The rod wiper seal, often overshadowed by its more illustrious counterparts in the hydraulic and pneumatic systems, is a critical component that ensures the longevity and efficiency of machinery. This seemingly modest seal plays a pivotal role in maintaining the hygiene of equipment by preventing the ingress of contaminants like dust, dirt, and moisture.
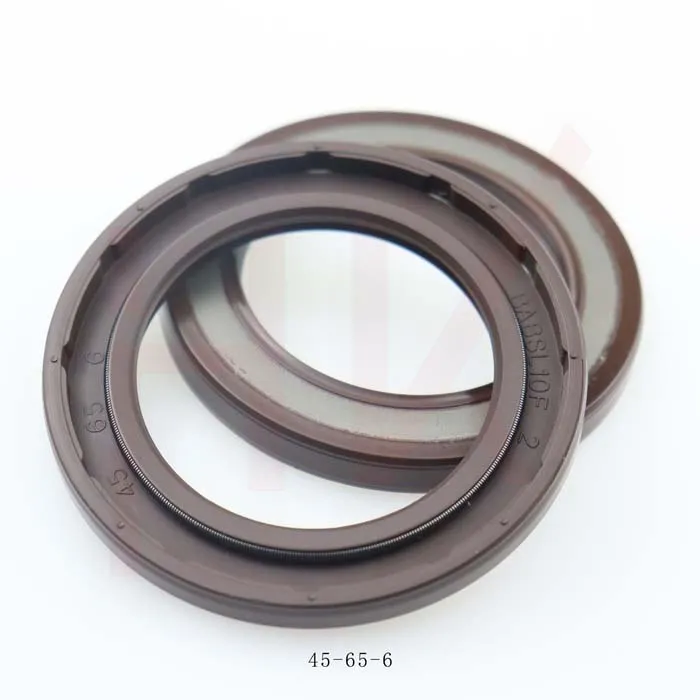
Experience with rod wiper seals has revealed that their performance hinges significantly on the material composition and the specific application they are used for. Nitrile rubber is commonly used for general applications due to its excellent resistance to oils and ability to function across a range of temperatures. For more demanding environments, such as those involving chemicals or extreme temperatures, materials like fluorocarbon or polyurethane may be more appropriate due to their enhanced durability and resistance.
Experts understand that the selection of a rod wiper seal should never be an afterthought. The intricacies of machine operation can lead to drastic consequences if a seal fails, including potential safety hazards and extensive machine downtime. Therefore, engineers and operators are advised to meticulously analyze the operational conditions, such as speed, pressure, and temperature, before choosing the appropriate seal.
This proactive approach ensures that the machine operates smoothly while minimizing the risk of unexpected failures.
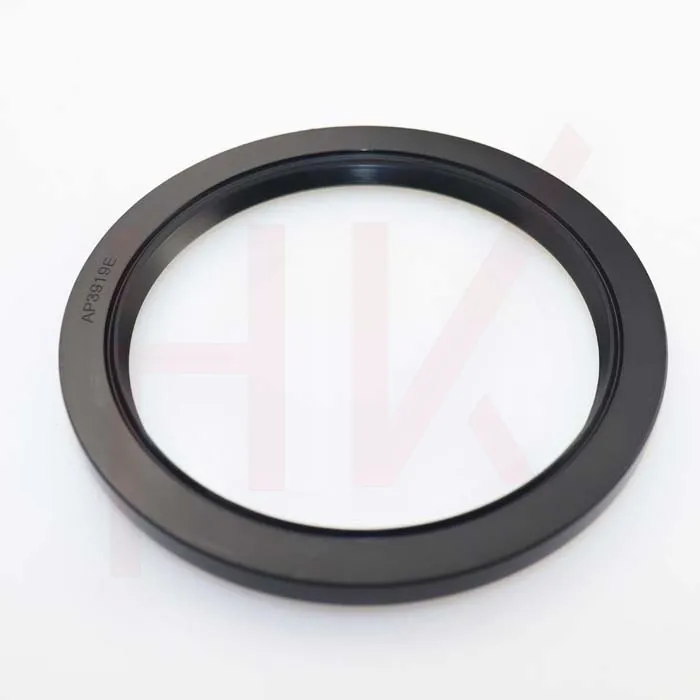
Authoritatively speaking, rod wiper seals are engineered to accommodate the dynamic nature of machine rods, which retract and extend during operation. This motion necessitates that the seal maintains a tight yet adaptable grip on the rod, providing a physical barrier to contaminants while allowing for the necessary motion. Manufacturers such as Parker Hannifin and SKF have set industry standards by introducing specialized rod wiper designs that cater to various industrial needs, showcasing their commitment to quality and innovation.
rod wiper seal
Trustworthiness is a crucial attribute in the business of rod wiper seals. The integrity of a seal can often determine the line between a machine's operational success and failure. Thus, it's imperative for procurement managers and engineers to select seals from reputable suppliers who adhere to stringent quality control measures and possess a track record of reliability. Certifications and compliance with international standards, such as ISO 9001, offer reassurance that the seals meet high-quality requirements.
The evolving landscape of industrial applications continues to pose new challenges and expectations for rod wiper seals. As industries move towards more sustainable and energy-efficient solutions, there is a growing demand for seals that not only perform effectively but also contribute to lower energy consumption and prolonged machine life. Innovative seal designs, featuring enhanced lip profiles and advanced material blends, are at the forefront of this evolution, marrying traditional reliability with modern efficiency needs.
Through real-world applications, rod wiper seals have proven indispensable in sectors ranging from automotive to aerospace. In hydraulic cylinders, for example, their role in preventing oil leaks and keeping contaminants out is fundamental to maintaining hydraulic pressure and operational efficiency. Similarly, in industrial machinery, the reliability of rod wiper seals ensures that machines run without unnecessary interruptions, directly affecting productivity and profitability.
In conclusion, the rod wiper seal, while small, offers significant value in the larger scheme of mechanical operations. By focusing on material selection, design innovation, and supplier integrity, businesses can achieve optimal equipment performance and longevity. The experts’ consensus is clear attention to detail in the selection and maintenance of rod wiper seals is crucial. As industries continue to optimize and upgrade their machinery, rod wiper seals will play an increasingly vital role in ensuring that these machines remain operationally effective and efficient.