Investing in the right oil seal for machinery maintenance can significantly enhance performance and extend the life of your equipment. Oil seals, also known as radial shaft seals, are integral in preventing leakage of lubricants and blocking contaminants from infiltrating machinery components. Here, we delve into the nuances of selecting and maintaining oil seals, drawing from deep industry insights and research to provide an authoritative guide tailored for machinery professionals and businesses.
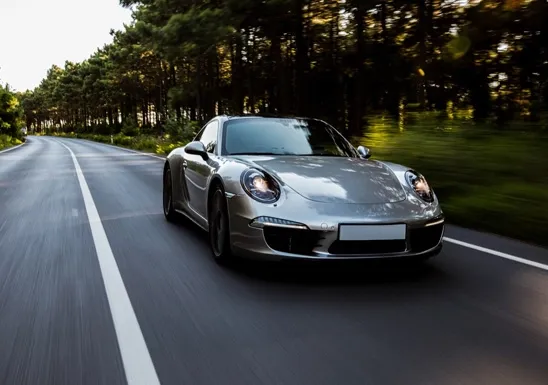
Oil seals find wide applicability across various industries, including automotive, aerospace, manufacturing, marine, and agriculture. Their primary function is to seal the openings between static and dynamic sections within mechanical equipment. To ensure your machinery's optimal functioning, choosing the right oil seal involves consideration of several critical factors.
Material selection tops the list. The most common materials for oil seals include nitrile rubber, fluorocarbon, silicone, and polytetrafluoroethylene (PTFE). Nitrile rubber is generally used for its excellent oil resistance and cost-effectiveness, while fluorocarbon stands out in high-temperature environments. Silicone seals are preferred for their flexibility and low-temperature resistance, whereas PTFE offers superior chemical resistance and is suited for challenging applications. Professionals voice the importance of aligning the material choice with specific operational conditions such as temperature, pressure, and speed.
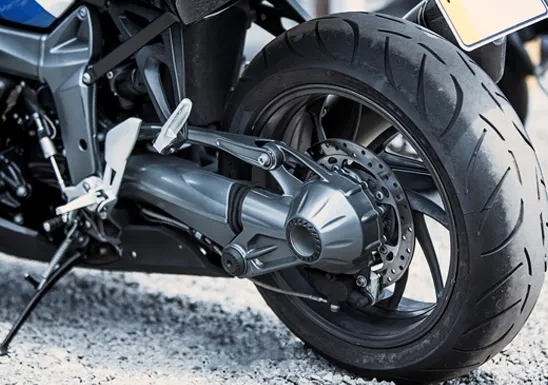
The seal’s design is another pivotal aspect. Lip seals, for example, utilize a flexible lip to maintain contact under varying conditions and are frequently used in rotary applications. Conversely, labyrinth seals provide a series of interlocking channels that form complex paths to block leakage. Each design offers distinctive benefits and constraints, which must align with your machinery's operational environment and specific requirements.
When choosing an oil seal, dimensions such as inner diameter, outer diameter, and width should align with those of the machinery components. Installing a seal that does not fit precisely can result in leaks and machinery failures, emphasizing the importance of accurate measurements and compatibility checks.
oil seal
Use-case scenarios underscore the significance of environmental considerations. Exposure to harsh environmental elements such as dust, moisture, and chemicals necessitate seals with enhanced durability. Regular evaluation of environmental conditions and adjusting seal choices accordingly can drastically reduce wear and tear, mitigating risks and averting costly downtime.
Robust maintenance practices prolong oil seal life, ensuring consistent performance and reliability. Frequent inspections, timely cleaning, and proper lubrication are basic yet vital maintenance steps. Additionally, monitoring for signs of wear, such as grooves or cracking, can preempt serious mechanical issues. Industry experts recommend having a proactive replacement strategy that focuses on predictive maintenance rather than reactive fixes.
Advancements in seal technology continue to evolve, bolstering the efficacy and durability of oil seals. Innovations in composite materials and eco-friendly alternatives are on the rise, driven by demands for sustainability and enhanced performance. Keeping abreast with industry trends and technological developments provides a strategic advantage.
Selecting the right oil seal not only contributes to the seamless operation of machinery but also upholds the integrity and reputation of businesses across industries. Meticulous selection, combined with proactive maintenance, translates to improved efficiency, reduced operational costs, and prolonged equipment lifecycles. By embedding these best practices into operations, businesses not only optimize their machinery but substantiate their leadership in sectors committed to excellence and efficiency.
Ultimately, expert advice and product assurances from reputable manufacturers further consolidate trust and reliability in oil seal choices. Partnering with companies that provide extensive knowledge, customization options, and comprehensive support enhances decision-making and ensures that your investments are safeguarded. This strategic alignment reinforces your business's reliability, achieving sustainable success and operational excellence.