Navigating the realm of oil seals requires not just a cursory glance but a deep understanding of how their dimensions and construction cater to specific industrial needs. The 50x90x10 oil seal exemplifies a sophisticated engineering solution designed to maintain the integrity of mechanical systems across various sectors.
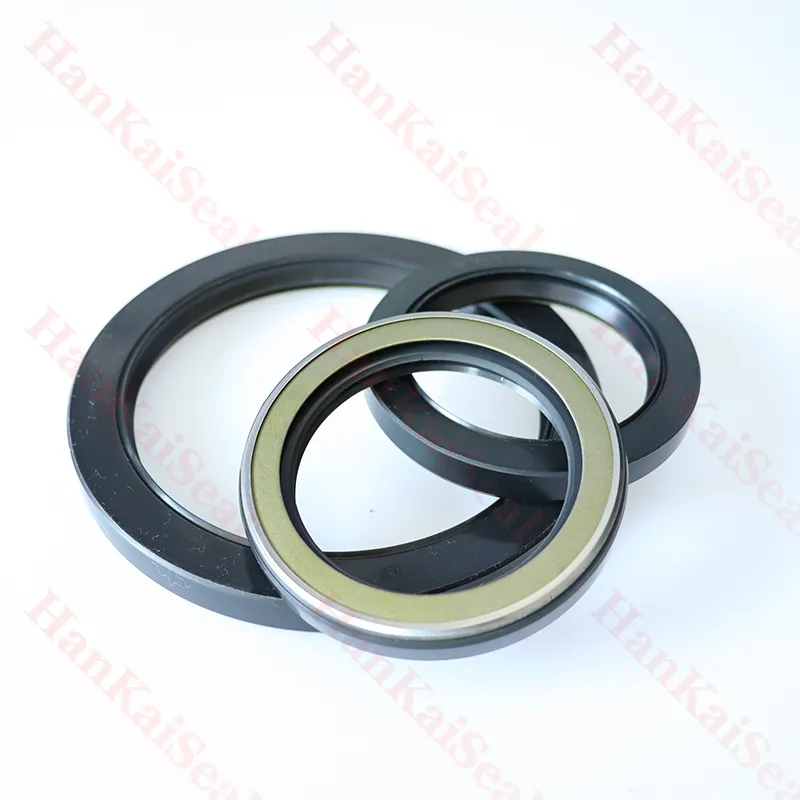
The dimensions,
50x90x10, denote the critical measurements that define this seal's function. A 50mm inner diameter allows precise accommodation onto shafts, ensuring a tight fit that minimizes the risk of contaminants infiltrating critical areas. The 90mm outer diameter fits securely within the housing, creating a barrier against external ingress, while a 10mm width provides stability and resilience, crucial in environments with fluctuating pressures or temperatures.
Expertise in the material composition of oil seals is essential for their optimal performance. Typically, 50x90x10 oil seals are crafted from high-grade nitrile rubber or fluoroelastomer compounds. Nitrile is praised for its excellent resistance to oils and some chemicals, making it ideal for automotive and industrial applications where exposure to lubricants is a constant. Conversely, fluoroelastomer, or FKM, offers superior thermal and chemical resistance, making it suitable for more demanding applications, like aerospace or chemical processing industries. Understanding these material characteristics enables businesses to select seals that prolong equipment life and reduce maintenance costs.
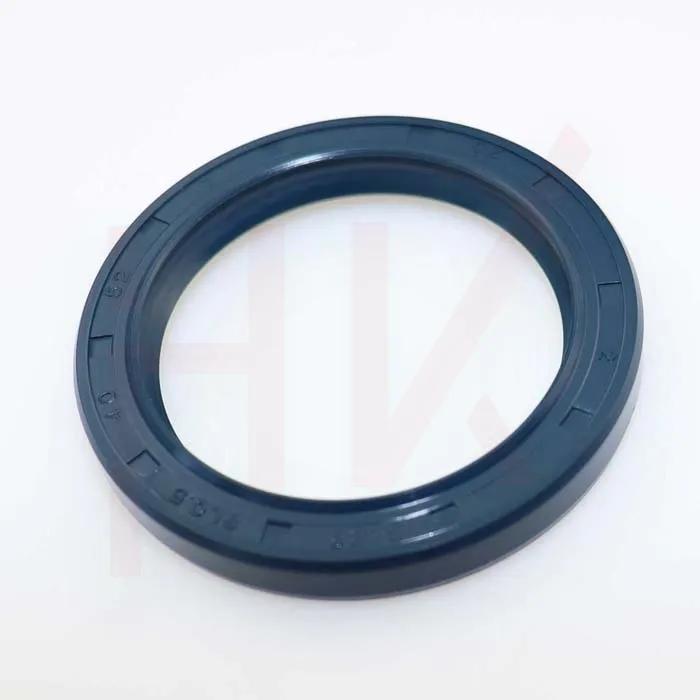
The authoritativeness of the 50x90x10 oil seal also lies in its design elements, notably the spring-loaded lip. This component exerts constant pressure against the rotating shaft, maintaining a seal even when the equipment is at rest or under high operational speeds. The design accounts for minor shaft misalignments, which are common in dynamic operations, and ensures reliable performance, significantly cutting down the likelihood of unscheduled downtimes.
50x90x10 oil seal
Moreover, authenticating the source and quality of oil seals is paramount. Procuring products from reputable manufacturers ensures adherence to international standards such as ISO/TS 16949, which governs quality management systems in the automotive industry. For industries beyond automotive, compliance with standards such as ISO 9001 can further validate a manufacturer’s commitment to quality. Trustworthiness is further bolstered by manufacturers who provide thorough testing results and certifications, demonstrating the seal's ability to uphold its integrity under specified conditions.
Industrial professionals with substantial experience often advocate scheduling regular inspections and replacements of oil seals, thereby preserving equipment efficiency. Over time, even the most robust oil seals like our 50x90x10 model can suffer wear and tear due to factors such as vibration, friction, and thermal cycling. Implementing preventive maintenance practices can mitigate the risks of unexpected failures and costly repairs.
The strategic implementation of 50x90x10 oil seals extends beyond just machinery preservation; it involves cost-benefit analyses that focus on long-term operational efficiency. High-performing seals can significantly cut down lubricant wastage and prevent costly leaks that might otherwise pose safety risks or environmental hazards. The expertise of maintenance engineers in integrating these components into their machinery further underscores the seal's value, optimizing resource allocation and boosting profitability.
In essence, the 50x90x10 oil seal stands as a testament to engineering prowess, embodying tailored solutions that address both common and niche requirements within mechanical systems. Its thoughtful design and reliable performance are cornerstones in promoting operational longevity and sustainability across diverse industrial landscapes. Leveraging this specific oil seal model can markedly enhance the reliability and efficiency of machinery, securing its spot as an indispensable component in the toolkit of seasoned industry professionals.