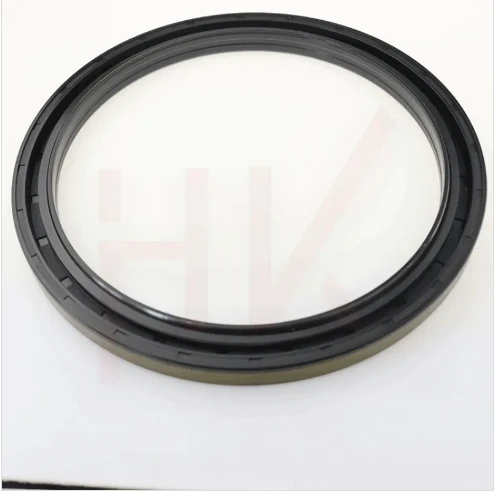
From a professional standpoint, the choice of a hub oil seal requires not just an understanding of the environmental conditions but also compatibility with the lubricants involved. Seals might seem like a minor component, but their failure can have catastrophic implications on equipment downtime and repair costs. Therefore, it's paramount to select a seal designed to resist not only basic wear and tear but also specific operational challenges. For businesses, this translates into lower maintenance costs and higher equipment uptime.
hub oil seal
In the realm of expertise, ongoing research and development continue to improve hub oil seal performance. Recent advancements include the development of hybrid seals that combine the best properties of traditional materials with cutting-edge engineering. For example, the combination of polytetrafluoroethylene (PTFE) with rubber offers superior wear resistance, lower friction, and unparalleled chemical stability. Mechanics and engineers utilizing these advanced seals often report increased service intervals and improved performance, signifying a leap in technological expertise applied to everyday operations.
Authority in the hub oil seal sector is primarily held by manufacturers with extensive experience and a track record of successful applications across industries. Brands that invest heavily in research and development to tailor their products to specific applications usually command respect and loyalty within the field. Their seals undergo rigorous testing to meet and exceed industry standards, ensuring not just compliance but leadership in technological advancement.
Trustworthiness of hub oil seals is critical, as operators need assurance that the seals will function as promised under a wide range of conditions. This focuses attention on quality management practices in manufacturing, ensuring that every seal delivered is consistent in quality and performance. Certified products with comprehensive warranties often indicate a higher level of commitment to quality from manufacturers, providing customers with the assurance they need to trust these small yet crucial components.
In conclusion, the humble hub oil seal represents more than just a minor part within the machinery. It encapsulates the principles of engineering excellence, reliability, and efficiency. For industries that depend on machinery for their operations, selecting the right seal is not merely a choice but a strategic decision that impacts the broader operational success. Through innovation and quality assurance, hub oil seals continue to uphold their essential role in modern mechanical systems, validating their critical contribution to industrial productivity.