The world of industrial machinery is intricate, demanding precision and reliability from even the smallest components. One such critical component that holds significant weight in this domain is the oil seal. Specifically, when we talk about the 80x100x10 oil seal, we delve into a niche that requires not just understanding, but expertise.
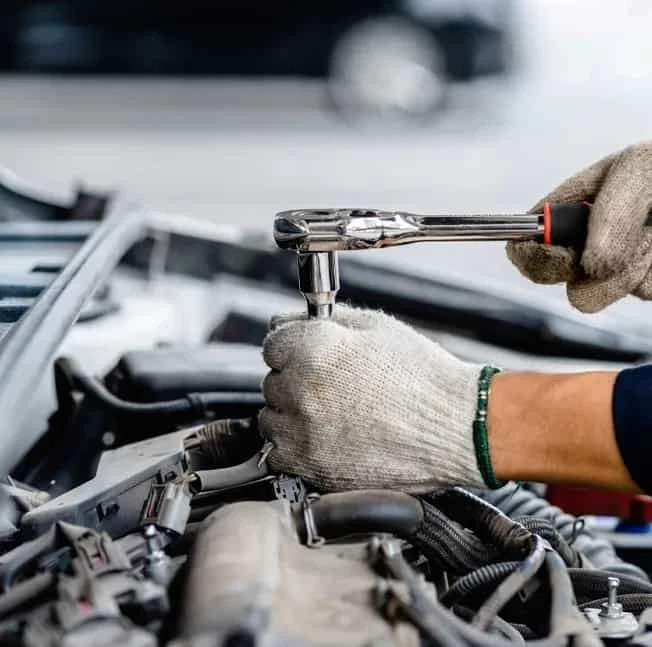
Oil seals, also known as rotary shaft seals, play a vital role in preventing leakage of lubricants, ensuring that the machinery operates efficiently without the intrusion of external particles.
The dimensions 80x100x10 reflect its metric sizing an inner diameter of 80mm, an outer diameter of 100mm, and a thickness of 10mm. This particular size is often used in various heavy machinery and automotive applications where the balance between size and sealing capability is crucial.
Years of engineering expertise have refined the design and materials used in crafting these seals to maximize performance. The material selection is critical; Nitrile rubber (NBR) is commonly used, offering excellent resistance to petroleum-based oils and fuels. However, when higher temperature resistance is required, Fluorocarbon (Viton) might be preferred. This material choice directly impacts the seal’s longevity and effectiveness, especially in harsh operating environments.
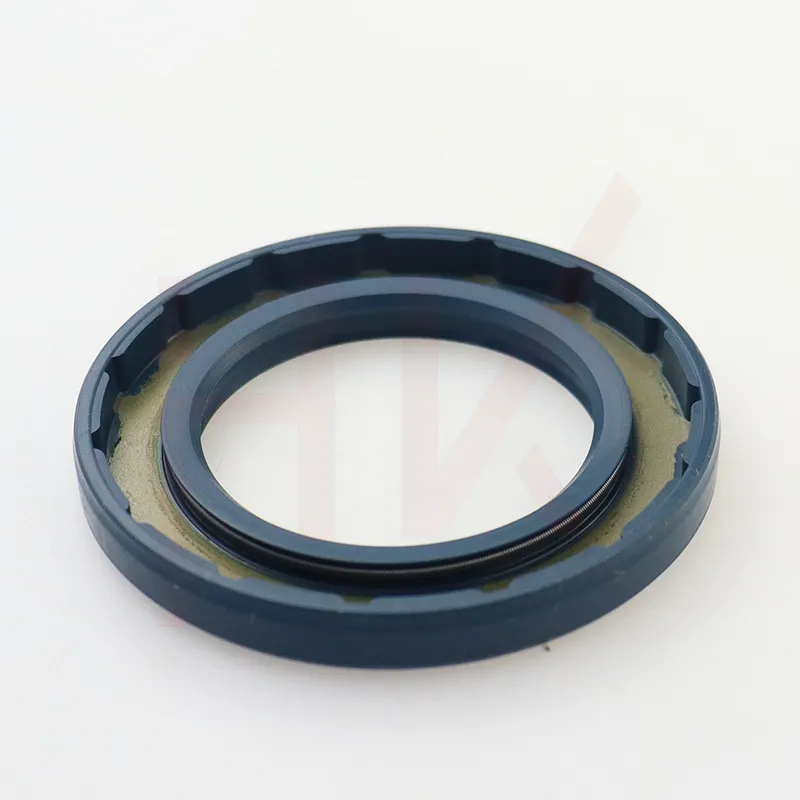
From an authoritative perspective, understanding the application environment is paramount. Different machinery operates under varying conditions of speed, temperature, and pressure. The 80x100x10 oil seal is designed to withstand radial and axial movements of the shaft while maintaining an airtight seal. This ensures no loss of lubricants, reducing wear and tear on components and maintaining operational efficiency.
Trustworthiness in oil seals, especially this size, comes from proven field performance. Manufacturers of high repute employ rigorous testing protocols to certify seals. Factors like compression set, hardness, and tensile strength are meticulously tested to meet international standards such as ISO or DIN. End-users should always seek seals that come with comprehensive testing credentials, ensuring reliability and safety in operation.
80x100x10 oil seal
Experience from industry experts emphasizes the importance of proper installation. Even the most precisely manufactured 80x100x10 oil seal can underperform if not correctly installed. Ensuring the shaft surface is smooth, measuring gland dimensions accurately, and proper lubrication during installation are critical steps. These practices prevent premature wear and improve the lifespan of the seal.
In trouble-shooting scenarios, common issues with oil seals can stem from environmental factors such as excessive heat, misalignment, or contamination. Regular maintenance checks, focusing on these potential pain points, can help in early detection and mitigate costly downtime. Experts recommend an integrated approach where alongside the use of high-quality seals, regular monitoring systems are implemented to maintain optimal performance.
For businesses sourcing these components, finding a reputable supplier is crucial. Suppliers who invest in research and development, and provide after-sales support, add significant value. They not only supply the seal but offer technical support, helping businesses adapt seals to specific needs and environments, thereby enhancing operational reliability.
In conclusion, the 80x100x10 oil seal is more than just a component; it is a guardian of efficiency and productivity in machinery. Through a combination of superior materials, meticulous engineering, and rigorous testing, this oil seal size remains a trusted choice for professionals seeking reliability in their industrial or automotive applications. Engaging with knowledgeable suppliers and adhering to best installation practices ultimately ensures optimal performance and extends the operational lifespan of machinery.