Seal kits for cylinders, an essential component in hydraulic and pneumatic systems, are the unsung heroes that ensure machinery operates seamlessly. Their complex design and strategic placement within machinery can dramatically extend equipment lifespan, reduce maintenance costs, and improve operational efficiency. Understanding their nuances not only establishes a baseline of expertise but also fosters trust among potential buyers.
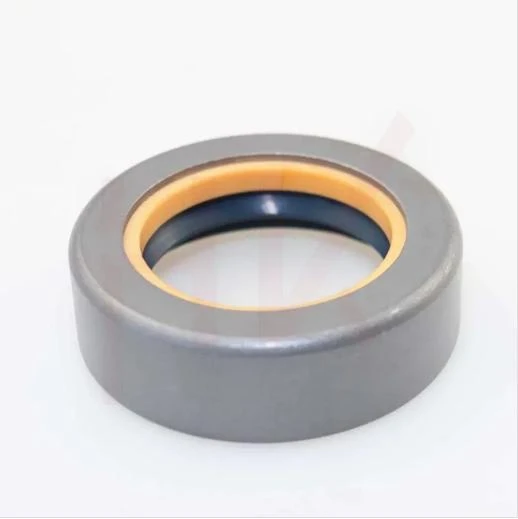
The first step in appreciating a seal kit's role is recognizing the diverse environments in which these cylinders operate. From construction giants like excavators to precision medical devices, each application demands a specific type of seal kit. A quality seal kit protects against leakages by maintaining optimal pressure within hydraulic or pneumatic systems. This is crucial, as leaks can lead to system failures, costly downtime, and expensive repairs.
A fundamental element of expertise in seal kits revolves around material composition. Seal kits are typically made from rubber, polyurethane, or PTFE, each offering distinct benefits depending on the application. Rubber seals provide excellent elasticity and enduring performance in varying temperatures, making them suitable for general purposes. Polyurethane seals are notable for their resistance to abrasion and extrusion, ideal for high-pressure environments. PTFE, known for its chemical stability and low friction, excels in specialized applications requiring excellent resistance to aggressive chemicals and extreme temperatures.
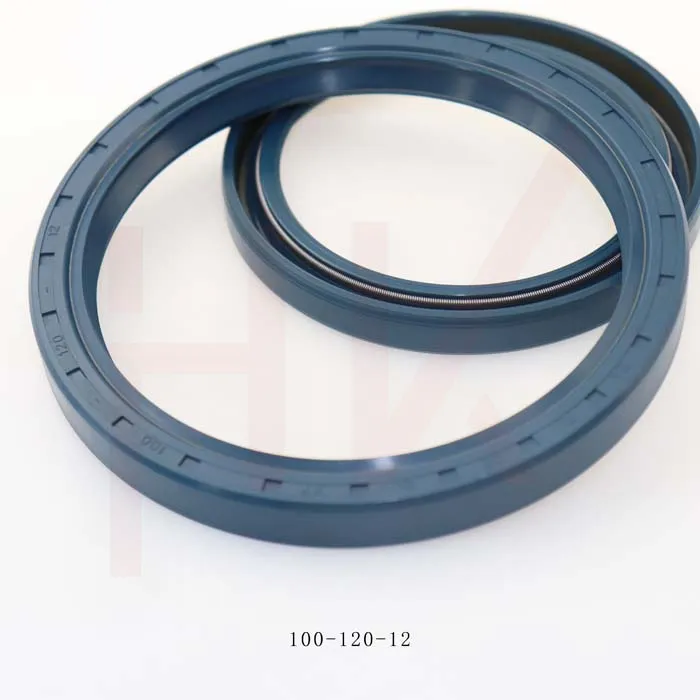
An authoritative voice in this domain emphasizes the importance of precision in selecting the right seal kit. Manufacturers often face a dizzying array of options calibrated for different shaft sizes, pressure ratings, and temperature ranges. Dependable suppliers provide detailed specifications and compatibility data, ensuring that end-users can make informed decisions. This emphasis on detailed product information not only aids in the selection process but enhances the credibility of the provider.
seal kit cylinder
Moreover, credible suppliers stay abreast of the latest advancements such as anti-extrusion backup rings or novel materials that reduce wear and tear. These innovations require a rigorous understanding of both the material science involved and the practical implications for machinery performance. Buyers are thus assured of receiving products that are not just current but also grounded in scientific progress.
Trustworthiness in the seal kit market is augmented by the supplier's customer support and warranty policies. Reputable companies offer comprehensive support throughout the product lifecycle, from installation guidance to troubleshooting. They also stand by their products, offering warranties that provide customers peace of mind — a critical factor when costly equipment relies on these seemingly simple components.
Real-life experience also showcases the impact of seal kits on operational success. Consider a manufacturing plant plagued with repeated downtime due to leaky seals. Upon consultation with a knowledgeable supplier, the plant switched to a high-performance polyurethane seal kit designed for the pressures specific to their machines. The result was a remarkable reduction in downtime and maintenance costs, underscoring the profound financial and operational impacts that expert selection of seal kits can have.
In sum,
the importance of understanding the intricacies of seal kits for cylinders cannot be overstated. Their selection is a nuanced process that requires a blend of technical expertise, authoritative knowledge of the latest industry trends, and trust in reputable suppliers. By prioritizing these factors, businesses not only optimize their machinery’s efficiency but also safeguard their bottom line. For these reasons, engaging deeply with the subject of seal kits transcends a mere procurement process; it becomes a decisive step toward operational excellence.