Oil seals, sometimes known as shaft seals, rotary seals, or lip seals, play a critical role in the functionality and longevity of machinery across various industries, including automotive, aerospace, manufacturing, and more. These components are designed to protect and equip machinery to operate at optimum efficiency by preventing leaks, contaminants, and maintaining necessary lubrication.
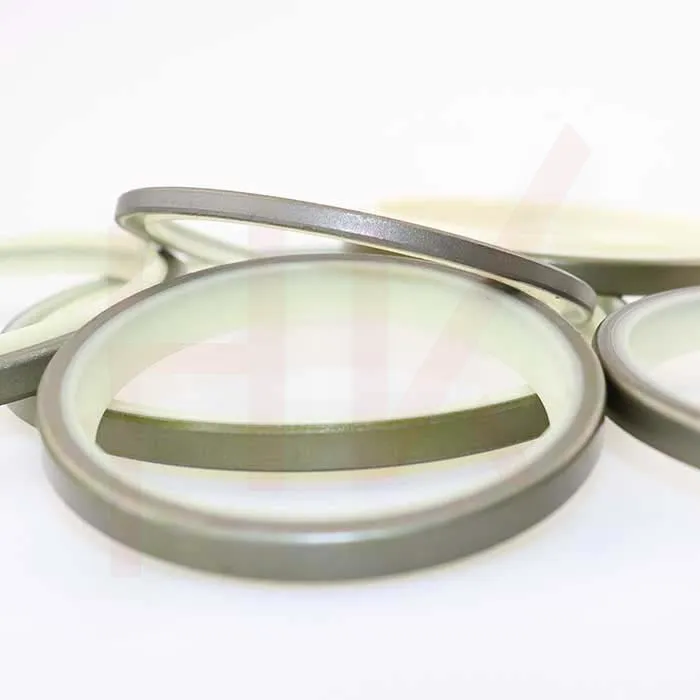
At the heart of the oil seal's function is its ability to separate different substances. In engines and gear systems, for instance, oil seals serve the pivotal function of keeping lubricants inside while simultaneously preventing contaminants such as dirt, dust, and water from entering and causing potential damage. This dual action is crucial for maintaining the integrity of the mechanical system, and preventing any malfunction or wear due to foreign matter intrusion.
A typical oil seal comprises three essential parts the sealing element, metal case, and spring. The sealing element is often made from elastomers like nitrile rubber or silicone, providing flexibility and resistance to chemicals and temperature fluctuations. The metal case gives structural stability to the seal, while the spring ensures consistent pressure is applied against the shaft, maintaining a tight seal.
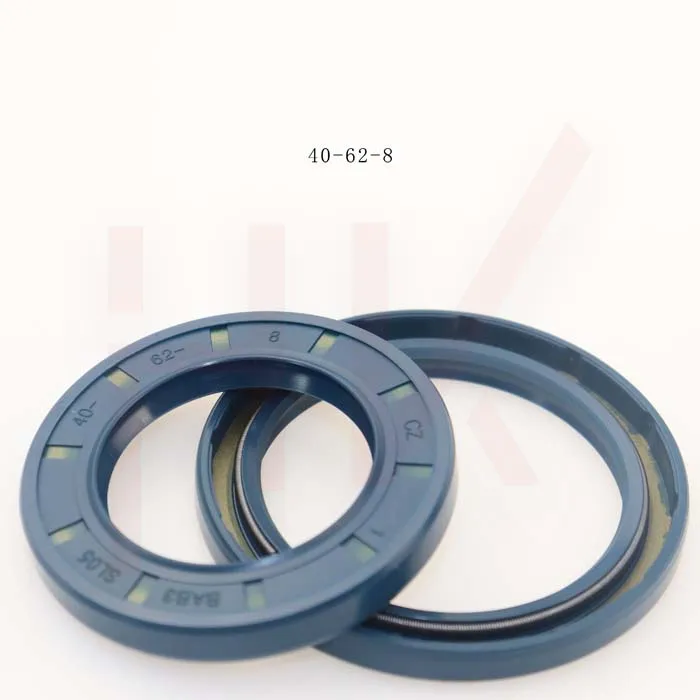
Real-world applications of oil seals highlight their significance. In an automotive engine, for instance, oil seals are responsible for ensuring that engine oil does not leak from the crankshaft or timing cover, thereby safeguarding other engine components. By maintaining oil circulation, these seals contribute to the engine’s efficiency and longevity, indirectly influencing vehicle performance and fuel economy.
Furthermore, in the industrial sector, machinery and manufacturing equipment heavily rely on oil seals for sustained operation. In a production line, oil seals are crucial for the smooth operation of rotating shafts and gears that might otherwise suffer from lubrication loss or contamination. Regular inspection and replacement of oil seals can prevent unscheduled downtime and costly repairs, underscoring their indirect impact on operational efficiency and profitability.
what is the function of oil seal
The expertise involved in selecting the right oil seal cannot be understated. A mismatch in size or material may lead to premature seal failure, leading to potential equipment damage or safety hazards. Therefore, knowledge of operating conditions, including shaft speed, temperature, and chemical exposure, is vital when choosing an oil seal. Consulting with manufacturers or utilizing engineering expertise ensures that the chosen seal meets the application requirements.
Trustworthiness and authoritativeness in this domain stem from understanding that while oil seals might appear as minor components, their failure can lead to significant mechanical issues. Ensuring regular maintenance, recognizing early wear or damage signs, and replacing oil seals promptly can mitigate risks. Companies often rely on certified professionals and quality manufacturers to provide reliable oil seals that comply with industry standards.
Emerging technologies are continually pushing the boundaries of oil seal capabilities. Advancements in material science are enhancing oil seal materials, providing greater resistance to heat, pressure, and chemicals. Additionally, innovations in design are improving seal efficiency, decreasing friction losses, and extending service life. Staying informed about these advancements allows businesses to adopt newer, more efficient oil seals that support more sustainable operations.
In conclusion, oil seals are unsung heroes in ensuring mechanical systems' operational efficiency and longevity. Their role in maintaining lubrication and preventing contamination is indispensable across various industries. By leveraging expertise in selecting the right seals and keeping abreast of technological advancements, businesses can rely on these critical components to operate efficiently and cost-effectively. The attention to detail in maintenance and understanding of oil seal importance reflects a commitment to operational excellence and reliability.