Effective management of machinery dependability often hinges on the meticulous specification and maintenance of seemingly minor components like the shaft dust seal. This small yet crucial element plays a pivotal role in safeguarding mechanical systems, enhancing their lifespan and ensuring operational fluidity. Exploring its utility reveals insights into why understanding and selecting the right shaft dust seal is imperative for engineers and maintenance professionals alike.
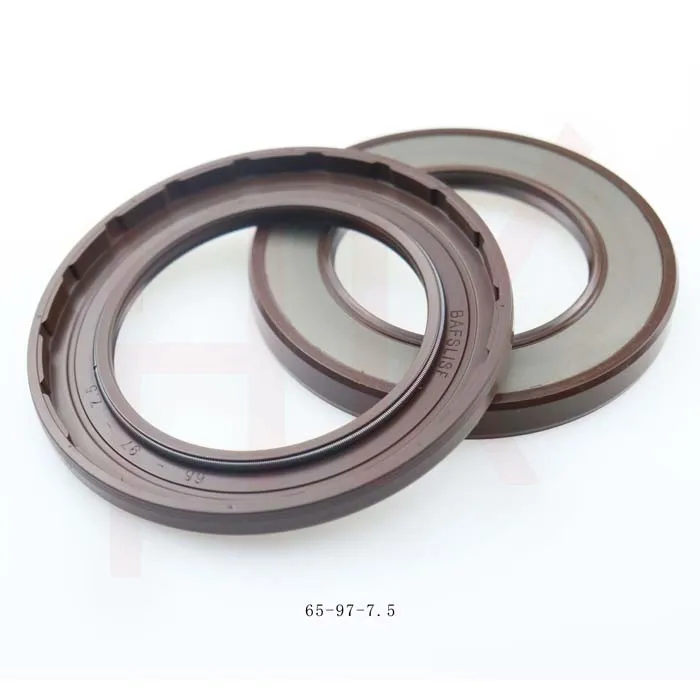
Shaft dust seals are predominantly used to prevent contaminants like dust and dirt from entering a machine's internal environment. For many industrial applications, from automotive engines to manufacturing equipment, the invasion of dust can lead to catastrophic mechanical failures. By crafting a robust barrier, shaft dust seals play a pivotal role in the overall health and efficiency of mechanical systems. Their utility extends beyond merely stopping dirt; they help retain lubricants within the machine, aiding in maintaining the optimal operation temperature and reducing wear and tear on moving parts.
Selecting the appropriate shaft dust seal requires a deep understanding of the operating environment and the specific machine needs. Various materials are part of the seal's manufacturing, each offering certain benefits. Nitrile rubber, for instance, provides excellent resistance to oil and abrasion, making it suitable for hydraulic environments. On the other hand, Viton offers superior high-temperature stability and resistance against chemicals, extending reliability in environments where machines are exposed to harsh substances. Engineers must evaluate the operational conditions — including the temperature range, chemical exposure, and the nature of the motion involved — before selecting the seal material.
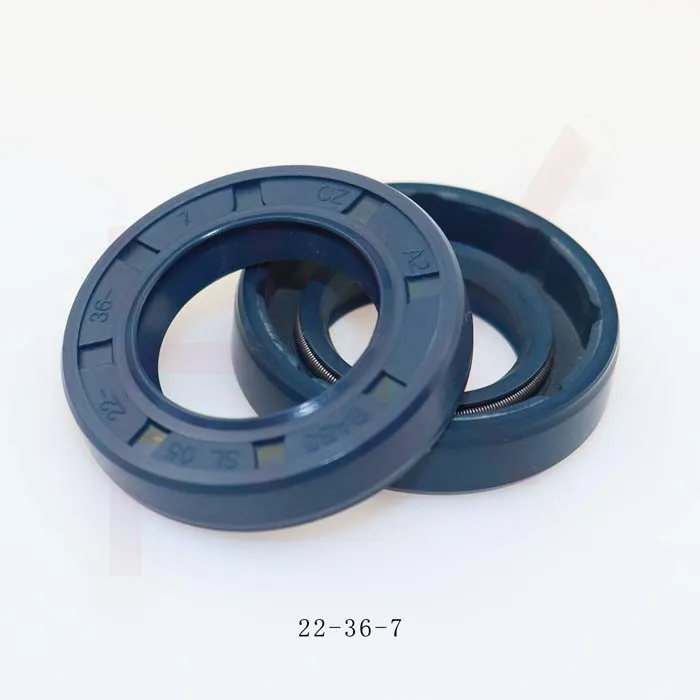
Installation precision is critical when dealing with shaft dust seals. Properly installed seals are central to preventing leaks and potential mechanical damage. Specialists must ensure that the seal is seated correctly, checking for any gaps or misalignments that might compromise its efficiency. Regular inspections can help identify early signs of wear or damage, such as hardened or cracked sealing surfaces, which, if unaddressed, may lead to seal failure.
Shaft dust seal failure can manifest in several ways, often initially noticeable as minor leaks or overheating in the machinery. Over time, unnoticed or uncorrected seal failure can evolve into more significant problems, potentially necessitating costly repairs or causing an outright breakdown. Effective maintenance routines should include periodic inspections and prompt replacement of failing seals, ensuring that machinery continues to operate smoothly and safely.
shaft dust seal
Investing in high-quality shaft dust seals may appear trivial, but their impact on operations is substantial. Using a substandard seal can lead to premature wear of machine components, driving up maintenance costs and downtime. Moreover, operational inefficiencies can lead to increased energy consumption, thereby cutting into any cost savings achieved by opting for cheaper components in the first place. High-quality shaft dust seals contribute indirectly to a reduction in environmental impact by improving efficiency and reducing waste.
In terms of innovation, the development of new composite materials in seal technology is pushing the boundaries of what shaft dust seals can achieve. Enhanced designs provide greater longevity and stress resistance under extreme conditions — advancements that result in lowering long-term operational costs. It's essential for industry professionals to keep abreast of these innovations, integrating the latest technological advancements into their systems to maintain a competitive edge.
Shaft dust seals are not merely functional components but pivotal protectors of mechanical integrity. Their role in maintaining lubricants, preventing contamination, and ensuring smooth operation cannot be overstated. For companies, this translates to better operational reliability and reduced maintenance costs, thereby safeguarding their investments and sustaining high productivity levels.
By emphasizing detailed understanding and application of shaft dust seals, companies and engineers can significantly enhance machine reliability and performance. This involves careful consideration of the seals' material compatibility, installation precision, and regular maintenance practices. Recognizing the critical role these components play in the broader mechanical ecosystem is fundamental to achieving optimal system performance and operational longevity. Developing expertise and staying informed about the latest seal technologies further establishes a firm foundation for durable and efficient system operations, reinforcing both trust and authority within the industry.