The advancement in industrial technology has ushered in a new era of efficiency and precision, with dual loader cylinder seals playing a pivotal role. As the components that ensure the optimal functionality of machinery, these seals serve as a crucial interface in hydraulic systems designed to resist leakage and retain pressure. For professionals seeking to optimize their operational infrastructure or enhance product reliability, understanding the nuances of dual loader cylinder seals is invaluable.
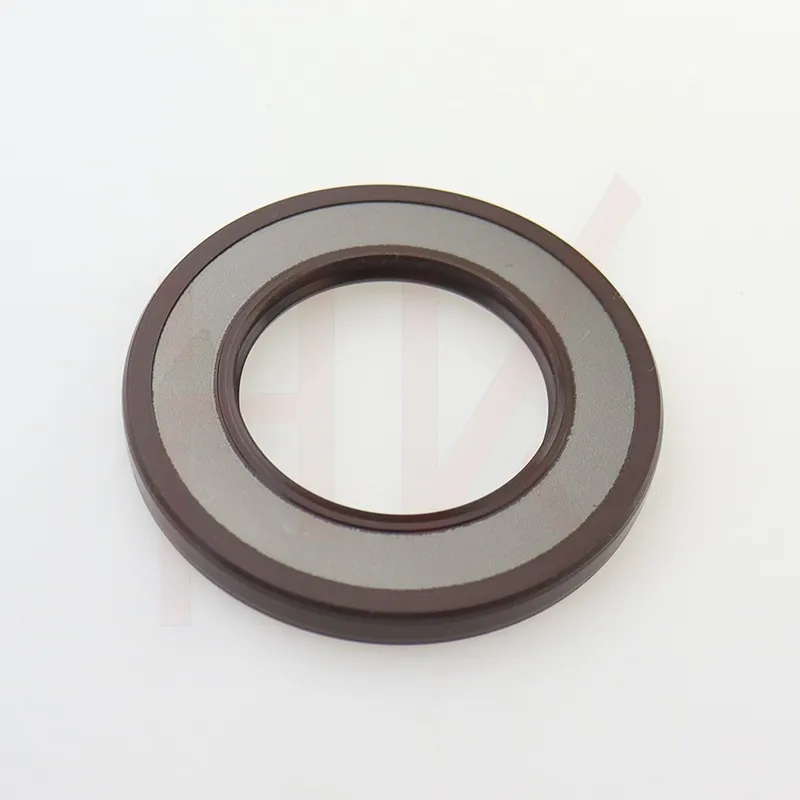
In the heart of numerous hydraulic systems across industries ranging from construction to manufacturing, dual loader cylinder seals are integral. They provide the necessary barrier between the internal mechanics of a system and the external environment, reducing contamination risks and extending the life of the equipment. Crafted from high-grade materials like polyurethane and rubber, these seals are engineered to withstand the challenging conditions they frequently encounter, including high pressure and varying temperatures.
One of the remarkable features of dual loader cylinder seals is their dual functionality. By acting both as a seal and a guide, they maintain the alignment of the piston with the cylinder bore, preventing metal-to-metal contact that can lead to premature wear and tear. This not only maintains the structural integrity of the equipment but also ensures precision in movement, vital for tasks requiring high accuracy.
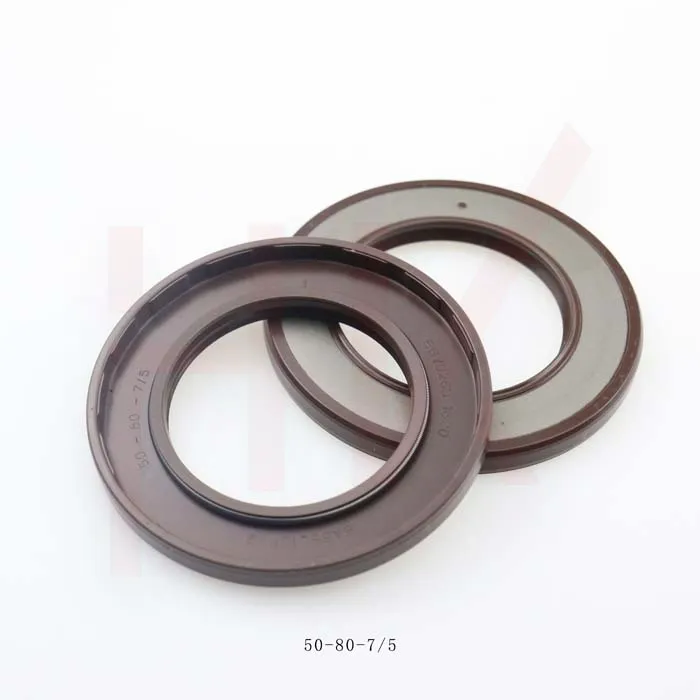
Moreover, the design intricacies of dual loader cylinder seals illustrate a blend of engineering expertise and material science. Each seal is meticulously crafted to address the specific needs of diverse applications. Whether it’s resisting aggressive chemicals, enduring extreme temperatures, or handling excessive pressure, these seals must be precisely tailored to the demands of the environment they are part of. This customization is often based on rigorous testing and a deep understanding of the operational dynamics involved.
dual loader cylinder seals
For businesses, particularly those reliant on heavy-duty machinery,
selecting the right dual loader cylinder seal becomes a strategic decision. The wrong choice can lead to catastrophic failures, expensive downtimes, and significant financial losses. Therefore, consulting with professionals who possess authoritative knowledge on hydraulic systems and component specifications can not only enhance operational efficiency but also fortify the trustworthiness of equipment performance.
Furthermore, maintaining a robust documentation practice regarding the performance metrics of dual loader cylinder seals can be immensely helpful. By analyzing seal wear patterns, pressure resilience, and temperature tolerance, businesses can make informed decisions about maintenance schedules and component replacements. This data-driven approach fosters a culture of continuous improvement, ensuring that machinery operates at its peak potential.
Additionally, leveraging expert consultation can provide critical insights into advancements in seal technology. With the rapid development in materials science, innovations such as improved elastomer technology or advanced composite materials can offer enhanced durability and flexibility. Staying informed about these advancements allows businesses to keep their machinery updated with the most efficient and reliable components.
In conclusion, the role of dual loader cylinder seals goes beyond mere functional necessity—they are instrumental in safeguarding the operational integrity of hydraulic systems. By prioritizing their design, material selection, and maintenance, businesses can achieve significant improvements in performance and reliability. As such, collaborating with experienced professionals and embracing technological innovations in seal design not only elevates machine efficiency but also fortifies the trust that stakeholders place in a company’s operational capabilities. Thus, dual loader cylinder seals are not just components; they are cornerstones of industrial advancement and operational excellence.