Oil wiper rings are critical components in the operation of various machinery and engines. Their primary function is to ensure the efficient control and management of oil flow, which is essential for maintaining the integrity of mechanical systems. For those new to this topic or seeking to improve their understanding, let's explore the essential aspects that define the significance, application, and advancements in oil wiper ring technology.
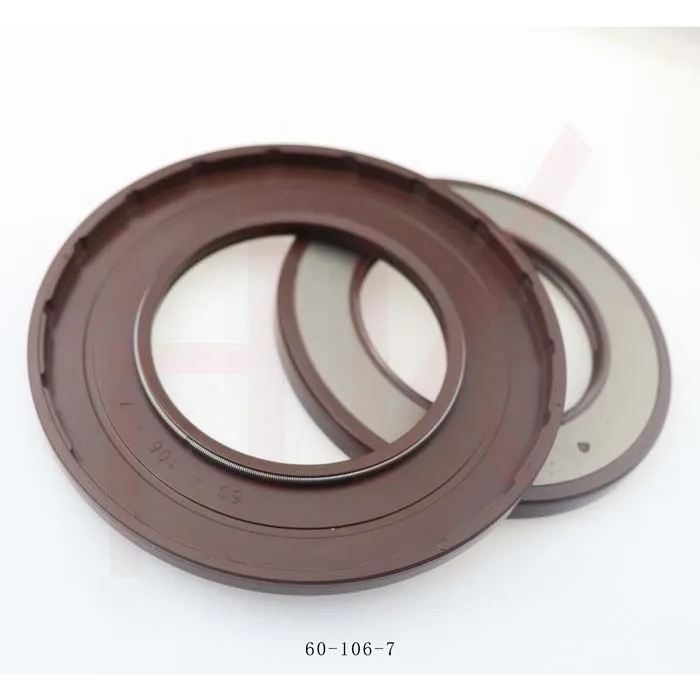
At their core, oil wiper rings play a vital role in preventing oil leakage and contamination of the combustion chamber with oil in piston engines. By regulating oil flow, these rings help maintain optimal lubrication, reducing friction and wear on engine components. This, in turn, extends the life of machinery, enhances performance, and prevents costly downtime due to maintenance or repairs. The expertise involved in the design and manufacturing of oil wiper rings has evolved significantly, with modern companies utilizing advanced materials and technologies to produce rings that can withstand extreme temperatures, pressures, and chemical interactions.
For professionals in the industry, selecting the right oil wiper ring is a matter of technical expertise. The material composition of the ring is one critical factor, as it must be compatible with the specific operating conditions of the engine or machinery. Common materials include cast iron, steel, and specialized alloys, each offering unique properties such as resistance to wear, heat, and chemical corrosion. Additionally, the design of the ring, including its profile and tension characteristics, must be engineered to meet the specific needs of an application to ensure an effective seal and optimal oil control.
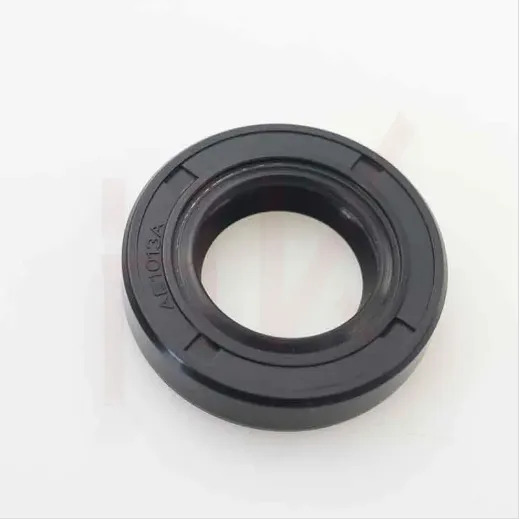
As an authoritative source in the field, manufacturers often provide detailed technical specifications and material science support to assist engineers and technicians in making informed decisions. Trust in these products is generally underpinned by rigorous testing and quality assurance processes that ensure compliance with industry standards and certifications. Moreover, the reputation of a manufacturer often plays an essential role in establishing credibility and trustworthiness, as companies with a long history of innovation and reliability are more likely to deliver consistent performance.
oil wiper ring
Recent advancements in the field have seen the integration of smart technology and data analytics into oil wiper ring systems. Some manufacturers now offer rings equipped with sensors that provide real-time data on ring performance, including temperature, pressure, and wear levels. This data can be used to perform predictive maintenance, allowing operators to address potential issues before they result in failure. Such technological innovations not only enhance the user experience but also improve operational efficiency and reduce costs.
In the realm of practical experience, feedback from clients and end-users is invaluable. Many industries, such as automotive, aviation, and manufacturing, have shared case studies demonstrating significant improvements in machine performance and longevity following the implementation of high-quality oil wiper rings. These real-world applications provide compelling evidence of the product’s impact and further assert its essential role in industrial operations.
In conclusion, oil wiper rings are an indispensable component in mechanical systems that require precision and reliability. Their contribution to maintaining lubrication, preventing contamination, and improving the longevity of machinery cannot be overstated. As technology continues to advance, so too will the capabilities and applications of these vital components, ensuring they remain a cornerstone of efficient and effective engine and machinery operation. Industry professionals and companies must continue to value expertise, rely on authoritative sources, and build trust through innovation and proven performance to maintain competitive advantage in this dynamic field.