The Importance of Oil Seals in Machinery Maintenance
In the realm of machinery and equipment, the role of oil seals cannot be overstated. These vital components serve as a critical barrier between the internal moving parts of a machine and the external environment, preventing the leakage of fluids and the ingress of contaminants. With their cylindrical or lip-shaped designs, oil seals effectively seal the interface between two rotating or reciprocating surfaces, ensuring that lubricants remain within the system and harmful substances are kept out.
The primary function of an oil seal is to maintain the integrity of the lubrication system in a machine. By creating a tight seal, these components prevent the loss of oil, which is essential for the proper functioning of bearings, gears, and other moving parts. Without adequate lubrication, these components can quickly wear down, leading to reduced efficiency, increased friction, and ultimately, costly repairs or even catastrophic failure.
Moreover, oil seals also protect against the contamination of the lubricant by external elements such as dust, water, and dirt. These contaminants can have a detrimental effect on the performance of the machine, causing corrosion, accelerated wear, and reduced reliability. By acting as a physical barrier, oil seals help to keep these contaminants at bay, ensuring that the lubricant remains clean and effective.
In addition to their functional benefits, oil seals also play a crucial role in extending the lifespan of machinery
In addition to their functional benefits, oil seals also play a crucial role in extending the lifespan of machinery
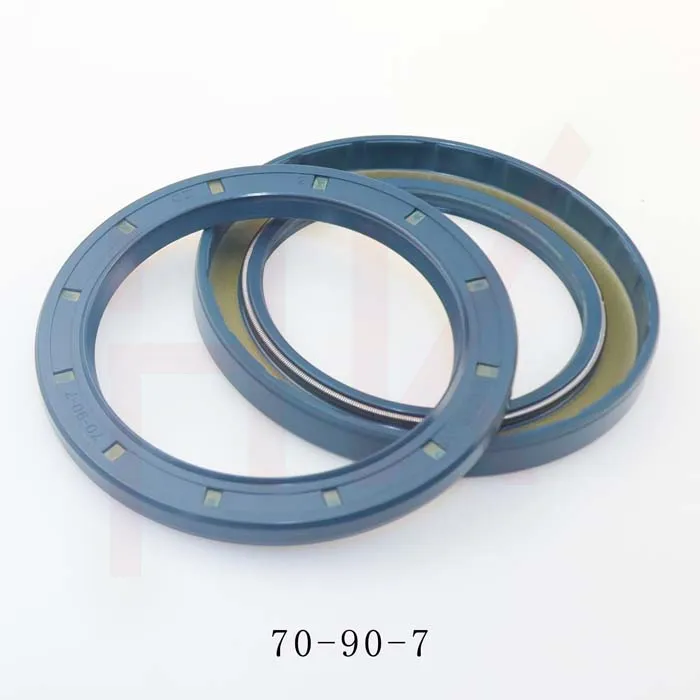
In addition to their functional benefits, oil seals also play a crucial role in extending the lifespan of machinery
In addition to their functional benefits, oil seals also play a crucial role in extending the lifespan of machinery
14x24x6 oil seal. By preventing the ingress of harmful substances and maintaining the purity of the lubricant, these components help to reduce the frequency of maintenance and repair requirements. This not only saves time and money but also minimizes downtime, ensuring that machines can operate at peak efficiency for longer periods of time.
When it comes to selecting the right oil seal for a particular application, it is important to consider factors such as the type of fluid being sealed, the operating temperature and pressure, and the speed and direction of rotation. By choosing a seal that is specifically designed to meet these requirements, engineers can ensure that the seal will perform reliably and effectively throughout its service life.
In conclusion, oil seals are indispensable components in the maintenance of machinery and equipment. Their ability to prevent fluid leakage, protect against contamination, and extend the lifespan of machines make them a critical factor in ensuring the smooth operation and long-term sustainability of industrial processes. As such, it is essential to choose the right oil seal for each application and to regularly inspect and replace these components to ensure optimal performance and longevity.