When dealing with hydraulic and pneumatic systems, ensuring the longevity and efficiency of machinery components is crucial. One component that plays a critical role in these systems is the wiper seal. A wiper seal, also known as a scrapper seal, serves as the first line of defense against contaminants, safeguarding the inner workings of machinery by preventing dirt, dust, and other foreign particles from entering the system. This article delves into the intricacies of wiper seals, blending experiential insights with professional knowledge to emphasize their importance and functionality.
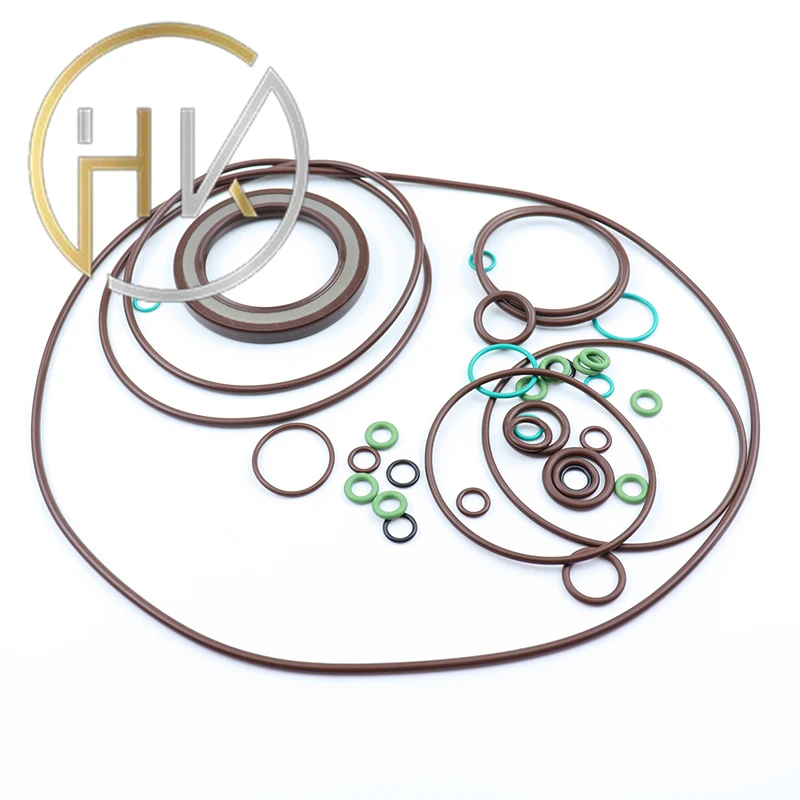
Understanding wiper seals requires a fundamental grasp of their role in systems where fluid dynamics are pivotal.
Primarily used in cylinders, these seals are tactically positioned at the interface where the rod exits the cylinder. The seal's principal function is to scrape off external debris from the rods as they retract, ensuring that the integrity of the internal environment is uncompromised. Without wiper seals, the risk of contaminants infiltrating and damaging the cylinder is significantly increased, which could lead to mechanical failures or costly maintenance.
From an expert standpoint, selecting the right wiper seal demands an understanding of the application environment and operational conditions. Factors such as temperature, pressure, speed, and the types of contaminants are crucial in determining the most suitable material and design for a seal. Wiper seals are commonly fashioned from materials like polyurethane, nitrile rubber, or polytetrafluoroethylene (PTFE), each offering distinct advantages. For instance, polyurethane is renowned for its robust wear resistance and is ideal for applications requiring durability across various temperatures. Conversely, PTFE offers remarkable chemical resistance, making it the preferred choice in environments exposed to aggressive substances.

In terms of authority, industry standards often dictate the specifications and materials used for wiper seals to ensure reliability and performance. Reputable manufacturers adhere to rigorous standards such as those set by the International Organization for Standardization (ISO) and the American Society for Testing and Materials (ASTM). These standards ensure that wiper seals not only meet performance expectations but also comply with safety and quality benchmarks. Partnering with recognized suppliers and manufacturers can enhance trustworthiness, as they provide seals that are tested and proven to meet industry demands.
wiper seal
Trust in wiper seal performance is further reinforced through real-world applications and testimonies from seasoned engineers and maintenance professionals. An effective wiper seal can drastically reduce the frequency of system downtimes and maintenance costs, as demonstrated in various industrial case studies. For example, a manufacturing firm that produces heavy machinery experienced a significant reduction in hydraulic cylinder maintenance after upgrading to seals made from advanced composite materials. This switch not only improved their machinery's uptime but also extended the service life of the hydraulic components, showcasing the tangible benefits of investing in superior wiper seals.
Maintaining the efficiency and safety of hydraulic and pneumatic systems is a multi-faceted challenge that hinges on the reliability of components such as wiper seals. As the unsung heroes of contamination control, their impact on system longevity and performance cannot be overstated. By understanding the nuances of wiper seal selection and application, industries can optimize their machinery operations, minimize downtime, and ensure a safer working environment.
Evidently, the wiper seal is an indispensable component, integral to ensuring the seamless function of hydraulic and pneumatic systems. Harnessing the expertise of industry professionals and adhering to authoritative standards empowers businesses to make informed decisions about their system components. Through experience and expertise, wiper seals have proven their worth, securing their position as a critical element in modern industrial machinery.