Mechanical seals play a crucial role in preventing leaks and ensuring the efficient operation of various machinery across industries. The importance of maintaining these components cannot be overstated, as a mechanical seal failure can lead to significant downtime, costly repairs, and even safety hazards. A mechanical seal repair kit is an invaluable resource in such scenarios, designed to restore functionality and extend the service life of seals. This article delves into the experience and expertise surrounding mechanical seal repair kits, offering insights into their benefits, usage, and the importance of choosing the right kit for your needs.
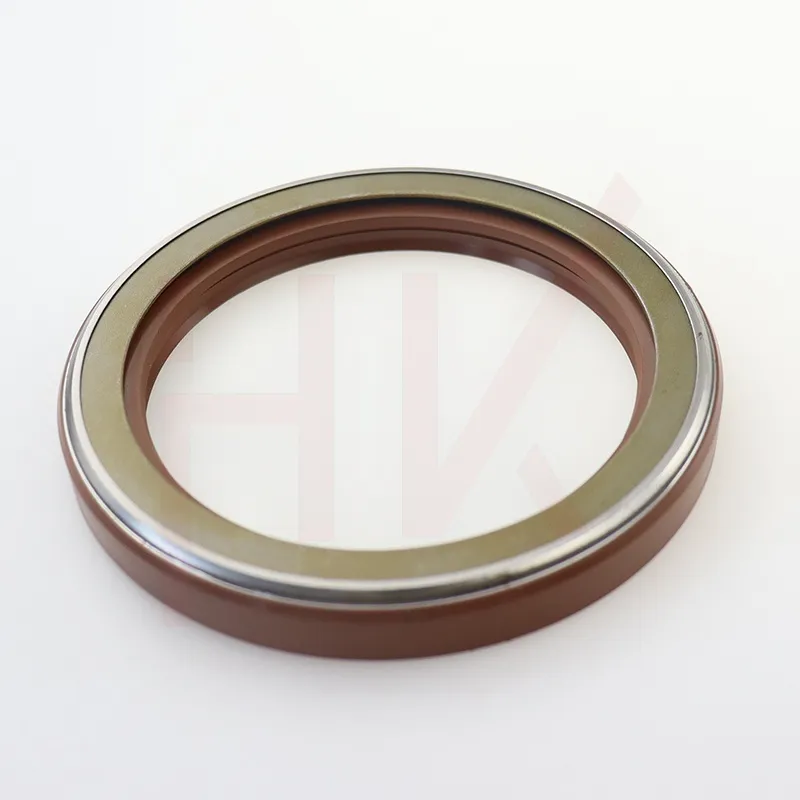
Mechanical seal repair kits are meticulously assembled to cater to a range of seal types and applications. These kits typically include all necessary components such as O-rings, springs, gaskets, and seal faces. The accessibility of these comprehensive kits enhances the experience of maintenance personnel, allowing for efficient on-site repairs without the need for specialized equipment or prolonged waiting periods for individual parts.
From an expert perspective, understanding the compatibility of repair kits with existing systems is paramount. Different systems operate under varying conditions—temperature, pressure, and chemical exposure—which can affect the performance and longevity of seal components. Expert knowledge plays a decisive role in selecting repair kits that match these operational conditions, ensuring that the mechanical seals are not only restored to working order but are optimized for prolonged use.

Authoritativeness in the realm of mechanical seal repair is often established through adherence to industry standards and certifications. High-quality repair kits are manufactured under stringent quality controls, often meeting or exceeding standards set by organizations such as the American Petroleum Institute (API) and the International Organization for Standardization (ISO). This certification underscores a manufacturer's commitment to reliability and performance, providing users with confidence in the products they are utilizing for critical repairs.
mechanical seal repair kit
Trustworthiness is further solidified by testimonials and case studies demonstrating the successful application of these repair kits across various sectors—be it oil and gas, water treatment, or chemical processing. Companies that offer robust after-sales support, detailed installation guides, and customer service also enhance the trust factor, ensuring that users have recourse to expert assistance should uncertainties arise during the repair process.
When considering the purchase of a mechanical seal repair kit, it's essential to evaluate the materials included within the kit. High-performance materials such as carbon graphite, ceramic, and tungsten carbide offer excellent wear resistance and thermal stability, making them suitable for challenging environments. Choosing a kit that provides these reliable materials can significantly impact the effectiveness and durability of the repair.
Moreover, regular training for maintenance teams on the proper use of these kits can greatly enhance their effectiveness. Workshops or instructional materials provided by manufacturers can equip personnel with the necessary skills to carry out proficient repairs and preventive maintenance, minimizing potential operational disruptions.
In conclusion, mechanical seal repair kits are vital investments that combine experience, expertise, authoritativeness, and trustworthiness. By choosing the appropriate kit, companies can achieve reduced downtime, lower maintenance costs, and enhanced safety, ultimately contributing to the seamless operation of their systems. As technology advances and industry standards evolve, staying informed and aligned with best practices in seal repair not only safeguards your equipment but also fortifies your position in an increasingly competitive market.