Experiencing leaks or inefficiencies in your pumping system can be frustrating and costly. One critical component that often requires attention is the pump seal kit. Understanding how to replace a pump seal kit effectively can save time, extend the lifespan of your equipment, and enhance overall system performance. Drawing from years of industry experience and technical expertise, here's a comprehensive guide to replacing pump seal kits.
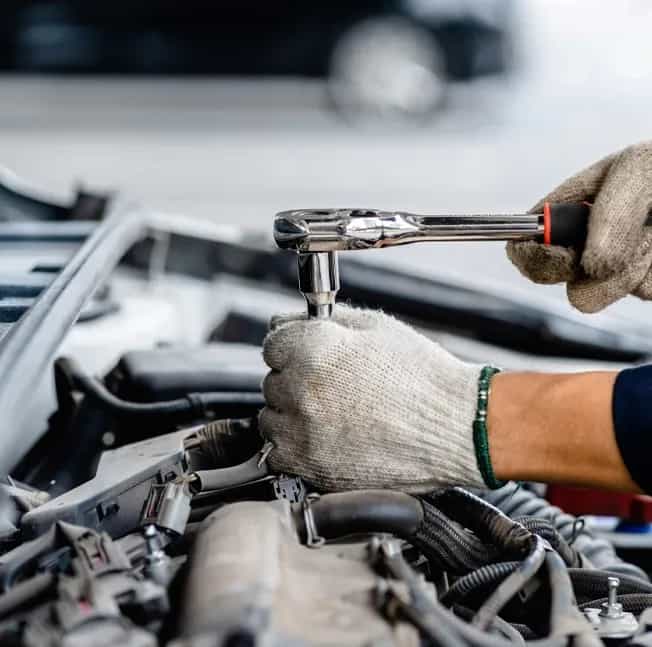
Having been involved in multiple projects concerning pump maintenance, it's evident that recognizing the earliest signs of a failing seal is crucial. Look for excessive vibration, leaks around the shaft, and unusual noises - these are common indicators that your pump seal may be compromised. Early detection not only prevents further damage but also reduces downtime and repair costs.
To begin the replacement process, safety is paramount. Ensure that the pump is completely disconnected from its power source and any interconnected systems are isolated. Always wear appropriate personal protective equipment, as this process may involve handling hazardous materials.
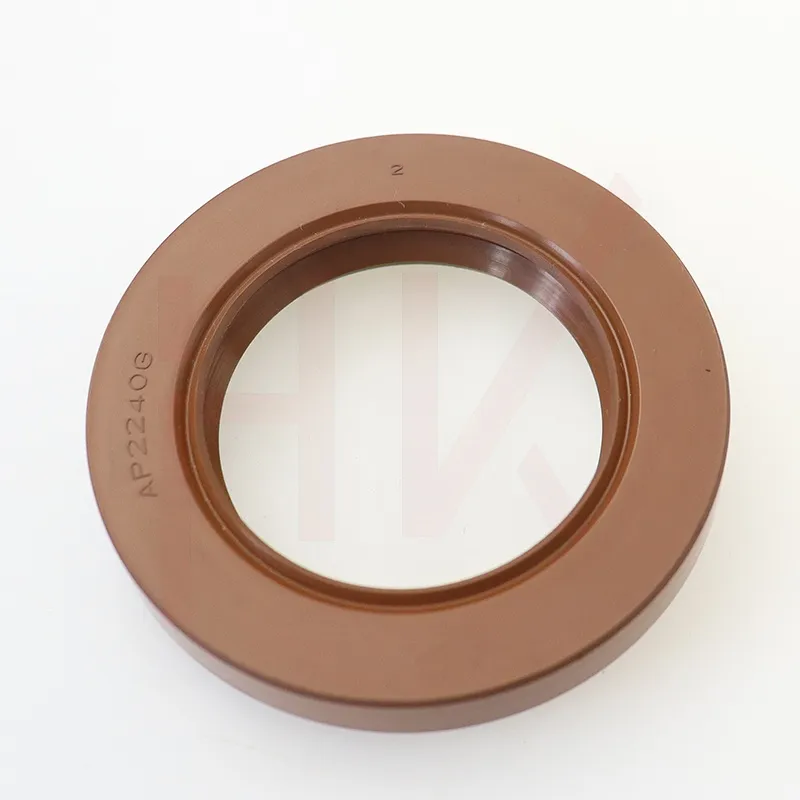
Next, it's essential to understand the specific type of seal kit required for your pump. Pumps vary significantly in design, and using the wrong seal can lead to further malfunctions. Refer to the manufacturer's manual or consult with a specialist to identify the correct seal kit. As an expert, I recommend maintaining an inventory of common seal kits relevant to your machinery to expedite replacement times.
Before disassembling the pump, thoroughly clean the exterior to prevent contaminants from entering the system during the replacement. Once clean, carefully dismantle the pump casing. Utilize tools that are suitable for your specific pump type—this is especially important with high-precision pumps used in industrial settings.
During my time in the field, a meticulous approach to examining each pump component has consistently proven invaluable. Inspect the mechanical seal for any visible damage or wear. Frequently, the cause of failure is evident in the form of cracked or brittle seal faces, or distorted elastomers. Understanding these symptoms allows for more informed decisions concerning parts replacement.
pump seal kit replacement
Upon assessing the old seal, clean the seal chamber and surrounding areas, removing any debris or residue that could affect the new seal’s performance. Installing the new seal requires precision; ensure the seal faces are not contaminated during installation. A lightly oiled cloth can be used to handle the seal, offering lubrication without risking impurities.
Assembly of the pump should follow in reverse order of disassembly, ensuring that every bolt and fitting is securely fastened. Before powering the pump, conduct a manual rotation check where applicable, ensuring there are no obstructions or abnormal resistance in the mechanical movement.
Post-installation, it's advisable to perform a test run at low pressure to verify the integrity of the new seal. Pay close attention to any leaks or irregularities in system behavior. In my professional experience, documenting the entire process with notes and photographs can be extremely beneficial for future reference or for conveying information to other team members.
For those managing large-scale operations, implementing a routine maintenance and inspection schedule can drastically reduce the frequency and impact of pump seal failures. This proactive approach not only embodies best practices consistent with industry standards but also reinforces reliability and trust within your supply chain.
In conclusion, replacing a pump seal kit is a critical maintenance task that demands both expertise and attention to detail. Employing a structured method enhances both the performance and longevity of your pumping systems. Whether you are a seasoned technician or new to machinery upkeep, staying informed and prepared is the foundation of effective maintenance. Leveraging professional insights and continuously updating your knowledge in line with technological advancements will keep your operations efficient and secure.