In the world of engineering and machinery, components such as high-pressure rotary shaft seals play an instrumental role in ensuring effective performance and longevity of equipment. These seals are crucial in preventing fluid leakage in high-pressure environments, maintaining system efficiency and integrity. When selecting and utilizing these components, understanding their function, application, and design nuances becomes vital for engineers and technicians alike.

High-pressure rotary shaft seals are designed to accommodate the demands of applications subjected to elevated pressures, typically found in hydraulic systems, compressors, pumps, and automotive industries. They operate by maintaining the separation between fluid and atmospheric environments, which is critical for the prevention of equipment failure due to leakage or contamination.
Application expertise is paramount when dealing with these seals. The selection process should consider several factors such as pressure levels, shaft speed, fluid type, and temperature range. These seals are constructed of robust materials such as elastomers, PTFE, or metal, each chosen based on compatibility with the application’s operational environment. For example, elastomer seals such as NBR or FKM are preferred in low to moderate temperature ranges, while PTFE is used for higher temperature and chemically aggressive environments.
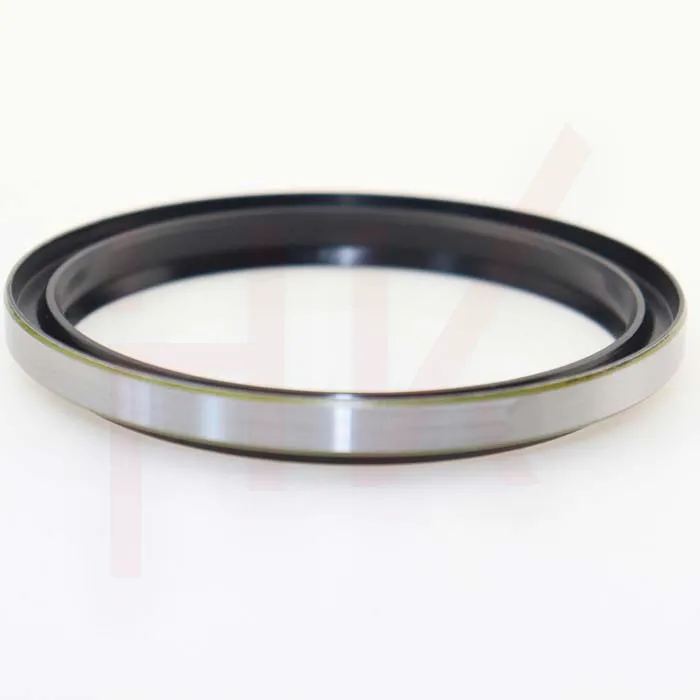
An authority in rotary shaft seals distinguishes themselves by offering tailored solutions compliant with industry standards. Knowledgeable professionals use advanced FEA (Finite Element Analysis) simulations to predict seal performance under various conditions, ensuring reliability and preventing costly downtime. Partnering with a reputable seal manufacturer can significantly boost trustworthiness, as their expertise in material science and mechanical engineering translates into products that consistently deliver optimal performance.
From an experiential perspective, securing the right high-pressure rotary shaft seal involves proactive maintenance and continuous monitoring of operational conditions. This means conducting regular inspections for wear and tear, ensuring proper shaft alignment, and adhering to recommended pressure limits. Advanced seals incorporate design features such as hydrodynamic aids or lip geometries that enhance lubrication and reduce wear, prolonging their service life.
high pressure rotary shaft seal
Furthermore, using a high-pressure rotary shaft seal that meets or exceeds quality certifications such as ISO 9001 or AS9100 can greatly enhance a company's credibility. These certifications provide assurance of quality control and continuous improvement processes in manufacturing, aligning with a company’s commitment to excellence and reliability.
Proper installation is another critical aspect, as even the finest seal can fail if incorrectly fitted. It's essential to follow manufacturer guidelines precisely, utilizing the correct tools and installation techniques to prevent damage during handling. Technicians should be trained in the nuances of seal installation, understanding the importance of cleanliness and precision to avoid contamination and misalignment.
Finally, the evolution in seal technology brings forth innovations such as seals with enhanced thermal properties and self-lubricating capabilities, suitable for demanding applications. Keeping abreast with these advancements is crucial for professionals aiming to maintain an authoritative edge in the industry.
In summary,
high-pressure rotary shaft seals offer invaluable protection and performance stability in various applications. By leveraging expertise, adopting a meticulous selection process, maintaining rigorous quality standards, and ensuring proper handling and installation, engineers and companies can achieve unparalleled results. Trusting in the power of innovation and expert guidance allows for maximizing the efficacy and lifespan of these critical components.