The wiper seal in hydraulic cylinders is a critical component that preserves the integrity and performance of the entire hydraulic system. As experts in the field have emphasized, understanding the intricacies of wiper seal functionality prevents both immediate and long-term operational inefficiencies. Renowned manufacturers often refer to these seals as the first line of defense against environmental contaminants.
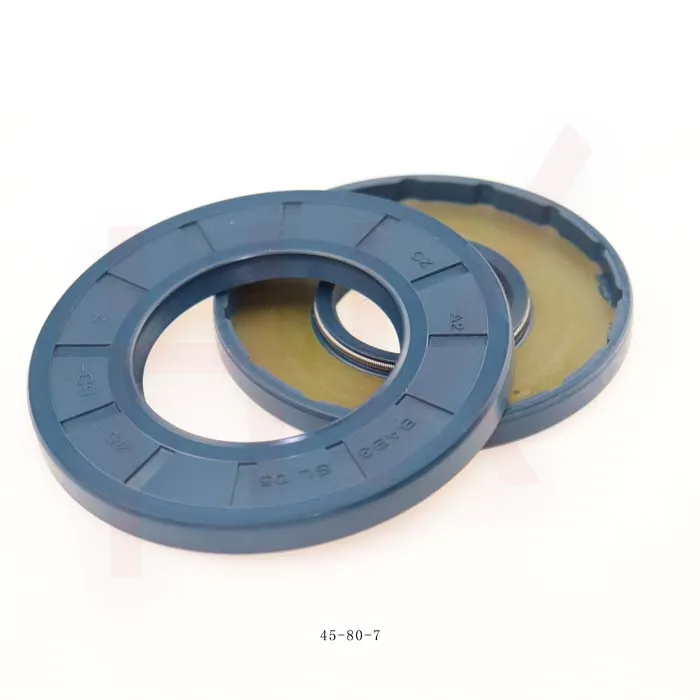
Experience tells us that hydraulic cylinders often operate in harsh environments, including construction sites, agricultural fields, and industrial settings, where dust, water, and debris abound.
The wiper seal plays an indispensable role here. Its primary function is to prevent dirt particles from entering the cylinder assembly. Without this protection, foreign substances could compromise the seal integrity of other components, leading to premature failure. Seasoned hydraulic technicians frequently recount extensive instances where a neglected or poorly selected wiper seal led directly to costly downtime and repairs.
From a professional perspective, the design and material selection of a wiper seal are paramount to its success. High-quality wiper seals typically consist of materials like polyurethane or nitrile rubber, chosen specifically for their durability and resilience in diverse environments. These materials are noted for their excellent abrasion resistance and elastic properties. Recent studies highlight that polyurethane wiper seals, in particular, offer superior resistance to wear and intermittent contact with aggressive chemicals often encountered in heavy-duty applications.
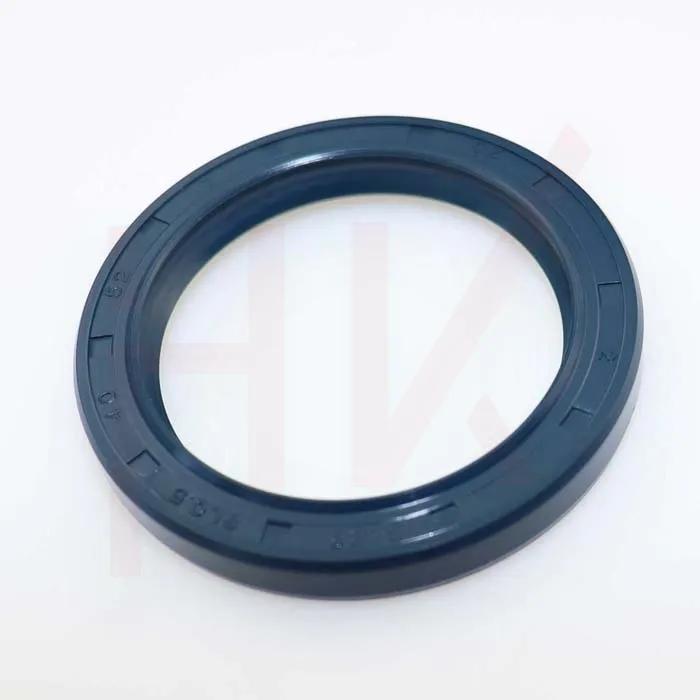
Authoritative sources in hydraulic engineering assert that the selection of a wiper seal must be based on several key factors—operating temperature, speed, and compatibility with hydraulic fluids. Industry standards often advise consulting with mineral oil-based or synthetic oil specialists to ensure that the chosen seal material can withstand the particular type of fluid exposure. Moreover, the design configuration, whether lip- or V-ring wiper seals, should align with the cylinder’s specific application needs, carefully balancing coverage and friction reduction.
wiper seal hydraulic cylinder
Establishing trustworthiness in this specialized field requires a comprehensive approach. End-users and maintenance teams rely on certified products that undergo rigorous testing and quality assurance protocols. Top manufacturers of hydraulic cylinder components often hold certifications such as ISO 9001, which guarantees that their products have met stringent quality standards. These companies often provide detailed documentation and testing results, making them a trusted choice for end-users worldwide.
In practice, installing a wiper seal necessitates attention to detail and precision. Experienced maintenance engineers will often emphasize ensuring the cleanliness of the cylinder and proper lubrication during installation to mitigate installation-related issues. Training programs from trusted hydraulic component suppliers are frequently recommended, as they equip technicians with the technical knowledge required for proper seal fitment and longevity.
In summary, the effectiveness of a hydraulic cylinder heavily depends on the flawless operation of its wiper seal. Drawing from real-world applications and expert insights, businesses are encouraged to invest in high-quality wiper seals as part of their overall hydraulic system strategy. By prioritizing such seals, operators can significantly enhance system reliability, lifespan, and performance, leading to greater productivity in their respective fields.