Rubber hub seals are a critical component in the realm of automotive technology and machinery, ensuring smooth operation and safeguarding essential mechanisms from external contaminants. Understanding their significance, functionality, and the nuances of their applications is imperative for anyone involved in industries where wear and tear can trigger costly inefficiencies.
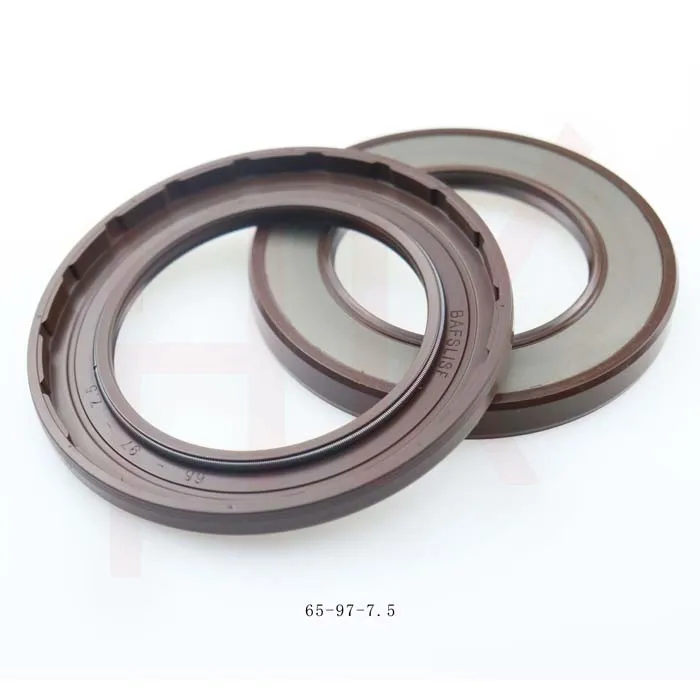
A rubber hub seal acts as a barrier, effectively sealing rotary elements, shafts, and other components. It prevents the ingress of dust, dirt, and other fine particles, which can prove detrimental to the function and longevity of mechanical systems. This protective function is vital, considering the adverse conditions under which many machines operate. From high-temperature settings in industrial environments to water exposure in agricultural machinery, rubber hub seals withstand diverse challenges to maintain optimal performance.
Manufactured from a specific blend of synthetic rubber, these seals are designed to exhibit outstanding resilience against external elements. Key considerations include thermal resistance, elasticity, and durability, which collectively determine the seal's performance. High-quality rubber compounds are essential for seals expected to endure extreme temperatures and conditions without compromising their protective abilities.
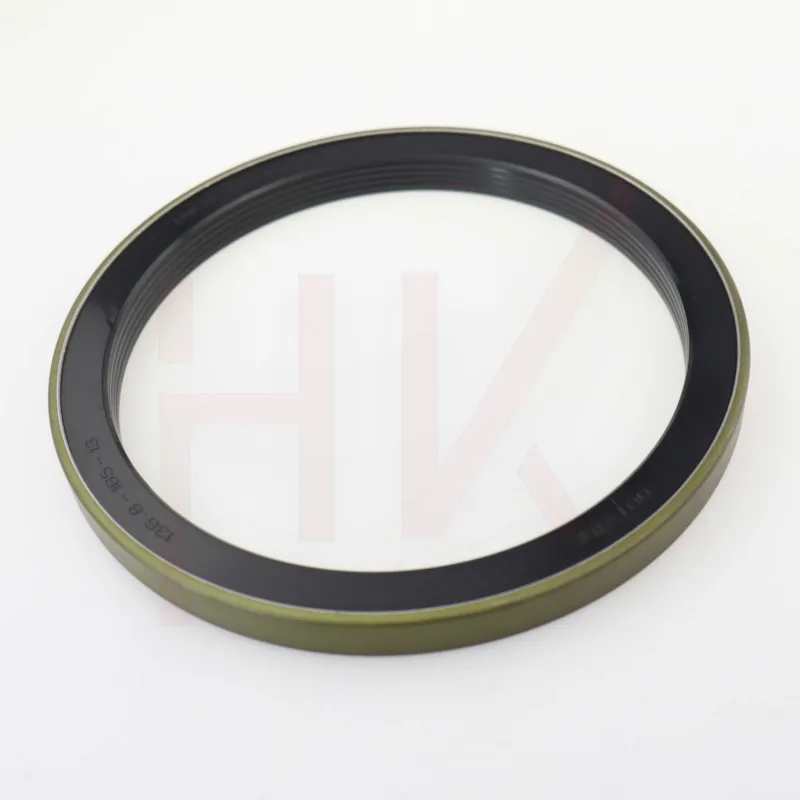
Selection of the right rubber hub seal is critical. Expertise in material engineering and a comprehensive understanding of the operational environment are prerequisites for making informed decisions. An accurately chosen seal can greatly enhance the efficiency of machinery, directly influencing downtime, maintenance costs, and overall productivity. A properly designed seal can significantly curtail lubricant leakage, thus optimizing the machinery's operation and extending its lifespan.
Moreover, expertise is required for installation. Improperly installed seals can result in accelerated wear, leakage, and system breakdowns. This emphasizes the need for experienced technicians who understand the intricacies of hub seal installations. Training and continuous education are crucial in ensuring those responsible for maintaining these systems possess up-to-date knowledge of developments in seal technology.
rubber hub seal
The authoritative use of rubber hub seals rests on robust empirical research. Research and development in the polymer engineering field have led to innovations such as enhanced thermal stability and chemical resistance in rubber compounds. These advancements inform best practices, ensuring users are implementing technology that reflects the latest industry standards.
Trustworthiness in rubber hub seal applications also hinges on compliance with industry regulations and standards. Adhering to practices endorsed by authoritative organizations such as the Society of Automotive Engineers (SAE) or the International Organization for Standardization (ISO) ensures that users apply products tested beyond rudimentary checks, verified under rigorous conditions.
Innovation continues to evolve rubber hub seal designs. Recent developments in nanotechnology and material science have introduced new compounds that promise longevity and exceptional performance. These incorporate fillers such as carbon black and silica, enhancing mechanical properties while maintaining the requisite flexibility and resilience.
In conclusion, the comprehensive understanding and correct application of rubber hub seals epitomize the fusion between engineering principles and practical deployment. Staying abreast of technological advancements and regulatory standards ensures that these vital components continue to meet the demanding needs of modern machinery, underscoring their significance within industrial paradigms. By committing to the principles of experience, expertise, authoritativeness, and trustworthiness, industries worldwide can reliably incorporate rubber hub seals to enhance the functional integrity of their machinery, underscoring the importance of these components in engineering excellence.