The realm of machinery and mechanical engineering hinges on numerous small yet crucial components, one of which is the shaft oil seal. This unassuming part plays a pivotal role in maintaining the efficiency and longevity of various mechanical systems. An effective shaft oil seal is not merely a component; it is a testament to engineering precision designed to prevent leaks, contamination, and potential system failures.
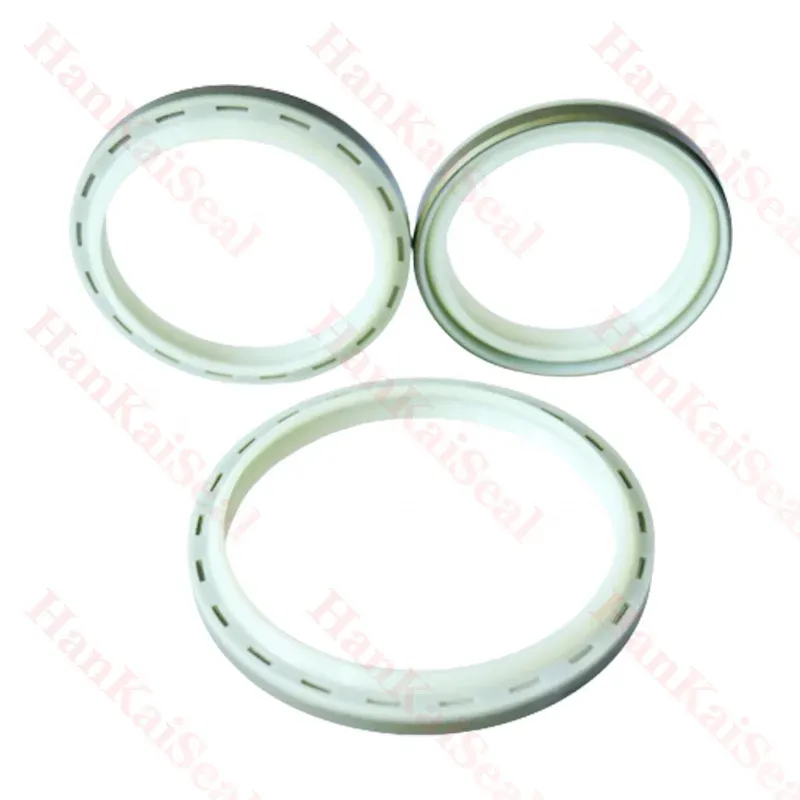
Shaft oil seals, often referred to as rotary shaft seals, are indispensable in industries ranging from automotive to aerospace. Their primary function is to seal the spaces between stationary and moving components in the mechanical assembly. By doing so, they keep lubricants in, while keeping contaminants like dust, dirt, and moisture out. This dual action ensures that the components operate smoothly without unnecessary wear and tear, thus extending the machinery's lifespan significantly.
The quality of a shaft oil seal can make or break the efficiency of an industrial process. High-quality seals are engineered to withstand extreme temperatures, pressures, and continuous movement. They are typically made from durable materials such as elastomers, metal, and plastic to cater to specific industrial demands. For example, seals used in automotive engines need to endure high heat and friction, whereas those in electrical appliances may require resistance against chemicals or electrical conductivity.
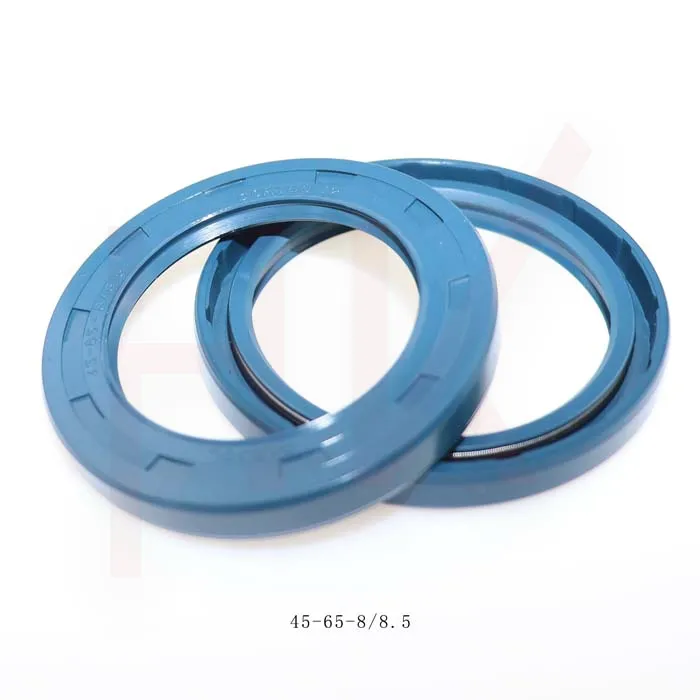
Understanding the dynamics of the environment in which the shaft oil seal will operate is critical for selecting the right product. In automotive applications, for instance, seals must endure high RPMs and fluctuating temperatures, which necessitates a design that can handle thermal expansion and shock. This requires a deep understanding of material science and engineering principles, underscoring the expertise needed in the production of these seals.
shaft oil seal
Not all shaft oil seals are created equal, and it's the deployment of cutting-edge technology in their design and manufacturing that separates the best from the rest. Computer-aided design (CAD) and computational fluid dynamics (CFD) are tools that allow manufacturers to simulate and optimize seal designs for specific applications. This scientific approach ensures that the seal achieves maximum performance across a variety of challenging conditions.
The choice of shaft oil seal impacts not only the equipment's operation but also the overall safety of the industrial ecosystem. A compromised seal can lead to leaks that contaminate the environment or lead to catastrophic equipment failure. Therefore, choosing a manufacturer with a proven track record and adherence to international quality standards is crucial. Industry certifications such as ISO 9001 are indicators of a company’s commitment to quality and precision in its manufacturing processes.
The importance of shaft oil seals also extends to their role in sustainability and cost-effectiveness. Investing in high-quality seals reduces the need for frequent replacements and the associated labor costs, leading to significant savings over time. Moreover, effectively sealed systems are more energy-efficient and environmentally friendly, as they prevent the escape of harmful substances into the environment.
In conclusion, the shaft oil seal is an integral component that ensures the smooth functioning of mechanical systems by preventing leaks and contamination. Its importance is reflected in the precision and expertise required in its manufacturing. From material selection to design optimization, every aspect of a shaft oil seal's production is geared towards achieving reliability and efficiency. The right seal extends equipment life, improves safety, and contributes to sustainable practices in industrial and automotive sectors. This focus on quality and precision not only enhances operational performance but also builds trust and authority in partners, customers, and stakeholders who rely on these small yet crucial components.