Hydraulic seal replacement might seem like a daunting task for those unfamiliar with the intricacies of hydraulic systems. However, understanding the vital role these components play and the process involved in replacing them can significantly enhance the efficiency and lifespan of machinery. Let's delve into the essential aspects that encompass the replacement of hydraulic seals, ensuring that the information is not only valuable but also authoritative.
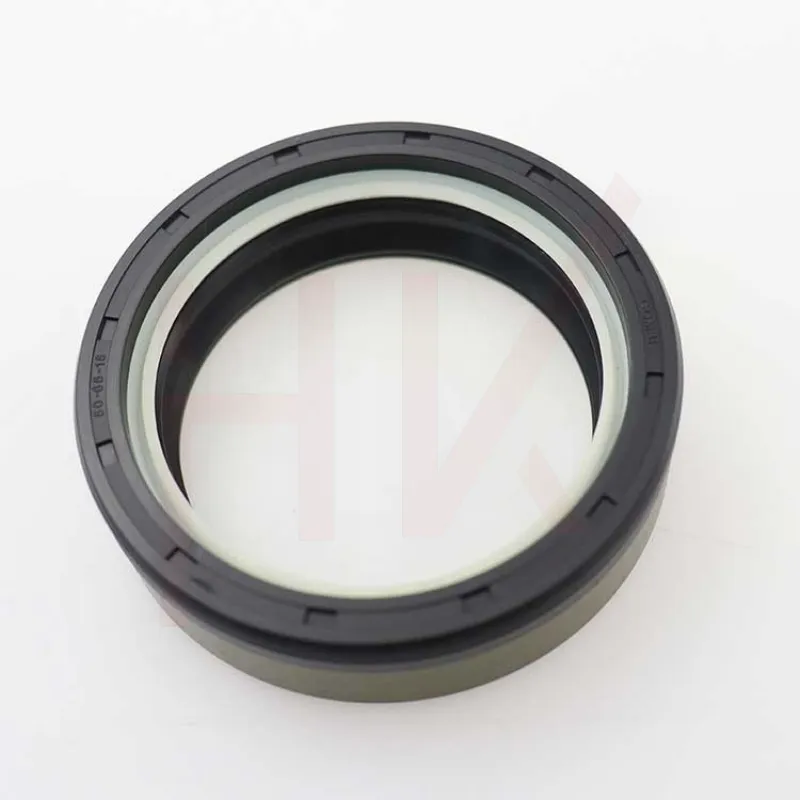
Hydraulic seals are essential components that prevent leakage and maintain hydraulic pressure within various parts of a hydraulic system, such as pumps, cylinders, and valves. These seals, made from materials like rubber, polyurethane, or PTFE, wear out over time due to factors like friction, temperature fluctuations, and exposure to hydraulic fluids. When seals fail, they can lead to serious issues such as fluid leaks, decreased system efficiency, and potential damage to hydraulic components.
Experience has shown that timely hydraulic seal replacement is crucial to the maintenance strategy of hydraulic systems. Waiting too long can exacerbate these issues, leading to costly repairs and downtime. To begin with, identifying the need for hydraulic seal replacement involves regular inspections. Signs that indicate it's time for a change include visible fluid leaks around seals, decreased performance, unusual noises, and increased cycle times.
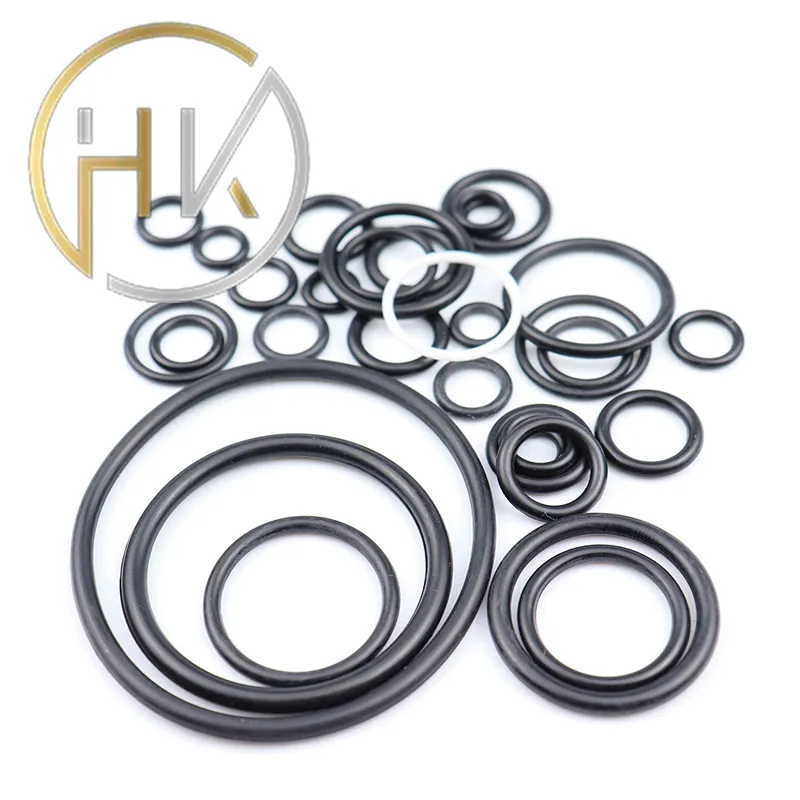
When the need for replacement is confirmed, selecting the appropriate seal type for your specific application is paramount. This requires expertise in understanding material compatibility with hydraulic fluids, temperature ranges, and pressure ratings. For instance, Nitrile rubber seals might be preferred for their versatility and cost-effectiveness, while Viton seals offer better performance in high-temperature applications.
The actual replacement process demands meticulous attention to detail to avoid damaging the new seals or other system components.
Begin by ensuring the hydraulic system is depressurized to prevent hazardous situations. It's crucial to have the correct tools on hand, such as seal picks, O-ring tools, and clean cloths to avoid contamination. Careful disassembly of the hydraulic component follows, taking particular note of how the existing seals are fitted to replicate during reassembly.
hydraulic seal replacement
An authoritative approach to seal replacement involves thorough cleaning of the sealing areas to remove debris and old seal residues. This step is critical for ensuring that the new seals seat properly and function without interruption. Additionally, applying a light amount of compatible lubricant can aid in the installation of new seals, reducing the risk of twisting or pinching during assembly.
Reassembly must be executed with precision, checking that each seal is positioned correctly and all components are secured. This stage of the process cannot be rushed, as improper fitting can lead to immediate leaks or system failures, undermining the entire endeavor. After assembly, the system should be gradually repressurized and tested for leaks before returning to full operational capacity.
Trustworthiness in hydraulic seal replacement is further supported by adhering to manufacturer guidelines and specifications. These documents offer insights into seal dimensions, recommended replacement intervals, and troubleshooting tips that can preempt common issues. Moreover, sourcing seals from reputable suppliers ensures that quality is not compromised, and warranty terms are clear and reliable.
Through this comprehensive approach to hydraulic seal replacement, machinery operators and maintenance personnel can enhance the reliability and performance of hydraulic systems. By combining experience, expertise, authoritativeness, and trustworthiness, the operation not only becomes more efficient but also contributes to the overall longevity of critical industrial equipment.