Seals and wipers are critical components in a wide range of industrial and automotive applications, ensuring the efficiency and longevity of machines by preventing the ingress of contaminants and maintaining fluid containment. Drawing from years of experience and industry expertise, this article sheds light on the nuances of these indispensable components.
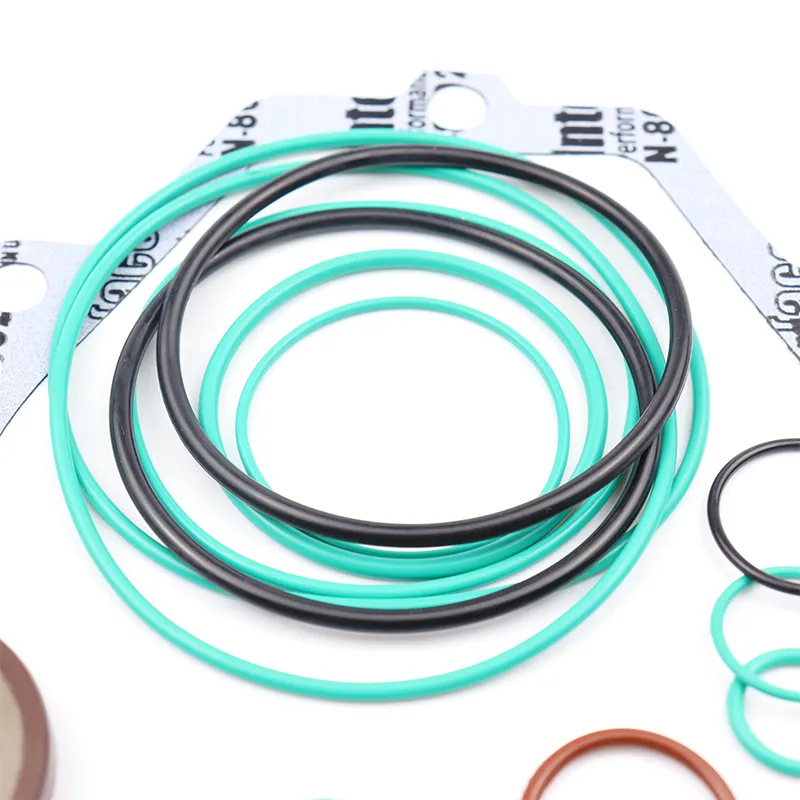
Seals, often regarded as the unsung heroes of mechanical systems, play a pivotal role in maintaining the integrity of any mechanical assembly. They function primarily to prevent leaks, ensuring that fluids — be it hydraulic oil, lubricants, or coolants — remain contained within their designated areas. This not only helps in maintaining optimal operational efficiency but also extends the life of machinery by minimizing wear and tear.
The material composition of seals is one of the key determinants of their effectiveness. Traditionally, seals have been manufactured using rubber, owing to its flexibility and resilience. However, advancements in material science have introduced synthetic alternatives such as PTFE (Polytetrafluoroethylene) and Viton, which offer superior resistance to temperature and chemical exposure. As an expert in seal manufacturing, the choice of material should always be aligned with the operational environment; for instance, a seal used in a high-temperature application must withstand thermal cycling without degrading.

Turning to wipers, these components serve a complementary yet distinct function. Often used in conjunction with seals, wipers remove dust, dirt, and other contaminants from the surface of a moving shaft. This is particularly crucial in outdoor or harsh environments where the presence of debris could compromise the integrity of seals and lead to system failure. Wipers are engineered for durability and precision, with designs that range from single to multiple lip configurations to suit different applications.
seals and wipers
The authoritative aspect of selecting seals and wipers hinges on understanding the particular requirements of the machinery or system. Industry standards, such as those set by organizations like SAE International or ISO, provide guidelines that help in selecting the right type and size of seals and wipers. Compliance with these standards ensures not only optimal performance but also safety and reliability.
Trustworthiness in the realm of seals and wipers is heavily influenced by the manufacturer's reputation. Brands that have consistently demonstrated quality, innovation, and commitment to customer satisfaction tend to be the go-to options for both OEMs and maintenance professionals. Reliability in performance, as evidenced by long-standing industry usage, underpins the trust that these components will perform under specified conditions over extended periods.
In conclusion, selecting the right seals and wipers is a decision that should be approached with a comprehensive understanding of both product specifications and the operational environment. With their critical role in enhancing the performance and life of equipment, seals and wipers are more than just peripheral components; they are central to maintaining the mechanical health of systems. As experts in the field, it is imperative to prioritize quality, adhere to industry standards, and choose reputable manufacturers to ensure trustworthiness in every application.