Searching for the perfect oil seal can be challenging, especially if you're working with a specific requirement such as [35 72 10 oil seal]. These numbers are not random; they denote important dimensions that must align with your machinery's needs — 35mm inner diameter, 72mm outer diameter, and 10mm width. Understanding these specifications is crucial for ensuring that the product meets your system's requirements and maintains optimal performance.
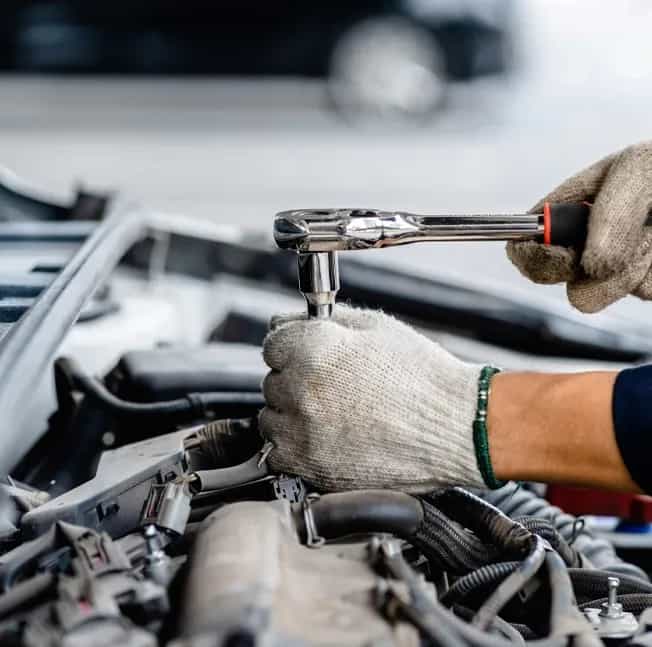
When it comes to selecting an oil seal, precision and quality are paramount. An oil seal is more than just an accessory; it is a vital component that protects against dirt, moisture, and other contaminants. In industries ranging from automotive to manufacturing, the choice of an oil seal significantly affects the machinery's efficiency and durability.
The numbers 35 72 10 are essential identifiers that help you select the exact fit for your equipment. The inner diameter of 35mm must precisely conform to the shaft to provide a perfect seal without any leakage. This specific size ensures that the rotary shaft is well-protected, preventing any unwanted particles from entering the system.
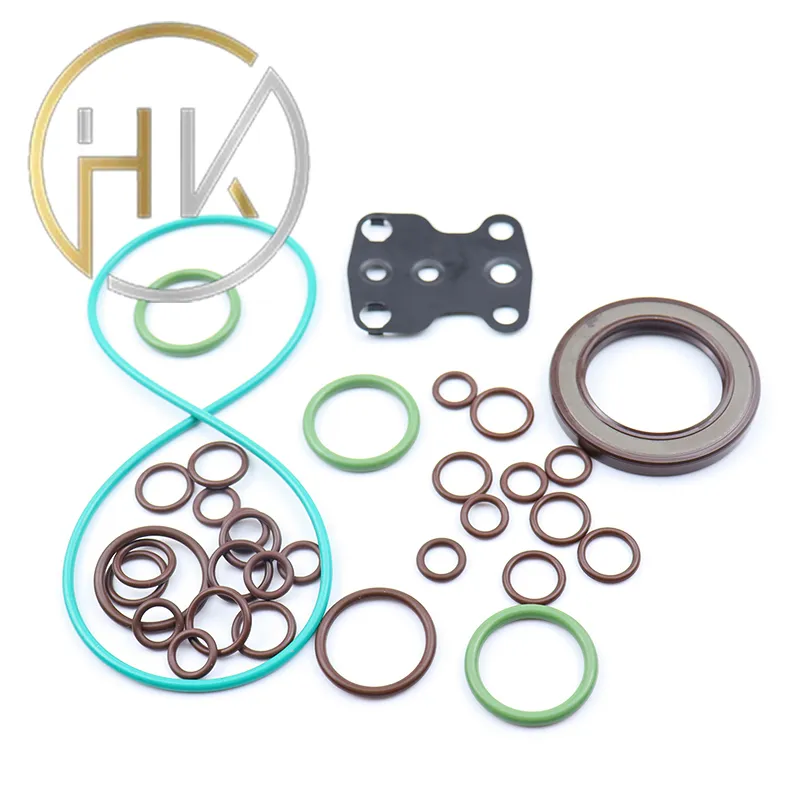
For the outer diameter of 72mm, it requires compatibility with the housing or bore into which it is installed. Therefore, understanding the outer specifications helps in achieving an airtight fit, which is critical for optimal performance and longevity of the machinery.
The 10mm width is equally important as it contributes to the overall pressure-retaining capabilities of the seal. A mismatch in this dimension could lead to swelling or premature failure when the pressure reaches critical levels during operation.
Beyond specifications, expertise in the material selection of the oil seal can dramatically affect performance. Typically crafted from high-grade nitrile rubber, or for more demanding applications, fluoroelastomers, these materials offer resistance to temperature variations and aggressive chemicals, ensuring reliability under extreme conditions. Industry experts often emphasize the importance of selecting the correct material tailored to specific environmental conditions, thereby enhancing the seal's lifespan and effectiveness.
35 72 10 oil seal
Authoritativeness in choosing the right oil seal comes from understanding not just the dimensions but also how these seals perform in real-world applications. Technical reviews and field tests have consistently shown that high-quality seals perform better under stress, keeping friction at bay and thus reducing wear and tear.
Trustworthiness in a product like the [35 72 10 oil seal] is visible in its adherence to industry standards. Reputable manufacturers often ensure that their products meet international quality benchmarks, and seasoned engineers advocate for sourcing oil seals from providers with proven quality assurance protocols.
The use of precision-engineered seals has been validated through rigorous testing, ensuring they perform efficiently in dynamic environments. As experienced users attest, integrating the appropriate seal leads to enhanced machine efficiency, reduced maintenance costs, and prolonged life cycles.
Despite the technical nature of oil seals, the focus remains on hands-on experience — understanding how to measure, install, and maintain these components significantly contributes to system reliability. Engaging with professionals or manufacturers who specialize in oil seals can offer additional insights that go beyond basic technical specifications.
In conclusion, while the numbers [35 72 10] might seem insignificant, they hold the key to finding an oil seal that provides seamless operation and protection. By combining expertise in materials, technical specifications, and industry standards, professionals can ensure that the machinery functions efficiently and remains protected against the challenges of everyday use.