The double lip oil seal, a critical yet often overlooked component, holds paramount importance in the seamless functioning of innumerable industrial machinery. To truly appreciate its value, one must delve into its design, function, and application, all of which amalgamate to enhance equipment longevity and performance.
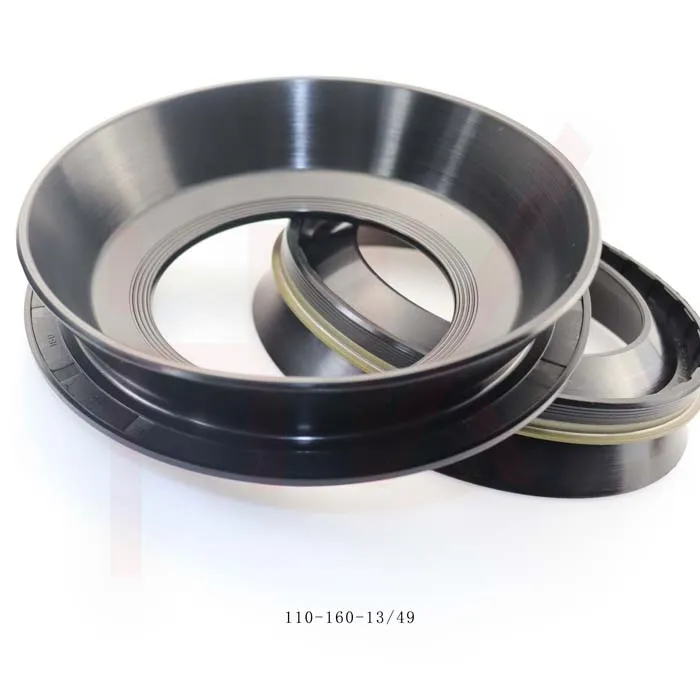
At its core, the double lip oil seal serves as a barrier, designed to retain lubricants and exclude contaminants within a mechanical system. Its dual-lip configuration offers an augmented sealing effect compared to its single lip counterpart. The first lip primarily works to retain lubricant within the system, ensuring that friction between moving parts is minimized, thereby prolonging their life. The secondary lip functions as a defense mechanism against external contaminants such as dust, dirt, and moisture, preventing these elements from compromising the internal integrity of machinery.
The expertise involved in manufacturing double lip oil seals cannot be overstated. Crafted from high-grade materials such as nitrile rubber, fluorocarbon, or silicone, these seals are engineered to withstand varied temperatures, harsh chemicals, and diverse operational environments. The meticulous engineering behind the lip design further enhances their flexibility and durability, ensuring a snug fit that adapts to shaft irregularities without compromising performance.
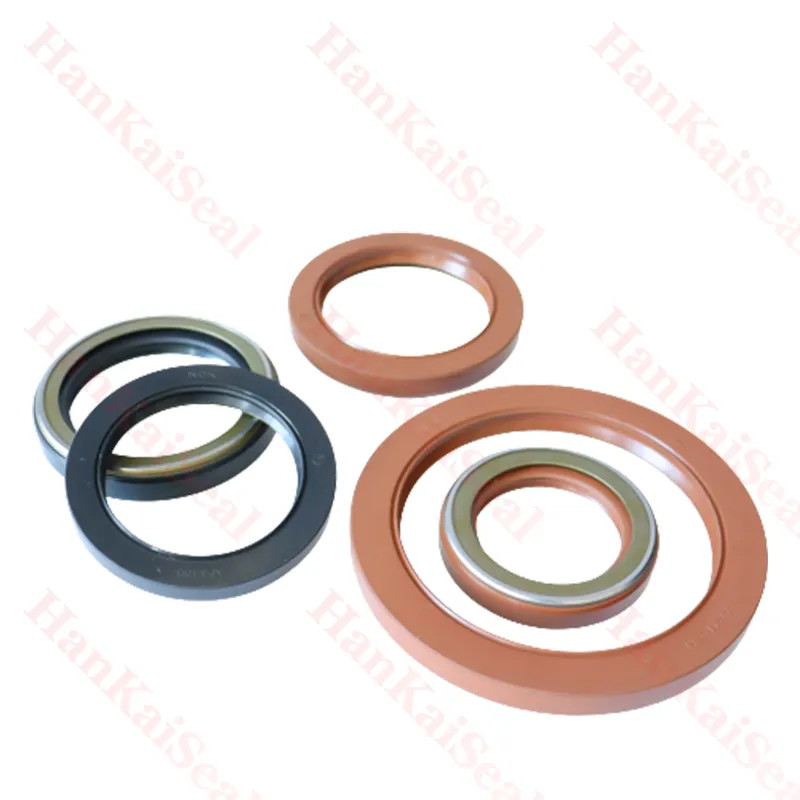
In industries such as automotive, aerospace, and heavy machinery manufacturing, the authoritative application of double lip oil seals is indisputable. Their role is especially crucial in environments where the machinery is subject to rigorous and continuous operation. For example, in the automotive industry, these seals are integral to the proper functioning of engines and transmissions, where they help maintain the lubrication required for smooth operation while simultaneously safeguarding critical components from destructive external elements.
Beyond the obvious mechanical advantages, the implementation of double lip oil seals offers greater economic benefits by reducing maintenance costs and machine downtime. Regular maintenance schedules often reveal that the presence of a double lip oil seal significantly reduces wear and tear on equipment, diminishing the frequency of part replacements and repairs. This reliability builds trust with users, resulting in long-term savings and enhanced productivity.
double lip oil seal
However, realizing these benefits hinges on the understanding and trustworthiness of the information propagated about double lip oil seals. Professionals tasked with selecting oil seals must rely on trustworthy suppliers and detailed technical data that accompany these components. Verified customer reviews and case studies can further provide real-world insights, fortifying the confidence of those making purchasing decisions.
Product authenticity also plays a vital role in fostering trust. Counterfeit parts are a pervasive issue within the industry, often leading to catastrophic machinery failures. Engaging directly with certified manufacturers and suppliers is imperative to ensure authenticity, performance, and compatibility of the double lip oil seals with the machinery in question.
Additionally, it is crucial that these seals meet international quality standards, such as ISO 6194 or DIN 3760, ensuring they have passed rigorous testing for endurance and functionality. Compliance with these standards not only guarantees product quality but also reinforces the manufacturer's credibility, making them a reliable partner for industries globally.
In conclusion, the double lip oil seal is more than just a mechanical component; it is a linchpin in the efficient operation and longevity of industrial machinery. Through meticulous design, durable materials, and authoritative application, these seals transcend mere functionality, embodying reliability and trust. For stakeholders across the industrial spectrum, these qualities are indispensable in the pursuit of excellence and efficiency. Prioritizing quality and authenticity in these seals will unequivocally result in streamlined operations, reduced costs, and trust in machinery performance – aligning perfectly with the core goals of any industrial endeavor.