The high-pressure lip seal stands as a critical component in industries where fluid dynamics and mechanical integrity are paramount. Recognized not only for its versatility but also for its robustness, the high-pressure lip seal ensures optimal performance in challenging environments, setting a benchmark for seals used in hydraulic systems, automotive applications, and aerospace.
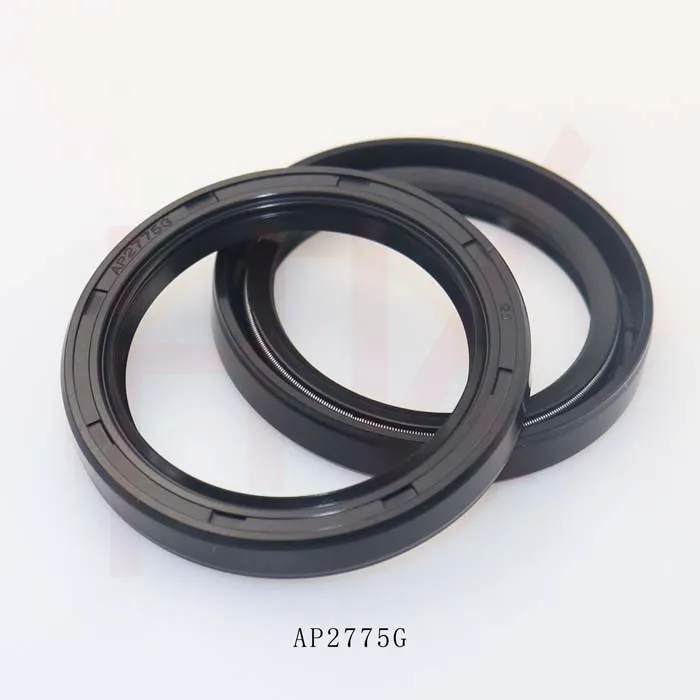
Structurally, the high-pressure lip seal is engineered to withstand demanding conditions by maintaining a high resistance against extreme pressures, temperatures, and fluid chemistries. These seals are designed with precision to reduce friction between moving surfaces, thereby enhancing efficiency and longevity of the machinery they serve. By creating a near-impenetrable barrier, they prevent the ingress of contaminants such as dust, dirt, and water, which can compromise the integrity of mechanical systems.
One of the most significant advantages of utilizing high-pressure lip seals is their exceptional capability to secure hydraulic applications. In an industry where hydraulic leakage can lead to catastrophic system failures, high-pressure lip seals offer a reliable solution. Their materials, often comprising advanced polymers and elastomers reinforced with metal inserts, are selected to perform optimally under high stress and temperature variances, ensuring the hydraulic fluids remain confined within the system.
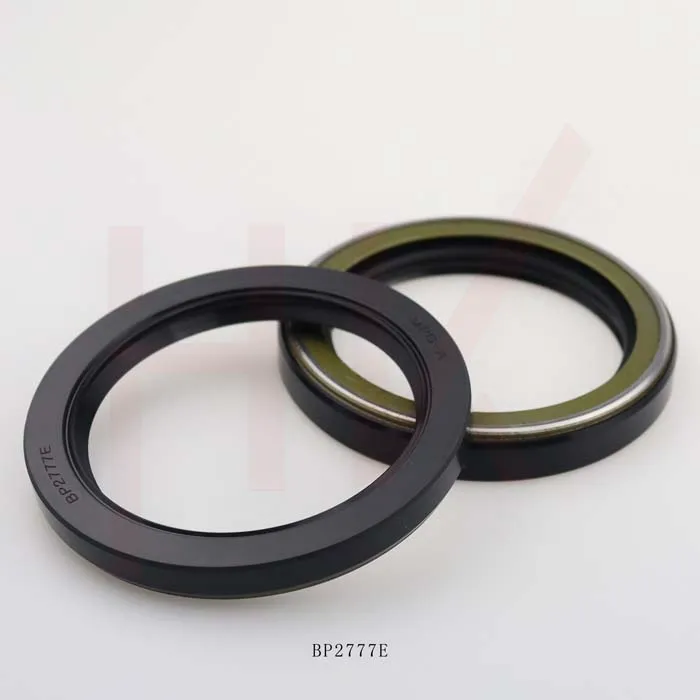
Drawing insights from industry experts, companies investing in high-pressure lip seals can attest to their resilience in enhancing system reliability. Their precision-engineered design aids in minimizing wear and tear, thus extending maintenance intervals and reducing downtime—an aspect crucial for industries like manufacturing and automotive where operational continuity is essential. Moreover, their ability to function under diverse operating conditions makes them a versatile choice for engineers and designers looking to enhance machinery performance.
The aerospace sector benefits immensely from high-pressure lip seals. Here, the operational narrative is one of extremes—extreme pressures, altitudes, and temperature fluctuations. High-pressure lip seals provide a critical interface, maintaining system integrity and preventing leaks that could otherwise lead to mission failure. Their high-performance materials sustain their elasticity and sealing capability over extensive cycles, underscoring their importance in aircraft hydraulic and fuel systems.
high pressure lip seal
From a product development perspective, the integration of advanced materials and novel design features categorizes high-pressure lip seals as pivotal. Continuous research and development efforts are made to enhance their compatibility with new fluids and emerging environmental regulations. By leveraging state-of-the-art technology, manufacturers are innovating seal designs that offer even greater resistance and durability, positioning them at the forefront of sealing technology.
Diversely, the authoritative value of high-pressure lip seals is supported by their compliance with industry standards and certifications. Engineers and procurement specialists emphasize the need to source these seals from reputable manufacturers who adhere to stringent quality assurance protocols. Certifications from bodies such as ISO or ASME affirm their commitment to providing products that meet and exceed safety and quality expectations.
In practice, the real-world application of high-pressure lip seals offers a valuable lesson in the synthesis of technology and material science tailored to solve specific engineering challenges. Interviews with field professionals reveal that correct installation and regular maintenance play pivotal roles in maximizing the seals’ lifespan and performance. Specific training programs dedicated to the proper installation techniques and maintenance schedules have been instrumental in ensuring these seals realize their full potential in operational settings.
In conclusion, high-pressure lip seals stand testament to the advancements in sealing technology and reflect deep-rooted expertise and industry knowledge. Their unique ability to offer unparalleled sealing solutions showcases their prominence across multiple industries, confirming their place not only as a critical component but as a catalyst for improved industrial reliability and efficiency.