In the realm of mechanical engineering and maintenance, the 14x24x6 oil seal emerges as a small yet indispensable component, revered for its prowess in ensuring efficient machinery operation. As an expert in this field with years of hands-on experience, the significance and nuanced functionality of this seemingly modest product become remarkably evident.
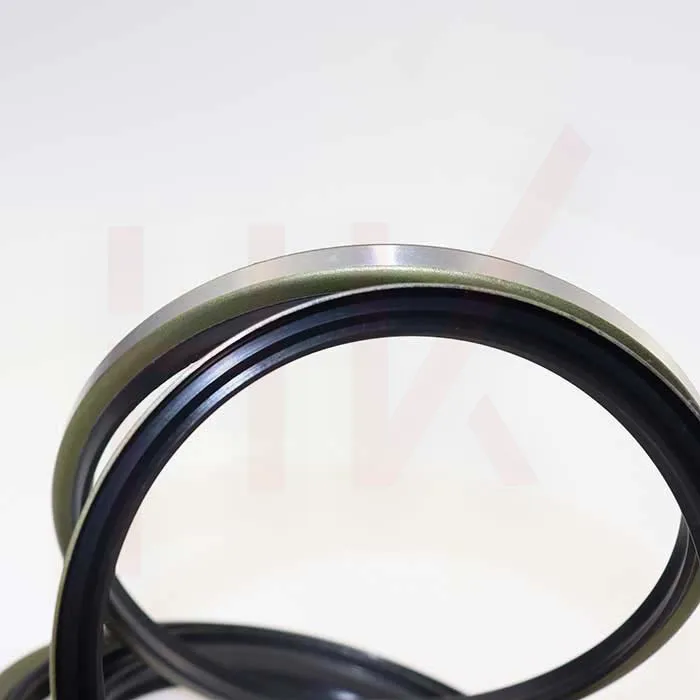
The 14x24x6 oil seal, characterized by its dimensions of 14mm inner diameter, 24mm outer diameter, and a 6mm width, holds a crucial role in preventing lubricant leakage and contaminants infiltration. This specific size is often employed across various industries, including automotive, aerospace, and manufacturing, due to its versatility and reliability in safeguarding rotating and reciprocating shafts.
This oil seal acts as a guardian at the interface of moving and stationary parts. Its construction typically involves high-quality nitrile rubber, Viton, or silicone, materials chosen for their durability and resistance to intense temperatures and harsh chemicals. Such resilience renders the 14x24x6 oil seal ideal for environments subjected to fluctuating thermal exposures and chemical interactions, where lesser materials might falter.
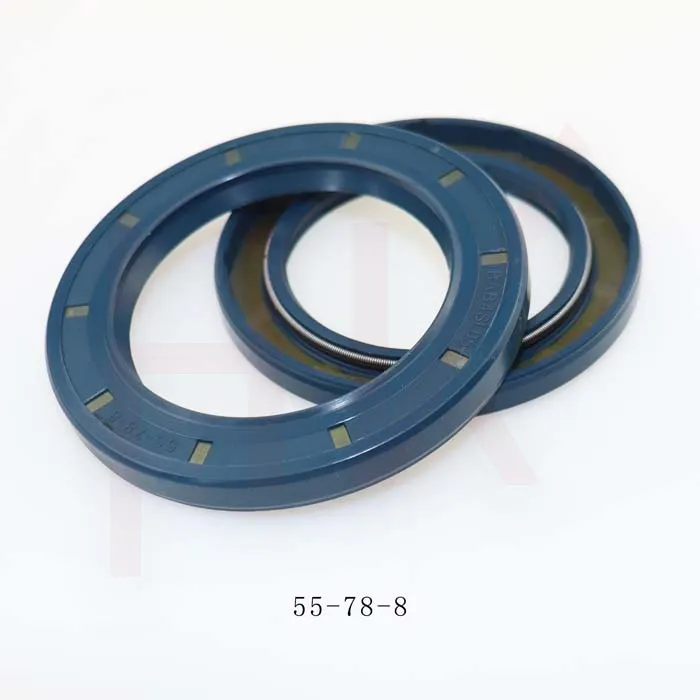
From an experiential perspective, meticulous installation of the 14x24x6 oil seal is pivotal. Errors during assembly can precipitate premature wear or complete system failure. Ensuring that the shaft surfaces are clean and undamaged before fitting the seal is fundamental to maintaining its longevity. Applying a thin layer of lubricant on the sealing edge can enhance installation ease and initial wear resilience, enabling the seal to function optimally from the outset.
Expertise in selecting the appropriate oil seal variant—single lip, double lip, or with an auxiliary dust lip—depends on the specific application requirements. Single-lip seals might suffice for standard conditions, whereas double-lip seals offer enhanced protection against contaminants, often necessary in gritty or dusty environments. This nuanced choice, when made with precision, bolsters the seal's efficiency and extends its service life, thereby enhancing the overall machinery performance.
14x24x6 oil seal
Authoritativeness in understanding and deploying the 14x24x6 oil seal is underscored by adherence to international quality standards and specifications. Renowned manufacturers ensure their seals undergo rigorous testing to comply with standards such as ISO or DIN, emphasizing quality assurance. This adherence not only validates the seal's performance metrics but also instills confidence in engineers and technicians relying on these seals for critical applications.
Trustworthiness of the 14x24x6 oil seal also hinges on regular maintenance and monitoring. Proactive inspections for signs of wear, such as cracking, hardening, or persistent leaks, can preempt catastrophic failures. Employing advanced diagnostic tools like thermographic cameras or vibration analysis equipment provides deeper insights into a seal's operational health, allowing for strategic maintenance scheduling.
Real-world applications further illustrate the utility of the 14x24x6 oil seal. In the automotive sector, it ensures that engine components operate smoothly by maintaining optimal oil levels and preventing ingress of dirt or moisture. In manufacturing, it stands as a barrier against lubricant loss in assembly lines and heavy machinery, reducing downtime and enhancing productivity.
Through this comprehensive understanding of the 14x24x6 oil seal, it becomes evident that its contribution is far from trivial. For those immersed in fields where machinery efficiency and reliability are paramount, the oil seal offers an unsung yet invaluable solution. Choosing, installing, and maintaining it with precision can significantly enhance the performance and lifespan of sophisticated mechanical systems, underscoring its essential role within the broader industrial landscape.