Choosing the right oil seal for your machinery is indispensable for ensuring efficiency and longevity. With an array of options available, the 40x55x8 oil seal stands out due to its precise dimensions and applications. Let's delve into the features, applications, and considerations of this particular oil seal to enrich your understanding and aid your purchasing decisions.

The 40x55x8 oil seal is engineered for precision and durability, performing optimally in dynamic environments.
The numbers 40x55x8 refer to the dimensions in millimeters, where 40 is the inner diameter, 55 is the outer diameter, and 8 is the thickness of the seal. This specific configuration makes it suitable for machinery that operates under moderate loads and speeds, providing a secure barrier against contaminants while ensuring that lubricants do not escape from the housing chamber.
A key feature of this oil seal is its high resistance to various environmental factors. Typically constructed from materials like Nitrile Rubber (NBR) or Viton, the seal offers exceptional resistance to wear, heat, and chemical exposure. Nitrile Rubber is widely used due to its affordability and adequate resistance to oils and fuels, whereas Viton is preferred in situations demanding higher chemical resistance and operating temperatures. Selecting the appropriate material based on your operational environment is paramount for achieving optimal performance.
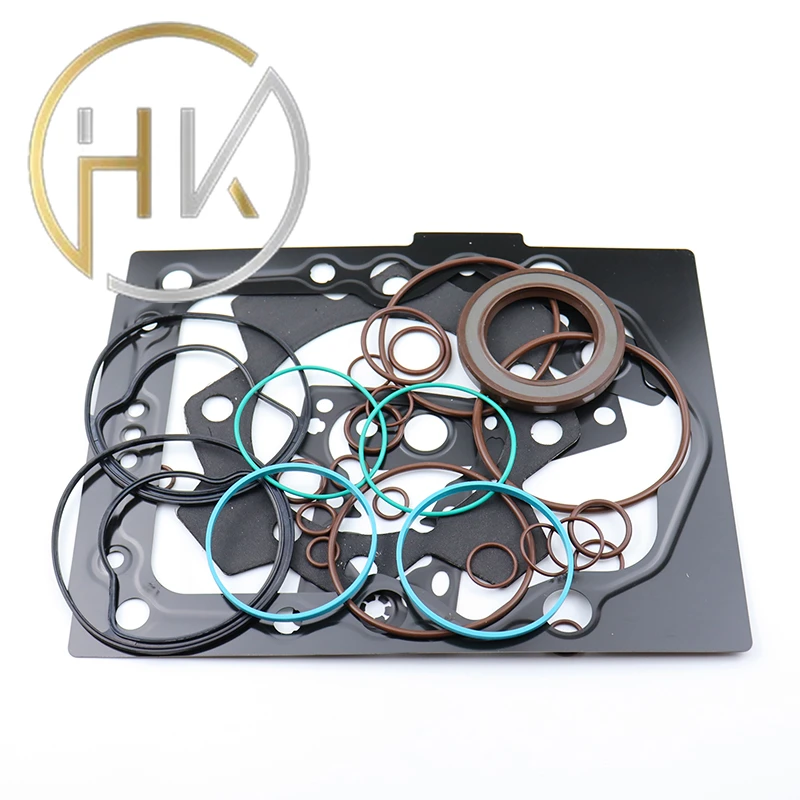
In terms of application, the 40x55x8 oil seal is commonly utilized in automotive engines, gearboxes, and industrial pumps. Its design is crucial for maintaining the integrity of these systems by preventing oil leaks, which could otherwise lead to costly repairs or downtime. In an engine, for instance, this seal retains lubrication in the crankshaft while preventing dirt and moisture ingress, thus safeguarding internal components from premature wear.
40x55x8 oil seal
Ensuring the credibility and longevity of your equipment begins with understanding the role of correct installation. Misalignment or incorrect installation of an oil seal can lead to rapid deterioration and failure. The use of proper tools and techniques, as well as adherence to manufacturer guidelines, cannot be overstressed. Cleanliness is also vital; any contamination on the seal lips or the sealed surface can compromise the performance.
Expert consultation is beneficial, especially when dealing with unique environmental conditions or specific machinery requirements. Consulting with a certified technician or supplier can provide insights into material science and seal technology, ensuring you choose the best fit for your application. Furthermore, sourcing from reputable manufacturers guarantees product authenticity and access to technical support if necessary.
Regular maintenance and inspection are instrumental in prolonging the life of oil seals. Scheduled checks for signs of wear, tear, and leakage should form part of routine maintenance. Immediate action following identification of potential issues can prevent extensive damage to machinery, contributing to overall system reliability and efficiency.
The decision to use a 40x55x8 oil seal should not merely be based on size compatibility. Its quality, material composition, and the specific demands of your operational environment are all critical factors that influence both its performance and lifespan. Equipped with this knowledge and guided by industry expertise, you can make informed decisions that enhance machinery performance and extend operational life.