Hydraulic shaft seals play a pivotal role in various mechanical systems, being indispensable components that ensure leak-tightness and optimal functionality. These seals are designed to prevent fluid leakage between a rotating shaft and its housing, safeguarding against potential damage and system failure. With years of application in industries ranging from automotive to heavy machinery, the importance of selecting the right hydraulic shaft seal cannot be overstated.
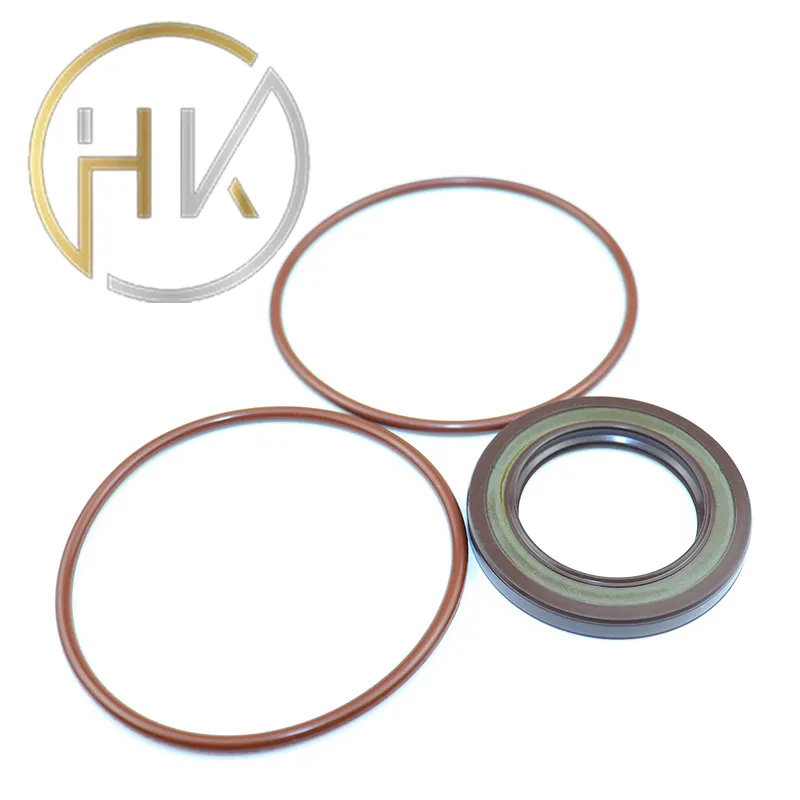
Understanding the intricacies of hydraulic shaft seals begins with recognizing their primary purpose to maintain the hydraulic balance within mechanical systems. These seals do more than just block fluid escape; they are engineered to withstand extreme pressures and temperatures, ensuring longevity and reliability. The choice of material is crucial, as it directly affects the seal's performance. Common materials include nitrile, polyurethane, and fluorocarbon, each offering unique benefits and drawbacks depending on the specific application.
The dynamic between the shaft and the seal is where the real complexity lies. As an experienced engineer will tell you, ensuring a proper fit is key. A poor fit can lead to premature wear, resulting in costly downtime and maintenance. It's essential to consider factors like the shaft's speed, the type of fluid being used, and the operating environment. For instance, in high-speed applications, the seal's material should not only possess exceptional wear resistance but also low friction to prevent heat generation.
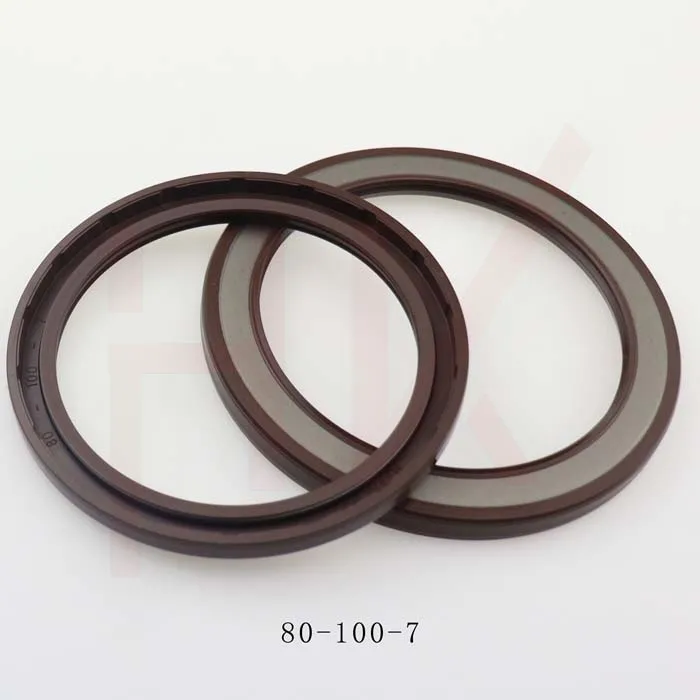
Expertise in designing hydraulic shaft seals requires a deep understanding of the engineering principles that govern fluid dynamics and material science. Engineers often rely on finite element analysis (FEA) simulations to predict how a seal will perform under various conditions. This predictive modeling is crucial not only for new designs but also for troubleshooting existing systems. By simulating real-world conditions, potential issues can be identified and rectified before they manifest in costly failures.
hydraulic shaft seal
The authority of a well-manufactured hydraulic shaft seal is often demonstrated through rigorous testing and certification. Manufacturers must subject their seals to exhaustive testing to ensure they meet industry standards. Certifications from reputable organizations serve as a testament to the product's quality and reliability. Without such certifications, the credibility of a hydraulic shaft seal can be significantly diminished.
Building trust with clients is another critical aspect. This is achieved by maintaining transparency in the manufacturing process and providing detailed product information. Clients are more likely to trust a product that offers complete technical specifications, including installation guides and maintenance tips. Furthermore, offering exceptional customer service, such as consultation and after-sales support, reinforces this trust.
For businesses dealing with hydraulic systems, choosing the right seal from a trusted manufacturer is as important as the system design itself. A reliable seal not only enhances the system's performance but also contributes to its overall efficiency and longevity. It is a small yet significant investment that can lead to substantial savings by minimizing maintenance costs and extending the lifespan of machinery.
In conclusion, hydraulic shaft seals are critical components that should not be overlooked. Their role in maintaining system integrity and performance is undeniable. When selecting a hydraulic shaft seal, consider the specific demands of your application, ensure that the seal has undergone rigorous testing, and rely on manufacturers with proven expertise and authority in the field. By doing so, you bolster the trustworthiness of your mechanical systems, ensuring they operate smoothly and efficiently for years to come.