In the world of mechanical applications,
the tiny yet mighty rotary oil seal plays a crucial part. These seals, though often overlooked, serve as unsung heroes by ensuring the seamless operation of machinery and extending the life of mechanical components. Understanding their importance, the intricacies involved in their functioning, and how to select the right seal can make a significant difference in industrial maintenance and engineering applications.

Rotary oil seals, often referred to as shaft seals or lip seals, perform the vital task of excluding contaminants like dirt, dust, and moisture while retaining lubricants within rotating shafts and bearings. Their precision in preventing lubricant seepage and ingression of foreign materials ensures optimal performance, reduces friction, and minimizes wear, thereby enhancing the efficiency of machinery. It’s imperative to acknowledge that the integrity of an entire system can be compromised by a malfunctioning seal, making the choice of the appropriate rotary oil seal paramount.
Delving into the engineering of rotary oil seals reveals a diverse array of materials and designs tailored to specific applications. Commonly crafted from elastomers such as nitrile (NBR), fluoroelastomer (FKM), or silicone, these materials are chosen for their ability to withstand varying temperature ranges, chemical interactions, and mechanical stresses. For applications involving exposure to high temperatures and aggressive fluids, fluoroelastomer seals are preferred due to their superior resistance. Conversely, nitrile seals are often deployed in less demanding environments due to their cost-effectiveness and reasonable operational limits.
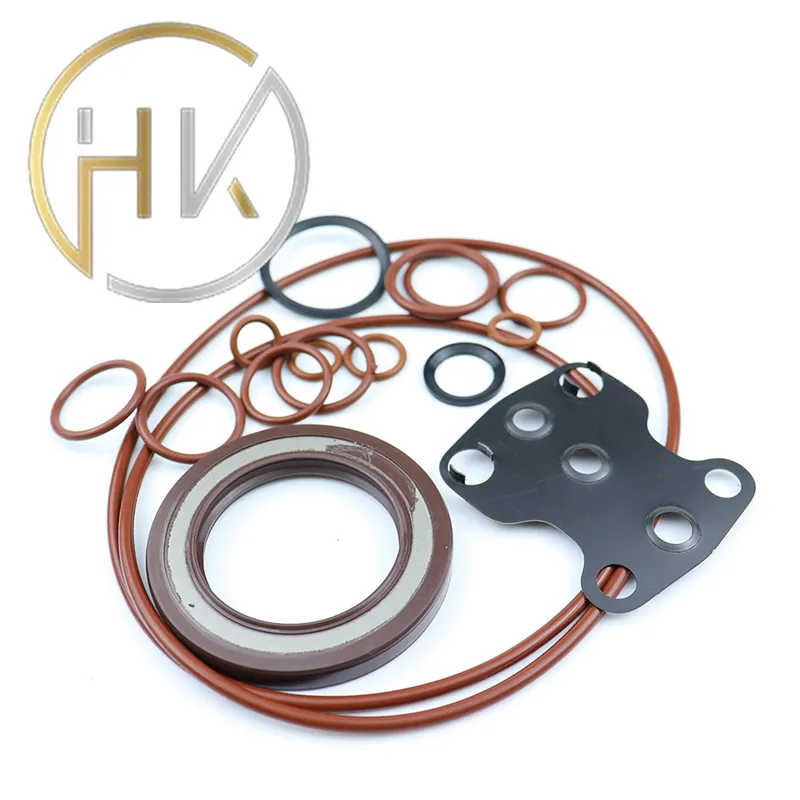
The design of rotary oil seals is equally varied, featuring single-lip, double-lip, and multi-lip configurations depending on the sealing requirements. Single-lip seals are employed for straightforward sealing tasks where contaminants are minimal, while double-lip seals offer added security by incorporating an auxiliary lip that provides enhanced protection against contaminants and leakages. Multi-lip seals extend these protections further by offering multiple layers of defense, often utilized in heavy-duty applications where the stakes of failure are high.
When selecting a rotary oil seal, several factors must be meticulously considered to ensure compatibility with the intended application. Shaft speed, temperature, pressure fluctuations, and the nature of the lubricant are critical variables that influence seal performance. A mismatch in any of these parameters can lead to premature seal wear, leakage, or total seal failure, resulting in costly downtime and repairs.
rotary oil seals
Moreover, installation precision plays a pivotal role in the longevity and effectiveness of rotary oil seals. An improperly installed seal, no matter how well-suited it is to the application, is prone to failure. It is essential to ensure that shafts are correctly aligned, surfaces are clean and smooth, and the seals are gently handled to prevent any damage to the delicate sealing lip. Utilizing specialized tools designed for seal installation can dramatically increase the success rate of seal implementation.
Maintaining rotary oil seals involves regular inspections and timely replacements to avert unscheduled downtimes. During maintenance checks, signs of wear, such as cracking, hardening, or swelling, indicate the need for immediate replacement. A well-implemented maintenance regime not only extends the seal’s lifespan but also enhances the overall reliability of the machinery.
In terms of sourcing, collaborating with reputable manufacturers who demonstrate expertise and reliability is indispensable. These manufacturers often provide insights into the latest advancements in seal technology, such as specialized coatings or treatments that reduce friction and wear, thus optimizing the performance and efficiency of seals.
To encapsulate, rotary oil seals, despite their unassuming presence, are fundamental to the optimal functioning of a wide range of mechanical systems. Their role in maximizing machinery performance, preserving system integrity, and minimizing downtime cannot be overstated. By comprehending their material and design intricacies, adhering to precise installation standards, and maintaining a vigilant maintenance schedule, industries can significantly enhance their operational efficiencies. Such diligence in managing rotary oil seals is not merely an operational necessity but a strategic advantage in the competitive industrial landscape.