Oil seals, often overshadowed by more complex machinery components, play a crucial role in ensuring the smooth operation and longevity of mechanical systems. As components that prevent the escape of lubricants and keep contaminants out, oil seals are indispensable parts of automotive, manufacturing, and many other industries. Here, we delve into their functions, their importance, and how they effectively contribute to machinery performance.
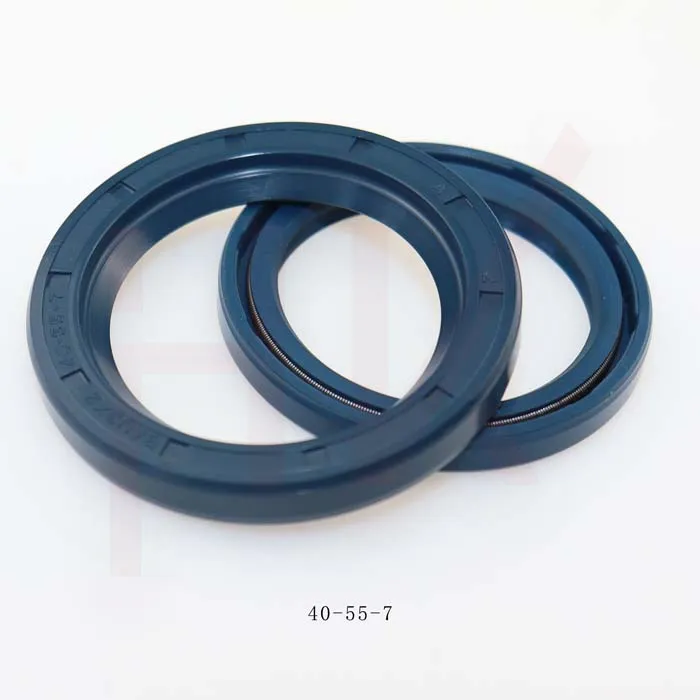
Oil seals, also known as rotary shaft seals, lip seals, or grease seals, primarily function to protect lubricated parts in machinery from contamination. By preventing the leakage of lubricants such as oil or grease and barring entry to dust, dirt, and other debris, oil seals ensure the effective functioning and longevity of the equipment. This protection is vital in preventing premature wear and tear, which can lead to costly repairs and downtime.
One of the primary functions of the oil seal is to maintain the necessary lubrication level in engines and machines by preventing the leakage of lubricants. This helps in reducing the friction between rotating components and minimizes wear, ensuring efficient operation. Lubricants are vital in any mechanical system, reducing the overall temperature and facilitating the smooth operation of moving parts. Oil seals maintain this delicate balance, ensuring no excess lubricant is lost which could otherwise lead to the overheating of parts and eventual mechanical failure.
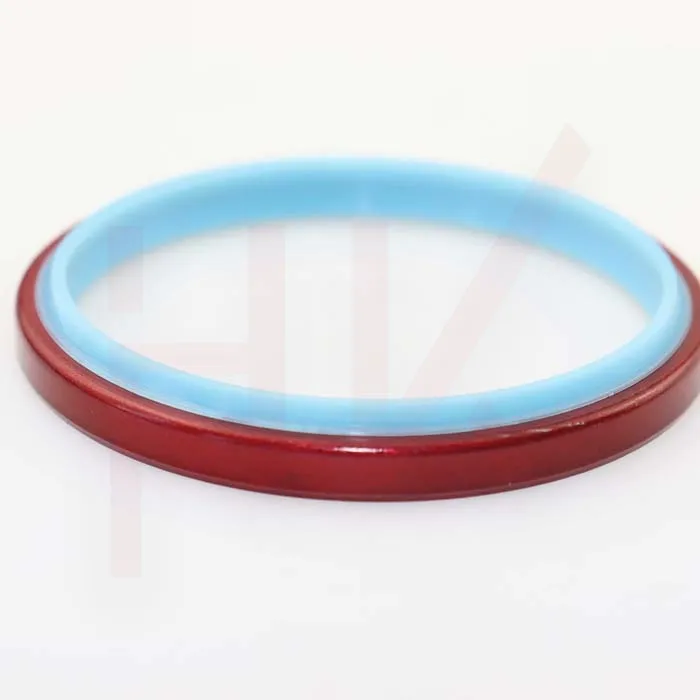
Another key function of oil seals is contamination control. Operating environments can be harsh, with dust, dirt, and other debris readily available to infiltrate sensitive components. An oil seal effectively acts as a barrier, preventing such contaminants from entering the machinery. When contaminants enter the system, they can cause abrasive wear and corrosion, significantly reducing the lifespan of machinery components. Therefore, the role of the oil seal in preventing contamination cannot be understated.
In complex machinery where components need to work in tight, precise tolerances, the role of oil seals becomes even more critical. Oil seals maintain the necessary working environment within these components by ensuring the insides remain unaffected by external factors. Machines used in precision industries like aerospace or electrical have narrow room for error, and maintaining an optimal operating environment is crucial—functions guaranteed by high-quality oil seals.
what is the function of oil seal
The effectiveness of oil seals also lies in their construction and materials used. Commonly constructed from a range of materials including rubber, Teflon, or silicone, oil seals are designed to withstand high temperatures, high pressures, and chemically-aggressive environments. Depending on the application, the choice of material is paramount to ensure the oil seal performs its intended function over its lifespan. Selecting the right seal, therefore, can provide significant benefits in terms of system reliability and performance.
Moreover, oil seals also contribute to the efficient use of resources. By ensuring that lubricants do not leak unnecessarily, they help in conserving these materials, contributing to both economic and environmental sustainability. Given the increasing awareness and regulatory constraints on environmental issues, the role of oil seals in preventing leakage is also linked to reducing environmental impact.
For industries requiring compliance with strict safety and environmental regulations, maintaining equipment reliability through effective sealing solutions is critical. Oil seals are a cost-effective way to manage these requirements, often being the unsung heroes in large-scale operations such as manufacturing plants, where downtime and repairs can wield significant costs.
Research and development in the field of oil seal technology is ongoing, focusing on creating seals with higher resistance to extreme conditions, longer lifespans, and improved performance characteristics. Novel materials and manufacturing techniques are being explored to meet the ever-growing demands of diverse industries.
In conclusion, while simple in design, oil seals represent a vital component in various mechanical systems. By effectively sealing lubricants and preventing the ingress of contaminants, they play a crucial role in maintaining equipment efficiency, durability, and reliability. Understanding their importance and selecting the appropriate oil seal can lead to substantial savings in maintenance and resource consumption while ensuring compliance with stringent operational standards.