Wiper seals are unsung heroes in the realm of hydraulic and pneumatic systems, quietly performing critical functions that extend the lifespan and efficiency of machinery. Their role might seem insignificant to the untrained eye, but for industry professionals who have spent years troubleshooting and optimizing machinery, wiper seals are fundamental components that demand respect and attention.
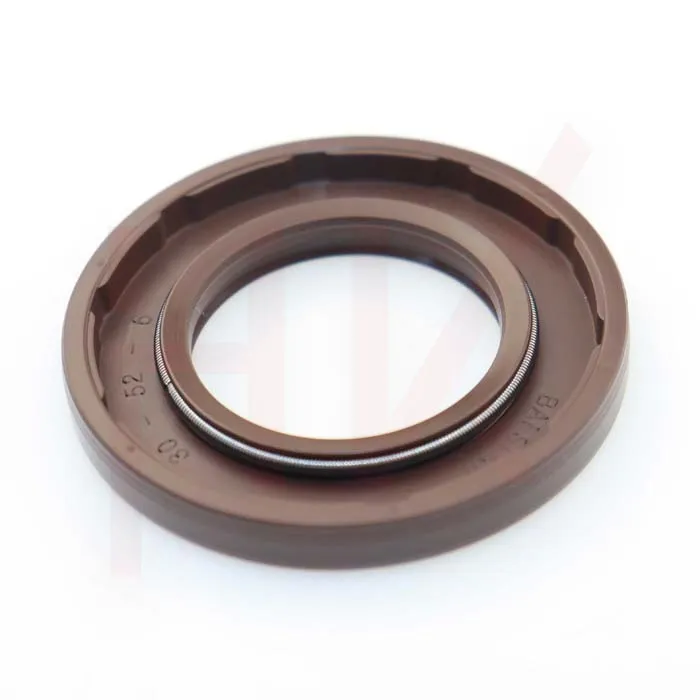
Experience has shown that selecting the appropriate wiper seal is far from a one-size-fits-all task. Industrial machinery operates under a spectrum of conditions, often harsh and varied, and each scenario dictates a different set of requirements for seal performance. For example, consider the multitude of environments an excavator might encounter—from muddy, wet conditions to dry, dusty plains. The wiper seals for its hydraulic cylinders must be formulated to endure constant exposure to abrasive particles while preventing contaminants from breaching the hydraulic system. A missed or inappropriate seal can lead to frequent breakdowns, increased operational costs, and, ultimately, reduced machinery lifespan.
The expertise of seasoned engineers comes into play in identifying the right materials and designs needed for specific applications. Common materials such as polyurethane and nitrile rubber are chosen for their robustness and flexibility. However, it is the subtle engineering nuances—such as the shape and profile of the seal lips—that make a significant difference in performance. For instance, a dual-lip wiper seal might be imperative in scenarios where additional spatial constraints are imposed, offering superior dust exclusion capabilities combined with minimal friction.

wiper seals
Authoritativeness in the subject of wiper seals is often derived from hands-on experience and rigorous application testing. Manufacturers who prioritize state-of-the-art research and development in seal technology provide comprehensive product data that includes empirical testing under simulated real-world conditions. Such diligence is not merely academic; it translates directly to user confidence. Companies like SKF and Parker Hannifin often lead the way with innovative designs that go through exhaustive testing processes to ensure durability and performance. These tests factor in variables like speed, pressure, temperature, and chemical compatibility to offer solutions that meet or exceed industry standards.
Trustworthiness in choosing the right wiper seals is vital, especially considering the cost implications of machinery breakdowns. Trusted suppliers often provide warranties and technical support as part of their service package, underscoring their confidence in their products. The provision of detailed installation guides, along with training for maintenance personnel, can further enhance the lifespan of the seal and the equipment it protects. This customer-centric approach builds a reputation of reliability and fosters long-term relationships between suppliers and clients.
In conclusion, the significance of wiper seals extends beyond their apparent simplicity. They are critical components that ensure the smooth operation of machinery across various industries. Choosing the right wiper seal requires a blend of experience and expertise, supported by authoritative product information and a foundation of trust with reliable suppliers. As industrial demands continue to evolve, the role of wiper seals will undoubtedly expand, underscoring their importance in maintaining operational efficiencies and safeguarding equipment investments. Understanding the intricate balance between design, material selection, and application environment is essential for maximizing the performance and longevity of wiper seals, ultimately contributing to more sustainable industrial practices.