Understanding the essential role of the oil seal hub is crucial for industries reliant on machinery and automotive performance. This often-overlooked component plays a pivotal role in ensuring the seamless operation and longevity of machines. Experts in mechanical engineering affirm that neglecting the oil seal hub can result in significant operational disruptions, underscoring the importance of informed maintenance practices and quality component selection.
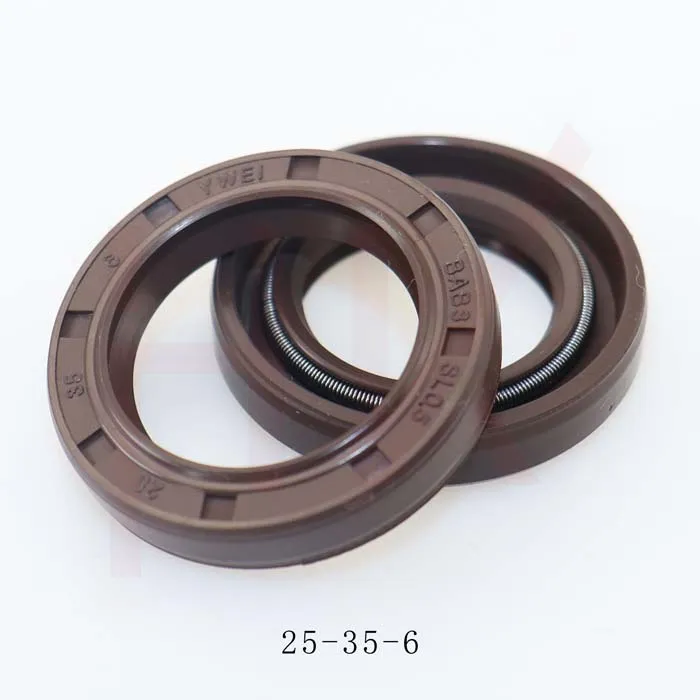
An oil seal hub prevents leakage, regulates lubrication, and protects bearings from contaminants. Its proper function is fundamental in reducing friction between moving parts, thereby minimizing wear and tear. Experienced engineers will attest that selecting the right oil seal hub can improve machinery efficiency and reduce energy consumption, translating to substantial cost savings over time.
From an expert perspective, choosing the right oil seal hub involves considering several critical factors material compatibility, environmental conditions, and operational requirements. Understanding these aspects can significantly enhance machinery performance. For instance, different materials offer varying degrees of resistance to heat, chemicals, and pressure. Nitrile rubber, silicone, and fluoroelastomers are some materials commonly used, each having specific advantages and optimal applications.
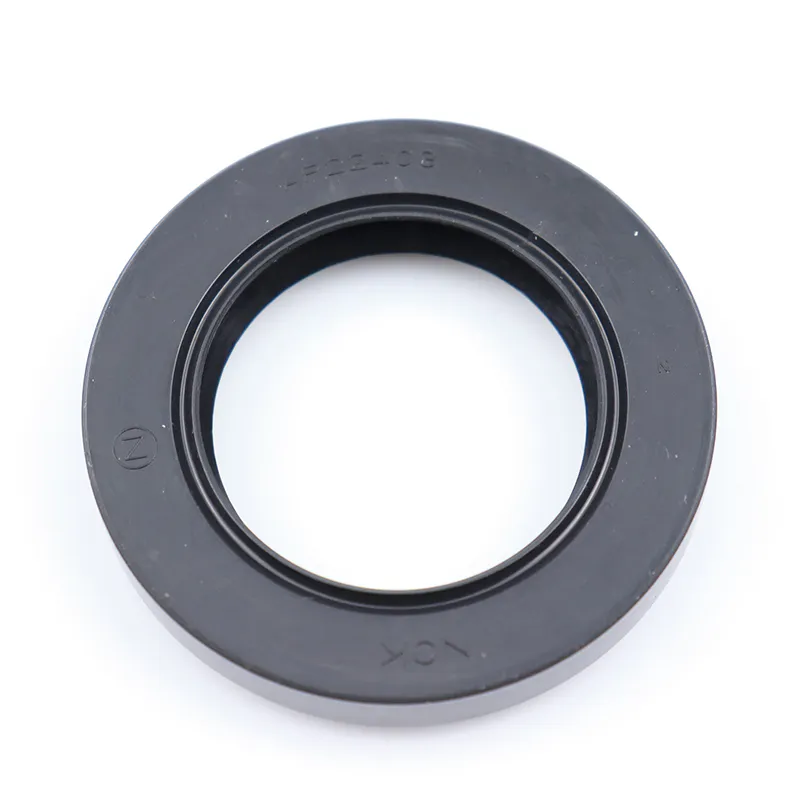
The importance of environmental awareness cannot be overstated. In industries where machinery is exposed to extreme temperatures or corrosive substances, selecting an oil seal hub with robust environmental resistance is vital. Such attention to detail is characteristic of organizations that prioritize longevity and reliability in their operations.
Expertise in oil seal hub selection hinges on understanding the nuances between dynamic and static sealing applications. Static seals are used when the sealing surfaces do not move relative to each other, while dynamic seals cater to applications where surfaces are in motion. Familiarity with these categories enables maintenance teams and engineers to make informed decisions, ensuring that operations remain smooth and uninterrupted.
oil seal hub
Furthermore, in the context of authoritativeness, relying on reputable manufacturers and suppliers is essential. Brands with proven track records offer oil seal hubs that meet rigorous industry standards, providing a level of assurance that translates into operational trustworthiness. Engineers and procurement specialists often refer to industry certifications and compliance with international standards as hallmarks of quality.
Trustworthiness extends to maintenance practices, where regular inspection and replacement of oil seal hubs prevent unexpected machine downtimes and costly repairs. Adopting a proactive maintenance schedule is a sound strategy, evidenced by years of engineering studies and industry best practices. Regular checks and timely replacements not only enhance machinery efficiency but also fortify safety measures, safeguarding both equipment and personnel.
The conversation around oil seal hubs must also include innovations and technologies driving the future of sealing solutions. As the industry evolves, new synthetic materials and designs are being introduced, promising enhanced durability and efficiency. Staying abreast of these developments demonstrates both expertise and commitment to continued operational excellence.
In conclusion, oil seal hubs may appear as small components in large machinery systems, but their significance is monumental. The experience gathered from years of industrial practice shows that when businesses invest in high-quality oil seal hubs and adhere to professional maintenance routines, they unlock significant enhancements in operational efficiency and longevity. By committing to expertise, authority, and trust, companies can anticipate greater returns on their investments, extending beyond immediate operational gains to sustained industry leadership.