Investing in quality components is crucial for ensuring the longevity and efficiency of industrial machinery. Among these components, the skeleton oil seal plays a pivotal role, albeit one that is often overlooked. Designed to prevent the leakage of lubricants and block contaminants, the skeleton oil seal is the unsung hero of machinery maintenance and efficiency.
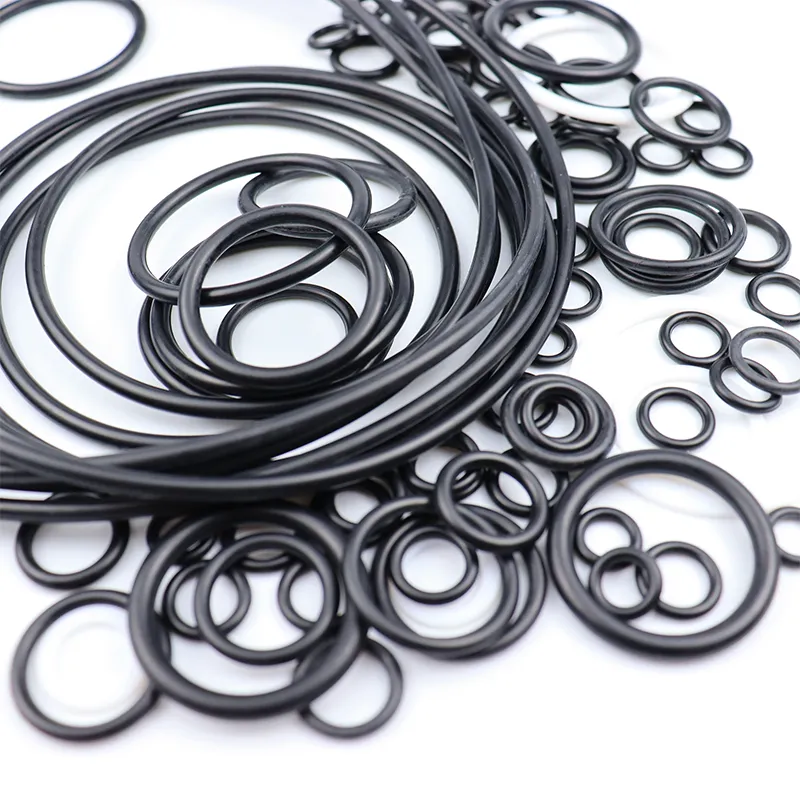
With over 15 years of experience in the field of machinery maintenance and optimization, I have witnessed firsthand the transformative impact that a well-chosen skeleton oil seal can have on operational efficiency. These seals form a crucial barrier between the moving and static parts of machinery, enabling smooth operation by maintaining lubrication levels and preventing foreign matter ingress.
Expertise in material selection for oil seals is essential. High-quality skeleton oil seals are typically crafted from durable materials such as nitrile rubber, fluoroelastomers, or silicone, each selected based on specific operational requirements such as temperature ranges and exposure to chemicals. For instance, fluoroelastomers are highly resistant to heat and chemical degradation, making them suitable for high-temperature environments. On the other hand, nitrile is more cost-effective and ideal for general purpose applications with lower thermal demands.
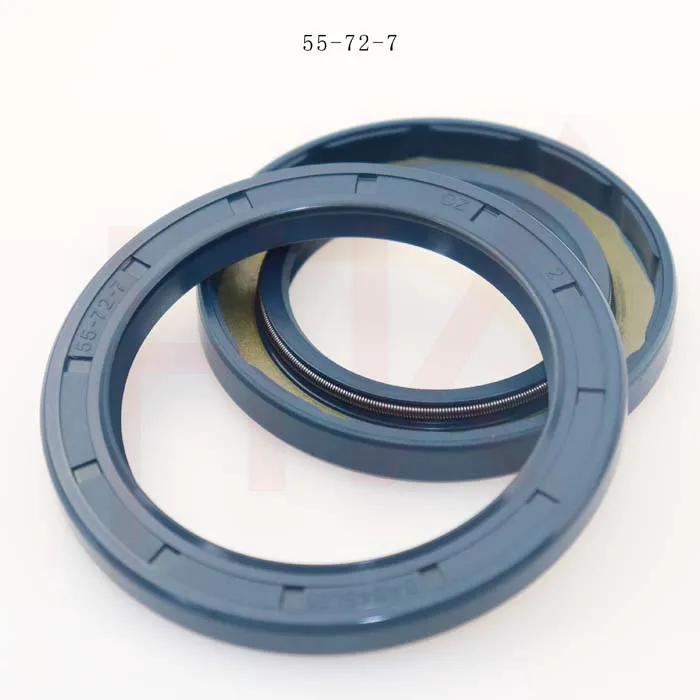
Understanding the mechanics of skeleton oil seals can significantly enhance their utility. Designed for easy installation, these seals often include features like a spring-loaded lip that maintains contact with the rotating shaft to ensure a tight seal over time. This spring mechanism compensates for any minor wear, ensuring consistent performance without the need for frequent adjustments or replacements.
Authoritative studies conducted on equipment maintenance have consistently shown that superior sealing solutions can reduce maintenance costs by up to 30%. These reductions stem from decreased lubricant consumption, less frequent repairs, and minimized downtime, all contributing to significantly lowered operational expenses. Regular monitoring and proactive replacement of worn seals can avert costly machinery failures and production halts.
skeleton oil seal
Trustworthiness in product choice begins with sourcing from reputable manufacturers who adhere to stringent quality control processes. Reliable manufacturers provide seals that are rigorously tested for resilience against environmental stressors, guaranteeing performance that aligns with industry standards. When selecting suppliers, one should prioritize those with positive customer feedback, industry certifications, and histories of consistent product excellence.
Notably, as industries advance towards predictive maintenance models, integrating condition-monitoring technology with skeleton oil seals is becoming increasingly prevalent. By equipping seals with sensors that detect wear and performance indicators, businesses can anticipate maintenance needs, thus optimizing machinery lifespan and functionality.
In conclusion, coupling professional expertise with the selection of the right skeleton oil seal can significantly impact machinery efficiency and operational costs. Prioritizing quality and performance-enhancing features over initial expenditures can yield long-term savings and performance benefits. The right seal protects more than just the lubricant; it shields the entire machinery from potential failures and inefficiencies, ensuring a seamless operational experience. Embrace the integration of intelligent technologies with durable materials to stay ahead in the ever-evolving landscape of industrial automation and maintenance.
Remember, your choice of a skeleton oil seal is not just about solving a problem today but preventing a problem tomorrow.