In the ever-evolving landscape of hydraulic systems, the hydraulic wiper seal stands as an unsung hero, a critical component that ensures the longevity and efficiency of machinery. This indispensable accessory embodies precision engineering, offering unparalleled protection against contaminants and leaks, ensuring the smooth operation of hydraulic cylinders. Understanding the intricacies of hydraulic wiper seals reveals not only their functionality but also their importance in various industrial applications.

Hydraulic wiper seals, often termed as scraper seals, are meticulously designed to perform a singular yet crucial function protecting the hydraulic cylinder from external contaminants such as dust, dirt, moisture, and other environmental adversaries. Understanding this functionality requires a dive into their unique design and material composition, both of which are tailored to withstand the rigorous demands of industrial machinery. Typically manufactured from durable elastomers or thermoplastic compounds, their robust construction facilitates outstanding wear and tear resistance, crucial for ensuring longevity amidst harsh operating conditions.
The expertise required in selecting the appropriate hydraulic wiper seal cannot be overstated. Engineers and maintenance professionals must consider several factors, including the type of hydraulic system, environmental conditions, and specific application requirements. The seal's design must complement the piston's rod, ensuring a tight fit to scrape off any dirt and debris effectively as the rod retracts. This selection process underscores the importance of having substantial knowledge and experience in hydraulic systems, ensuring that the seals optimize the system's functionality and efficiency.
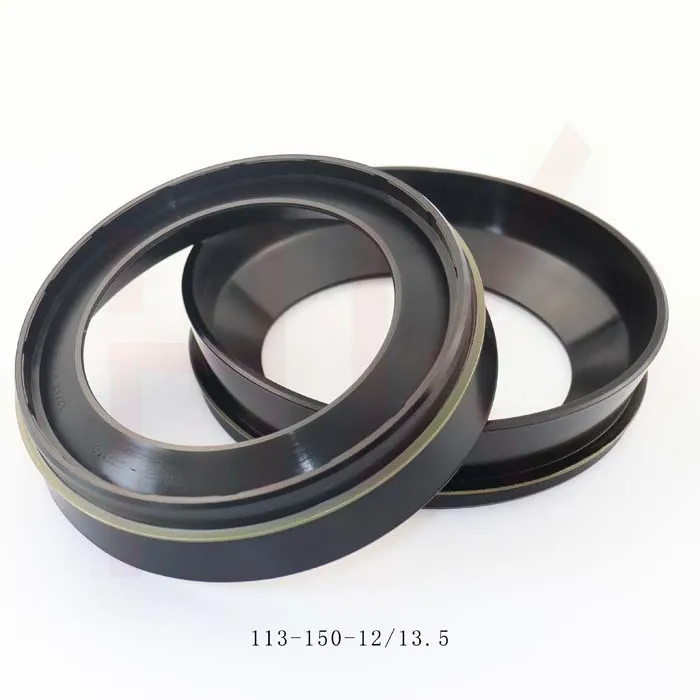
Moving beyond mere functionality, hydraulic wiper seals represent a confluence of engineering authority and innovation. Manufacturers leverage cutting-edge technologies to create seals that not only meet but exceed industry standards. These innovations extend to the development of materials that adapt to various temperature ranges and chemical exposures, further enhancing the seals' reliability and lifespan. This authoritative knowledge embedded in the product design guarantees users of the highest standards in hydraulic sealing solutions.
hydraulic wiper seal
While expertise and authority play significant roles, trust in hydraulic wiper seals is built through real-world applications and field tests. Industries such as automotive, aerospace,
and construction rely heavily on hydraulic systems, which in turn depend on the impeccable performance of wiper seals. Field tests and case studies consistently demonstrate how high-quality wiper seals contribute to reduced maintenance costs and downtime due to their high endurance and protective capabilities. Companies and technicians alike trust these seals for maintaining optimal performance and ensuring the machinery operates without unexpected failures.
Furthermore, in today’s eco-conscious environment, hydraulic wiper seals also contribute to sustainability efforts. By effectively preventing leaks and protecting against contamination, they contribute to environmentally friendly operations. Their role in prolonging the life of hydraulic components reduces waste and the need for frequent replacements, aligning with the broader industry goals of sustainable and responsible manufacturing and maintenance processes.
Emphasizing the importance of regular maintenance, businesses are encouraged to incorporate the inspection and replacement of hydraulic wiper seals into their routine machinery checks. This proactive approach ensures the continuous and effective functioning of hydraulic systems, mitigating the risk of costly repairs or system failures. Knowledgeable professionals understand that the cost of replacing a wiper seal is negligible compared to the potential losses from hydraulic system downtime, further highlighting the seal's value in maintaining operational efficiency.
In conclusion, hydraulic wiper seals are pivotal not just as components within hydraulic systems, but as essential contributors to operational excellence and industrial efficiency. Their role transcends basic sealing functions, representing a blend of expert engineering, robust trustworthiness, and a commitment to sustainability. As industries continue to innovate, the reliance on these unsung heroes remains steadfast, a testament to their unwavering performance and unmatched reliability in the world of hydraulics.