Rotary shaft seals, often known as lip seals or oil seals, are critical components in various mechanical systems, providing an essential barrier to retain lubricants and exclude contaminants. Their primary function is to separate environments while managing friction and wear, ensuring the longevity and efficiency of both stationary and rotational machinery.
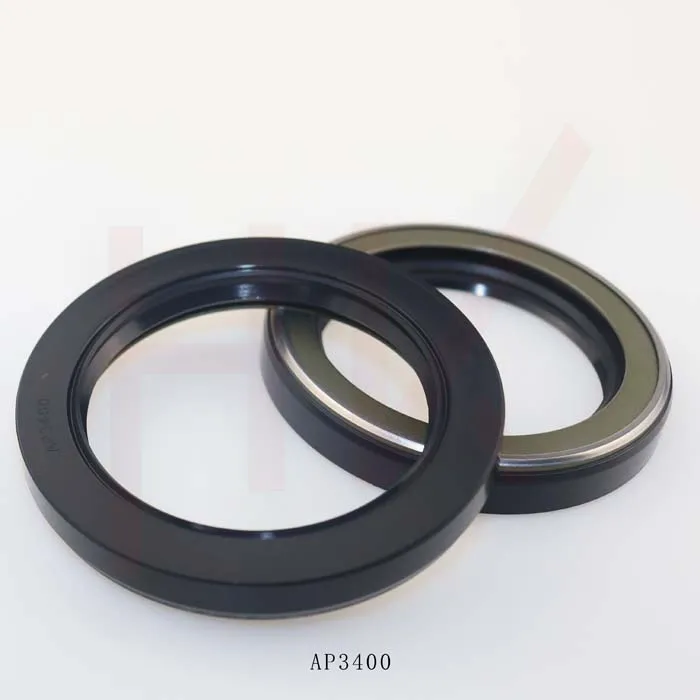
The experience with rotary shaft seals across industries presents a spectrum of benefits and challenges. Industries from automotive to aerospace have long employed these seals to improve product reliability and performance. In automotive applications, for example, these seals prevent engine oil leakage, consume less power due to reduced friction, and ensure smooth operation of the engine components.
With decades of industry use, expertise in the design and material composition of rotary shaft seals has evolved significantly. Modern seals are made from a variety of materials, including advanced elastomers, thermoplastics, and PTFE composites. These materials improve seal performance under diverse temperature ranges and chemical exposures, thereby enhancing equipment lifespan and reducing maintenance needs.
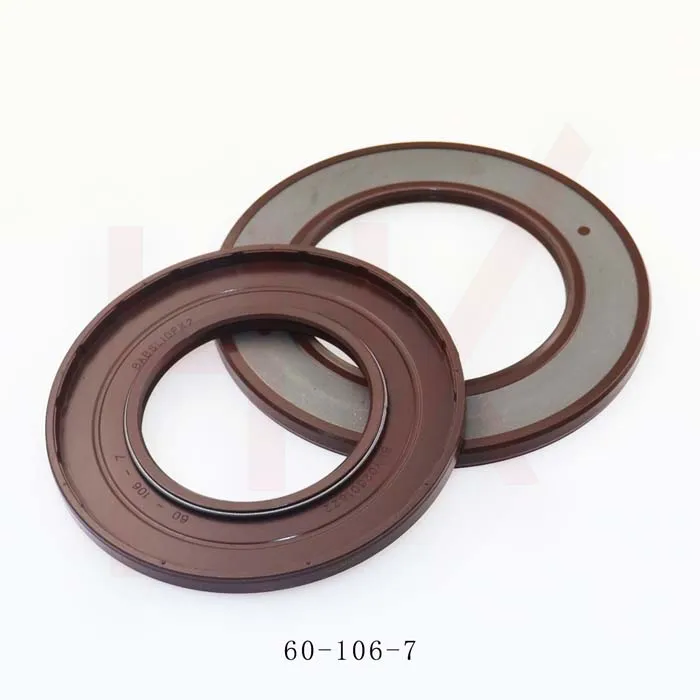
Understanding the intricacies of rotary shaft seal application is paramount for optimal performance. Professional consultation often results in tailored seal designs that address specific operational parameters such as pressure, temperature, shaft speed, and the types of fluids present. Such custom solutions not only optimize seal functionality but also extend the lifespan of machinery, reflecting the seal manufacturers' authoritative command over their domain.
rotary shaft seal
Two key phenomena impact the performance of rotary shaft seals lip wear and shaft runout. Lip wear, a direct result of continuous friction,
significantly affects seal integrity over time. The solution lies in selecting materials with superior wear resistance and lubricating properties. Conversely, shaft runout, an off-center rotation of the shaft that increases load and reduces seal life, can be mitigated with precision engineering and installation techniques, areas where trusted manufacturers provide valuable insights.
Moreover, the credibility and trustworthiness of a seal's performance are exemplified by rigorous testing and quality controls. During production, leading manufacturers utilize state-of-the-art testing facilities to simulate real-world conditions, assessing factors such as thermal cycling, pressure stability, and fluid compatibility. These tests not only refine product reliability but also instill confidence among end users in various industries.
From a product and commercial perspective, the evolving landscape of rotary shaft seals is driven by innovation and sustainability efforts. Manufacturers now focus on environmentally friendly materials and production processes, responding to global demands for reduced carbon footprints and compliance with international environmental standards.
In conclusion, rotary shaft seals serve as a pivotal element in machinery efficiency and durability. Their development, backed by profound expertise and stringent quality assurance, underscores their authoritative role in modern engineering applications. For companies looking to enhance machinery longevity and performance, investing in high-quality rotary shaft seals is a testament to their commitment to reliability and sustainable operation. Emphasizing tailored solutions, cutting-edge materials, and robust testing processes, trusted manufacturers offer an invaluable resource in navigating the complexities of seal technology.