Hydraulic seals play a pivotal role in maintaining the efficiency and longevity of hydraulic systems. They prevent leakage, maintain pressure, and keep contaminants at bay. However, like all mechanical components, hydraulic seals have a limited lifespan and will eventually require replacement. This article delves into the intricacies of hydraulic seal replacement, offering expert advice grounded in experience and endorsed by authoritative sources, ensuring credibility to guide your purchasing and maintenance decisions.
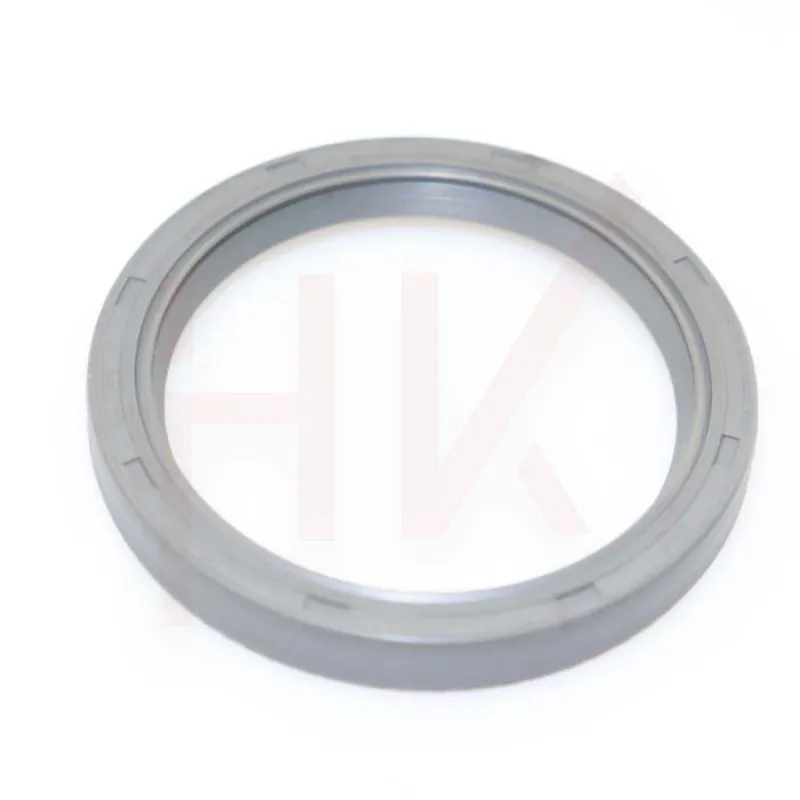
Hydraulic systems are at the heart of numerous industrial applications, from construction machinery to manufacturing equipment. When a hydraulic seal fails, it can lead to significant system inefficiencies, costly downtimes, and potential damage to the machinery. Thus, understanding the nuances of hydraulic seal replacement is crucial for maintaining optimal system performance.
Experience is a teacher, often reinforcing the necessity of routine inspections. Regular visual checks can preempt catastrophic failures by allowing early detection of wear, hardening, or deformation of seals. An experienced technician will know that seal failure isn't solely due to time but can also be exacerbated by factors like extreme temperatures, chemical exposure, and mechanical stress. Timely detection and replacement can significantly extend the life of the entire hydraulic system.
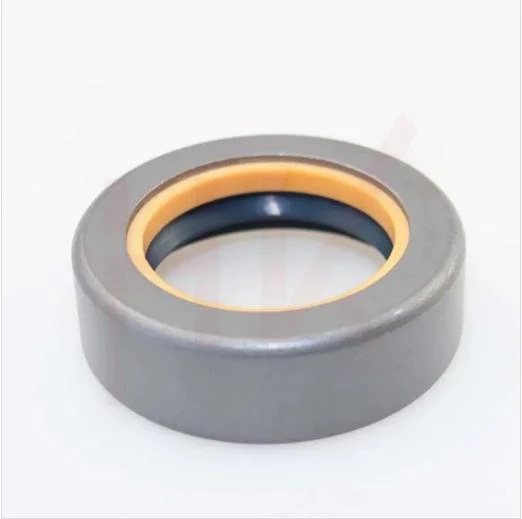
From a professional standpoint, expertise in selecting the right seal for replacement is paramount. Hydraulic seals come in a myriad of shapes, sizes, and materials, each tailored for specific applications and operating conditions. For instance, seals in high-temperature environments might be composed of materials like Viton, which can withstand extreme heat, whereas seals used in low-temperature operations might be made from Nitrile, which remains flexible in the cold. Expertise ensures that the chosen seal material matches its operating environment, reducing the risk of premature failures.
When talking about the authoritativeness, it's important to rely on certified professionals or trusted vendors when sourcing replacement seals. Brands with a reputation for quality, supported by rigorous testing and compliance with industry standards, should be your first choice. For instance, the seals meeting ISO 6194 or AS 568 standards generally assure compatibility and reliability. Additionally, consulting technical manuals provided by manufacturers can provide authoritative guidance on installation and maintenance, ensuring that you're following best practices.
hydraulic seal replacement
Trustworthiness in hydraulic seal replacement also emanates from transparency and accountability in service. Whether conducting maintenance in-house or outsourcing, a reliable provider will offer warranties on their services and parts. They would also maintain an open channel of communication regarding the condition of your hydraulic systems, potential risks, and the expected outcomes of the service performed.
When replacing hydraulic seals, a well-documented process is crucial. Begin by ensuring the system is depressurized and free from any residual hydraulic fluid. Carefully dismantle the relevant components and remove the old seal, inspecting the seal groove for any damage or debris that could impact the new seal's performance. Cleaning the area thoroughly avoids contaminants that could compromise sealing integrity.
Installation requires precision, as even the slightest mishandling can damage a new seal. Employ tools designed specifically for seal installation, ensuring they fit snugly without deformation. Apply a thin film of compatible lubricant to facilitate smooth installation and reduce initial wear. Once installed, reassemble the components, paying close attention to torque specifications and alignment, which prevent uneven pressures and premature failure.
Finally, after replacing hydraulic seals, a post-installation check holds importance. Gradually reintroduce system pressure while monitoring for leaks or abnormal sounds, which may indicate misalignment or improper seating. A systematic approach to post-replacement testing ensures the reliability of the installation before returning to full operational capacity.
Through integrating experiential learning with professional expertise, industry authority, and steadfast reliability, the lifecycle of hydraulic systems can be greatly enhanced. Companies prioritizing these principles in hydraulic seal replacement are better positioned to save on costly repairs, keep downtime minimal, and ensure the safety and efficiency of their operations.