The inner hub seal plays a critical role in automotive and industrial machines by ensuring the effective sealing of complex mechanisms and preventing unnecessary leakage. As an essential component, its importance cannot be understated, especially in applications involving high-speed rotations and precision engineering.

Understanding the functionality and importance of an inner hub seal requires an exploration of its design and the technology that enhances its efficiency. These seals are typically situated within the core regions of wheel assemblies or machinery where they perform the pivotal role of maintaining lubrication while preventing the ingress of dirt and moisture. This dual protection extends the lifespan of mechanical components by significantly reducing wear and tear.
From a professional's perspective, the applications of inner hub seals span across various industries, showcasing their versatility and necessity. In the automotive sector, they are indispensable for axle systems, providing a seal against contaminants, which if introduced, could lead to significant operational failures. Their ability to withstand harsh environmental conditions makes them ideal for off-road and high-performance vehicles, where reliability is non-negotiable.
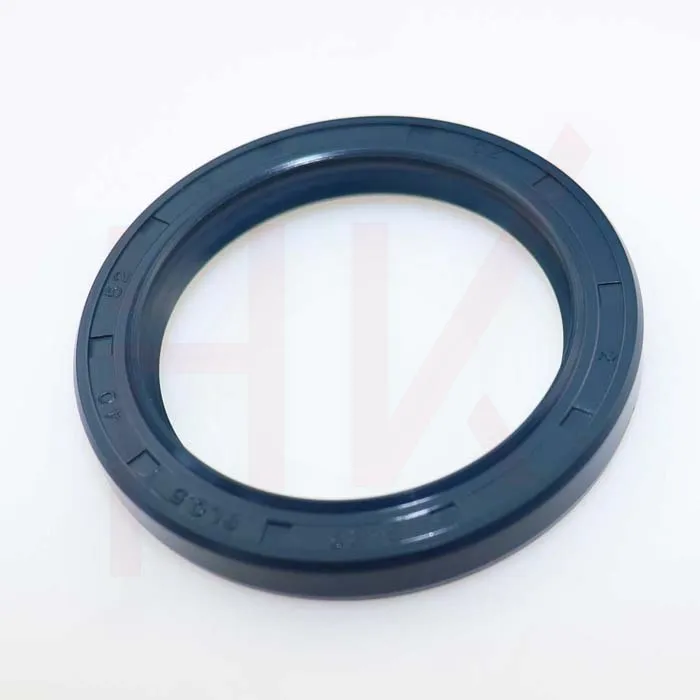
In industrial settings, the inner hub seal is vital in the operation of heavy machinery. Industries such as mining, construction, and manufacturing utilize these seals to prevent the failure of critical machinery parts due to contamination from dust, water, and other environmental factors. This not only guarantees efficient production processes but also minimizes downtime, which can be costly to businesses.
The process of choosing the correct inner hub seal involves understanding the specific operational demands and the environment in which they will function. For example, seals designed for high-temperature operations must be crafted from materials like silicone or fluorocarbon that can withstand excessive heat without suffering degradation.
Similarly, applications with exposure to chemicals require seals made from highly resistant materials such as PTFE.
inner hub seal
The expertise involved in manufacturing inner hub seals is quite profound. The journey begins with rigorous quality control procedures to ensure that each seal meets the necessary industry standards. The manufacturing process is highly specialized, often involving advanced techniques such as computer-aided design (CAD) and precise material engineering to create seals that offer unsurpassed performance. Expert technicians monitor each stage, ensuring that every seal is capable of withstanding the specific stresses it will encounter in its intended application.
As new advancements emerge in materials science and engineering, the capabilities of inner hub seals continue to evolve. Cutting-edge research is focused on developing multi-functional seals that can integrate sensors, allowing for real-time monitoring of seal wear and predictive maintenance. This innovation not only enhances reliability but also aligns with modern industry trends emphasizing the importance of data and analytics in improving machine performance and efficiency.
Furthermore, the aspect of trustworthiness in inner hub seal manufacturers plays a significant role in the industry. Companies that have consistently demonstrated excellence through providing high-quality, durable seals earn reputations that serve as testaments to their reliability. Trustworthy manufacturers are often members of industry organizations that uphold stringent quality standards, a critical factor for buyers when making procurement decisions.
In conclusion, the inner hub seal is far more than a simple component; it is a crucial element that ensures the smooth operation and longevity of machinery across various sectors. Its role in protecting against contamination and maintaining optimal functionality underlines the need for quality, expertise, and reliability in its production. For industry professionals, choosing the right inner hub seal involves a thorough understanding of operational needs, the latest technological advancements, and a trust in proven manufacturers dedicated to producing seals that meet the highest industry standards.