When considering the integral components that ensure the smooth and efficient operation of pneumatic systems, the pneumatic wiper seal often goes unnoticed, yet it plays a crucial role. These seals are pivotal in preventing contaminants from infiltrating pneumatic cylinders, thereby maintaining optimal performance and longevity of machinery. Understanding the importance of pneumatic wiper seals, their design intricacies, and their application is essential for industries reliant on pneumatic systems.
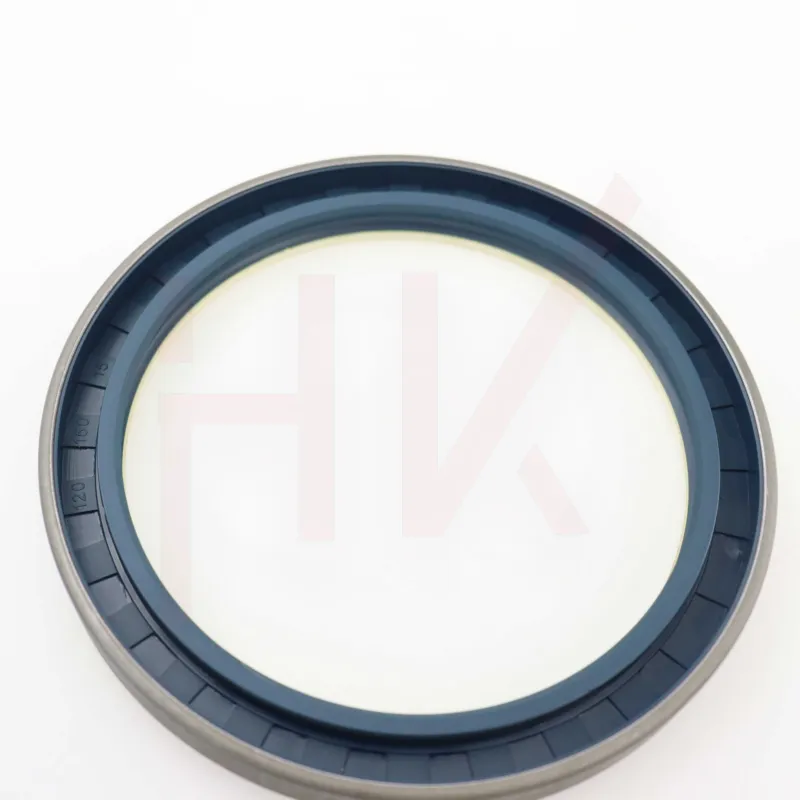
Pneumatic wiper seals are designed to primarily prevent the ingress of dust, dirt, moisture, and other particulate contaminants into cylinders. By forming a tight seal, these components effectively safeguard the internal elements of pneumatic systems, ensuring consistent performance and preventing costly downtime due to contamination-related failures. The seal acts as the first line of defense, wiping off any external contaminants as the rod retracts into the machinery.
The expertise in selecting the right wiper seal involves a thorough understanding of the material properties and compatibility with the environmental conditions. Wiper seals are typically crafted from elastomeric materials such as polyurethane, NBR (Nitrile Butadiene Rubber), or advanced polymers like PTFE (Polytetrafluoroethylene). Each material offers distinct advantages; polyurethane is known for its excellent abrasion resistance, NBR provides a balance of performance and cost-effectiveness, while PTFE is unbeatable in environments where chemical resistance and low friction are paramount.
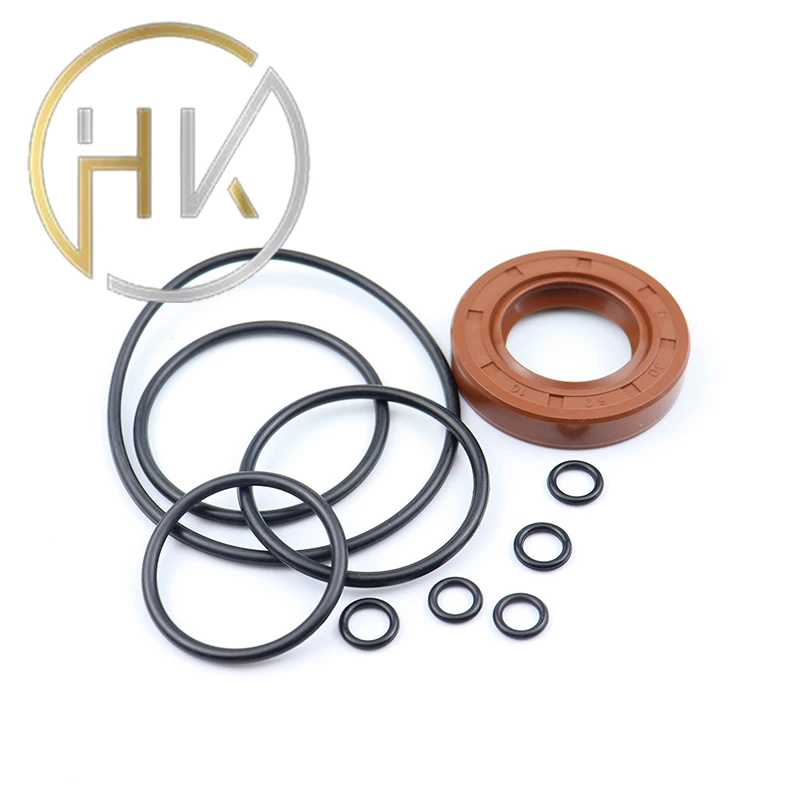
From an authoritative standpoint, manufacturers and industry experts emphasize the significance of precise engineering in pneumatic wiper seal design. The seal must be designed with an optimal lip profile that ensures effective wiping action without causing undue friction or wear on the rod surface. Innovations in design also include double-lip wiper seals, which provide an additional layer of sealing to enhance protection against contaminants.
For effective implementation,
trustworthiness in seal performance is critical. Industry best practices suggest partnering with reputable manufacturers who supply seals that adhere to stringent quality control standards. Ensuring that wiper seals meet international standards such as ISO or DIN can provide additional assurance of their reliability and longevity.
pneumatic wiper seal
In practical application, industries ranging from automotive to aerospace rely heavily on pneumatic wiper seals. In automotive manufacturing, for instance, wiper seals are crucial in pneumatic actuators ensuring precision and efficiency in assembly lines. In aerospace, the exacting standards of component performance demand wiper seals that can withstand extreme temperature variations and pressure conditions, ensuring safety and operational integrity.
Maintaining a stock of these seals and routine inspections can preemptively resolve potential issues, thereby reducing machinery downtime and extending the lifespan of pneumatic systems. Keeping an eye on wear patterns and performance degradation can also provide insights into the operating environment and possible adjustments needed for optimal system functioning.
Empirical evidence from industry leaders showcases that the failure of wiper seals can lead to rapid degradation of pneumatic components, necessitating expensive repairs and unscheduled maintenance. Investing in high-quality seals and regular maintenance can prevent such issues, offering substantial cost savings over time.
In conclusion, pneumatic wiper seals may seem like minor components in the grand scheme of industrial machinery; however, their ability to prevent contamination is critical for maintaining the efficacy and reliability of pneumatic systems. Companies that prioritize high-quality seal materials, precision engineering, and adherence to quality standards will likely experience better operational outcomes and longer equipment life spans. Understanding the profound impact of this seemingly trivial component allows businesses to optimize performance and safeguard their pneumatic systems against the challenges of modern industrial environments.