Single lip oil seals, meticulously crafted components often underestimated, play a crucial role in maintaining the efficiency and longevity of various machines. These seals are designed to keep lubricants within and contaminants out, ensuring that machinery operates smoothly and without interruptions.
The art of their functionality lies in their simplicity and effectiveness.
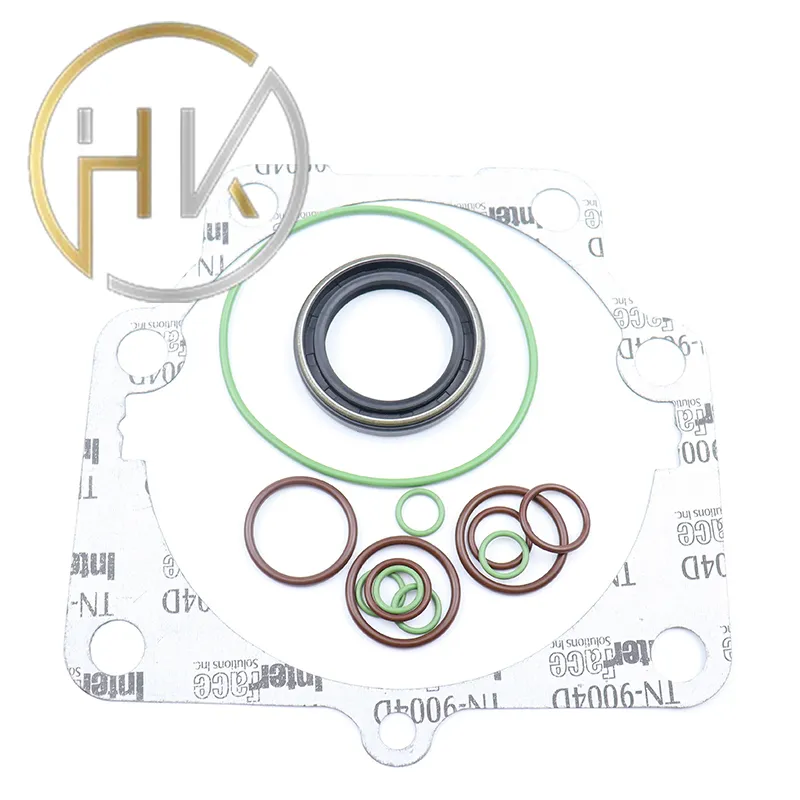
In the realm of industrial machinery and automotive applications, single lip oil seals stand out as essential guardians of performance. They are engineered to combat wear and tear, safeguarding the integrity of critical components. Despite their small size, these seals make a significant impact, acting as the first line of defense against fluid leakages and foreign particles that could compromise mechanical operations.
The design of a single lip oil seal features a flexible lip that closely adheres to a rotating shaft. This lip creates a barrier that securely retains lubricants while preventing contaminants from infiltrating the system. Made from durable materials such as nitrile rubber, silicone, or fluoroelastomer, these seals are versatile enough to function effectively in varied temperature ranges and chemical environments. This versatility underscores their applicability across industries—from automotive to industrial machinery, where maintaining a contaminant-free environment is paramount.
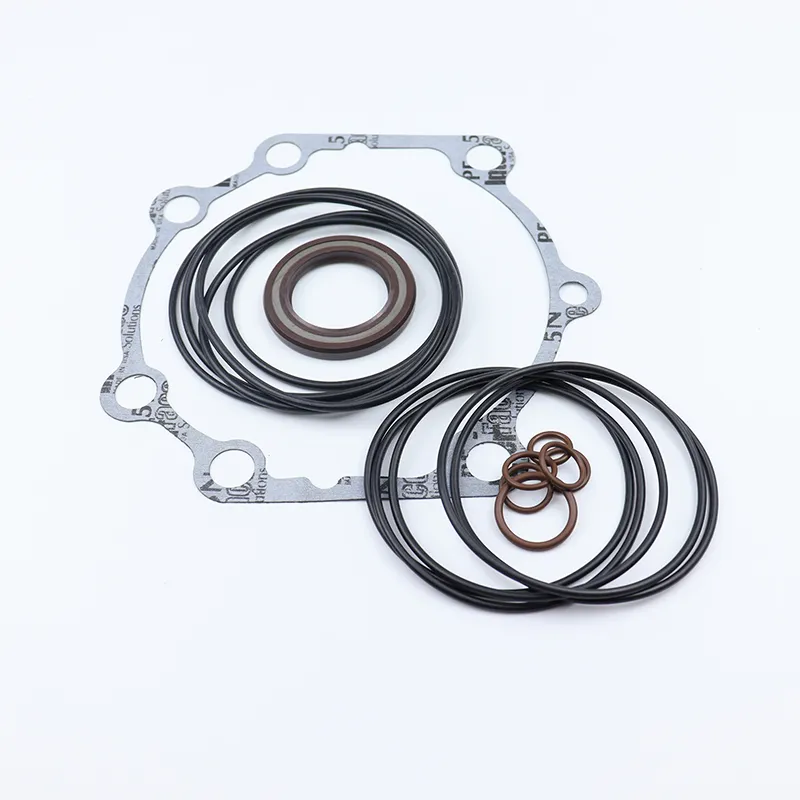
Experience in the field reveals that single lip oil seals are not just plug-and-play components. Their selection demands a nuanced understanding of the operating conditions, including shaft speed, operating temperature, and chemical exposure. For instance, high-speed applications may benefit from seals made from fluoroelastomer due to its excellent resistance to both heat and chemicals. The choice of material can significantly enhance the lifespan and performance of the seal, contributing to reduced maintenance downtime and cost savings.
single lip oil seal
Professional expertise suggests that the installation process of these seals should be handled with precision to maximize their effectiveness. Proper alignment and lubrication during installation help prevent premature wear and ensure optimal contact between the lip and the shaft. Additionally, regular maintenance checks to assess the condition of the seals can preclude potential failures that could lead to costly repairs.
From an authoritative standpoint, adopting quality oil seals from trusted manufacturers ensures a robust defense against mechanical failures. These manufacturers adhere to strict quality control measures, providing products that meet or exceed industry standards. A reputable seal not only reassures the user of its performance reliability but also extends the life expectancy of the machinery by maintaining their operational integrity.
Trustworthiness, a crucial attribute in the industrial supply chain, is bolstered when manufacturers and suppliers provide transparent information about their products' specifications and durability. Moreover, customer testimonials and rigorous testing results add layers of reliability, reinforcing confidence in the product’s capability to perform under specified conditions.
In conclusion, the single lip oil seal, though often overlooked in its critical role, is indispensable for maintaining the functionality and efficiency of machinery. Recognizing the detailed expertise required in selecting and managing these seals can lead to improved mechanical performance and longevity. When chosen and applied correctly, they uphold their promise of durability and protection, proving themselves as vital components within any mechanical system.