Choosing the right oil seal for machinery, especially in the numerical range such as 22 35 7 oil seal, involves a nuanced understanding of its technical specifications and application dynamics. An oil seal is indispensable in preventing leakage of lubricants while simultaneously aiding in the detainment of contaminants. Understanding these seals’ comprehensive attributes can catalyze machine efficiency and durability.
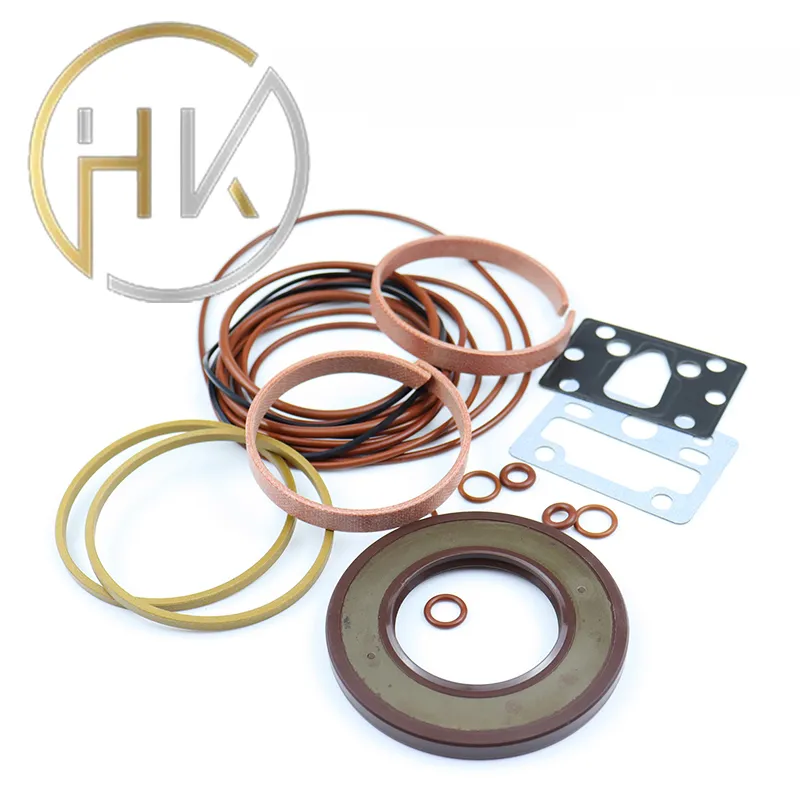
First,
consider the material. Typically crafted from nitrile rubber, Viton, or silicone, the material composition of the oil seal significantly impacts its performance relative to environmental variables and mechanical constraints. Nitrile rubber, for instance, is renowned for its compatibility with a wide array of lubricants and resistance to wear, making it a popular choice in industries where high durability is essential. The decision extends beyond base compatibility; it involves evaluating the operational temperature range. For 22 35 7 oil seals, which often feature an inner diameter of 22mm, an outer diameter of 35mm, and a thickness of 7mm, selecting materials that endure variable thermal expansions is critical.
Next, honing in on the applications reveals their indispensability across multiple sectors. Manufacturing equipment, automotive industries, and heavy machinery invariably rely on this dimension for its versatility. This particular size provides an optimal balance between strength and flexibility, ensuring both static and dynamic sealing performance. Its prevalence in automotive crankshafts and gearboxes highlights its efficacy in reducing oil spillage and contamination, which are notorious for causing mechanical failures.
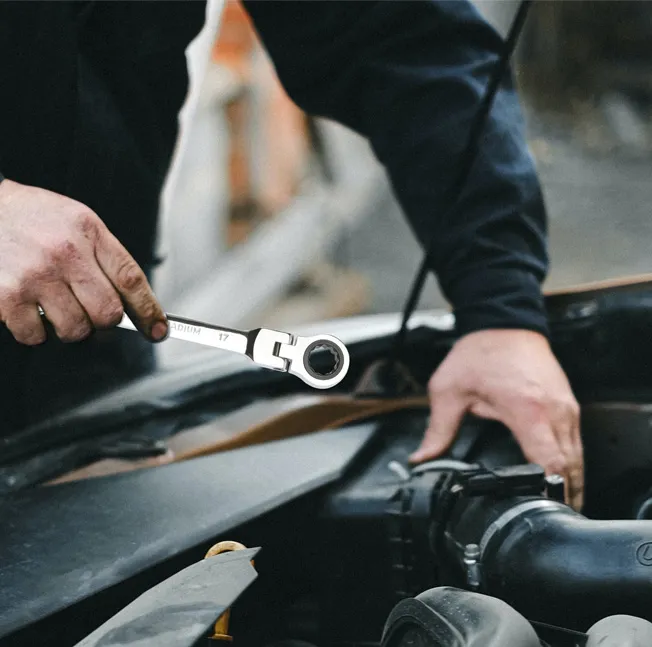
Inspection and maintenance of oil seals are paramount for maintaining operational integrity. Routine checks for any visible wear or tear avert catastrophic failures. An ill-fitted oil seal or one showing signs of degradation can lead to unwanted downtime or costly repairs. Developers and engineers should remain vigilant, monitoring for fluctuations in pressure or temperature that may inadvertently compromise seal integrity.
22 35 7 oil seal
Drawing from expert experience, incorporating oil seal enhancements via advanced surface treatments has shown to significantly extend lifespan. Techniques like plasma nitriding, for instance, impart an enhanced protective layer vastly improving resistance to friction and heat. Such professional interventions, though requiring upfront investment, promise a substantial reduction in long-term maintenance costs.
Trustworthiness in selecting 22 35 7 oil seals is fundamentally rooted in choosing reputable manufacturers. Brands with established credibility provide assurance through stringent quality control standards and certifications. These quality markers are not merely procedural; they ensure each product meets the rigorous demands specific to its intended application, thus forming a cornerstone of reliability. Engaging with experienced suppliers and utilizing their technical support further augments the selection process, enabling tailor-fit solutions.
Efficiency-driven industries stand to benefit significantly from thoughtful oil seal selection and applications. By leveraging expertise in mechanical dynamics and material sciences, informed decisions can significantly enhance the performance and longevity of machinery. Building authoritative knowledge in this niche area of product expertise anchors all ensuing technical decisions, establishing a robust framework for continual enhancement of machinery functionality.
In the grand scheme, staying abreast of innovations and emerging technologies in seal design and materials will serve as a competitive advantage. Whether through seminars, white papers, or manufacturer workshops, updating technical know-how ensures alignment with industry-leading practices, securing operational efficacy that transcends conventional expectations.