Oil seals play a critical role in hydraulic systems, ensuring efficiency and longevity by preventing fluid leakage and contamination. A deep understanding of their design, function, and maintenance is essential for any industry professional working with hydraulic machinery.
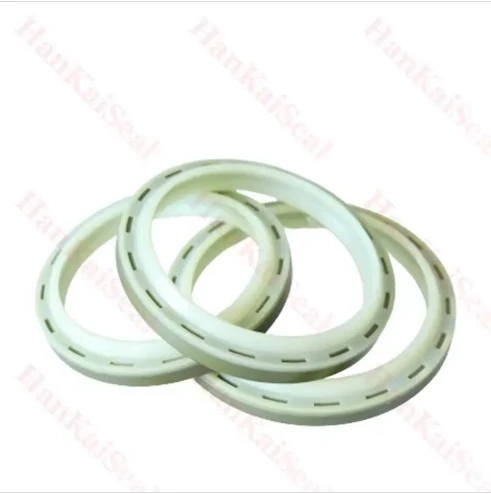
Oil seals, commonly known as shaft seals or radial lip seals, are specifically engineered to maintain the integrity of a hydraulic system by keeping lubricants in while keeping contaminants out. They are vital components in pumps, cylinders, and valves, where they manage the interaction between moving parts and the hydraulic fluid.
Professionals in the hydraulic industry appreciate the nuanced characteristics that different materials and designs of oil seals can offer. Nitrile rubber, for instance, is widely recognized for its excellent resistance to petroleum-based oils and fuels, making it a popular choice for many standard industrial applications. On the other hand, those working with more aggressive chemicals or in extreme temperature environments might opt for seals made from Viton or silicone, which provide superior chemical and thermal resistance.
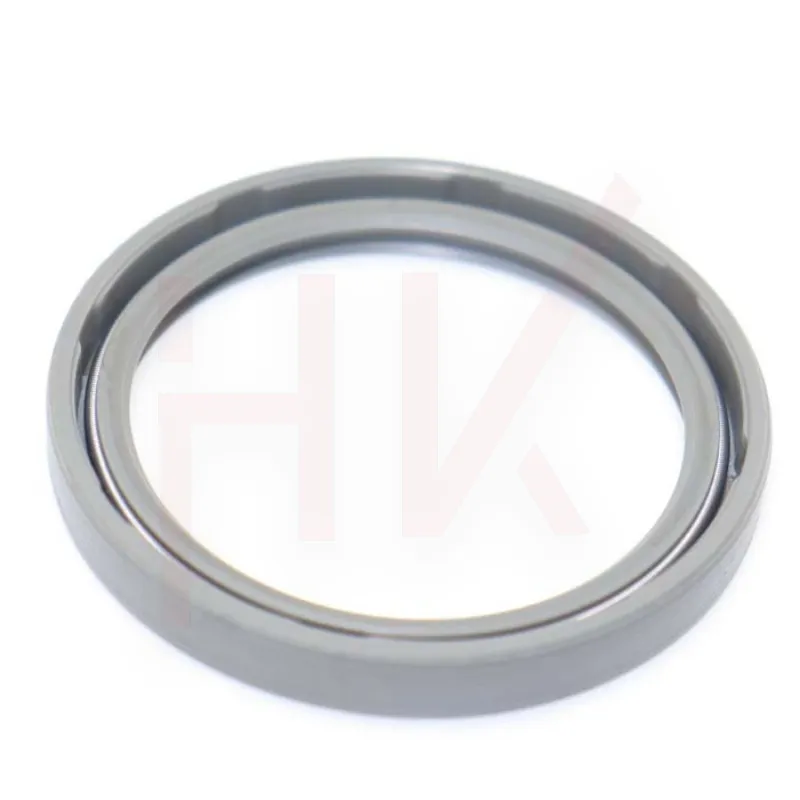
The design of oil seals is another critical aspect that experts must consider to ensure optimal performance.
The most common configuration is the lip seal, which features a flexible lip that rides on the shaft's surface. The lip design can vary greatly; some seals contain a single lip while others incorporate a dual-lip configuration for added protection against contaminants. Tension springs are also often integrated into oil seals to maintain lip pressure, ensuring continued contact and effectiveness over time.
For hydraulic systems operating under high pressure or speed conditions, specialized oil seals such as labyrinth seals or Teflon seals might be advisable. These are designed to handle the significant stress and isolation requirements present in demanding environments, providing not only superior sealing capability but also reduced wear on the interacting surfaces, thereby extending the system's lifespan.
Expert users will recognize the importance of proper installation and maintenance in maximizing the life and function of an oil seal in hydraulic applications. The installation process demands precision, as incorrect alignment or excessive force can damage seals, leading to premature failure. Using the correct tools, such as seal drivers or presses, is crucial to avoid common pitfalls like seal lip inversion or scoring of the shaft surface.
oil seal hydraulic
Regular inspection and preventive maintenance are imperative practices for sustaining operational efficiency in hydraulic systems. Experts advise routine checks for signs of wear or damage, such as cracking or hardening of the seal material, which could indicate impending failure. Furthermore, checking for proper lubrication levels and contamination presence can prevent seal degradation.
Industry insiders understand that choosing the right oil seal not only involves selecting the appropriate material and design but also understanding the specific demands of the hydraulic system it will serve. Factors such as the system's speed, pressure, temperature range, and the type of fluid used are all significant considerations that influence seal selection.
Additionally, knowledge-sharing and continued education are staples among professionals aiming to enhance their expertise in oil seals. Engaging with manufacturers for insights into the latest material and technology advancements can provide a competitive edge. Certification programs focusing on hydraulic systems and components often delve into oil seal technology, offering a more structured path to gaining in-depth knowledge.
The reliance on oil seals across industries—from automotive to aerospace—underscores their indispensability in maintaining hydraulic efficiency and reliability. Expertise in selecting, installing, and maintaining these components can significantly contribute to reduced maintenance costs, increased productivity, and a prolonged lifecycle of hydraulic equipment.
In conclusion, the effective utilization of oil seals in hydraulic systems demands a blend of technical knowledge, hands-on experience, and a proactive approach to learning about new technologies. Such a commitment not only optimizes system performance but also underscores the professional's role as a valuable asset in any industrial setting.