Replacing hydraulic seals is a crucial task in maintaining the efficiency and longevity of hydraulic systems. Hydraulics are used widely across industries, from automotive to industrial machinery, and the seals play a vital role in preventing leaks and ensuring optimal performance. This article delves into the intricacies of hydraulic seal replacement while highlighting real-world experiences, professional insights, authoritative guidelines, and trustworthy practices.
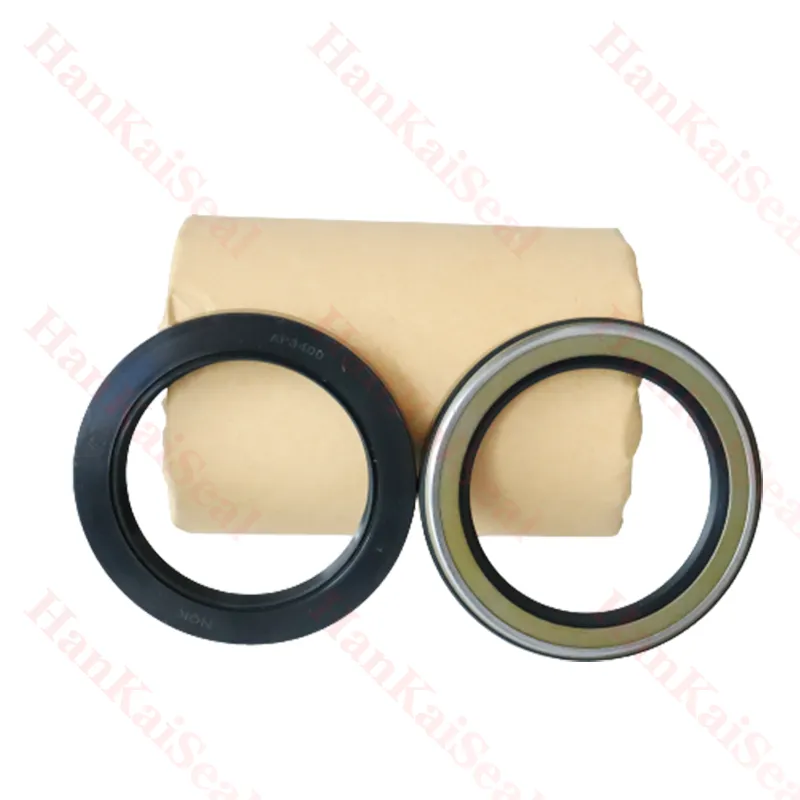
Hydraulic seals come in various types, including piston seals, rod seals, wipers, and rotary seals, each serving specific purposes. The performance of hydraulic machinery heavily depends on these components, as a failure can lead to system inefficiencies, increased maintenance costs, or even complete breakdowns. Industry experts emphasize the importance of recognizing early signs of wear such as leaks, unusual noises, or decreased performance, which indicate that a seal replacement is warranted.
From a professional standpoint, the process of hydraulic seal replacement starts with correctly identifying the type and size of the seal required. This involves understanding the specifications provided by equipment manufacturers, which can often be found in maintenance manuals or through direct manufacturer consultation. Using precise measuring tools, technicians can ensure that the replacement seals match the required dimensions perfectly to avoid further issues or complications.
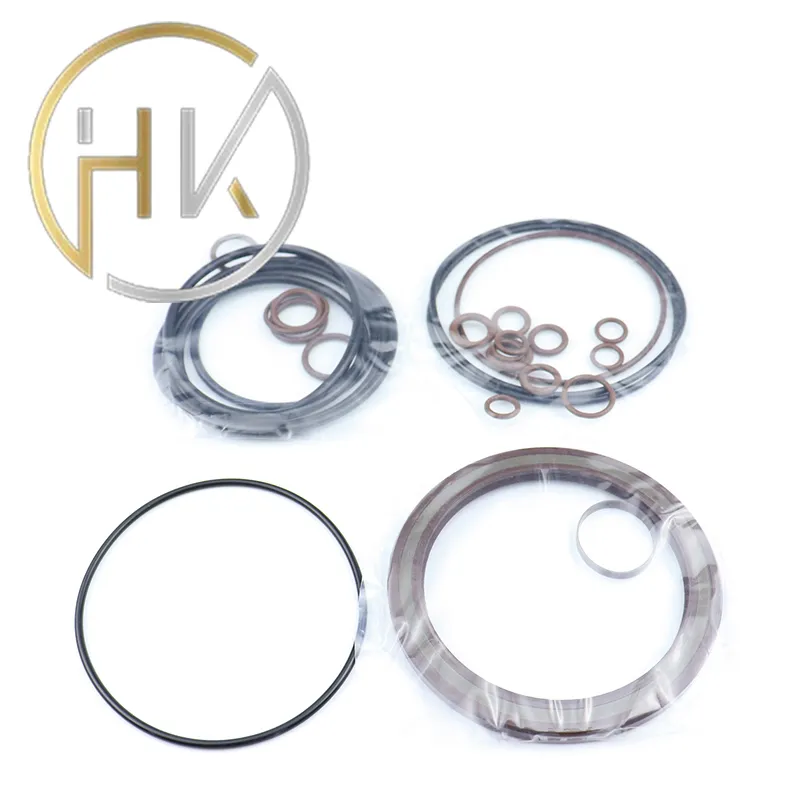
Expertise in hydraulic seal replacement extends beyond just selecting the correct seal; it involves understanding the conditions under which the machine operates. Temperature fluctuations, pressure changes, and exposure to chemicals can all influence seal performance. Therefore, selecting materials that withstand these conditions is paramount. For example, seals made from nitrile rubber are suitable for general use, while those made from PTFE offer better chemical resistance.
hydraulic seal replacement
Speaking to authority in the industry,
adopting best practices is essential for successful seal replacement. This includes cleaning the hydraulic components thoroughly before and after replacement to prevent contamination, which is a leading cause of premature seal failure. Proper lubrication of the seal and surrounding components also ensures smoother operation and longer life. Some manufacturers and certifications provide detailed step-by-step guidelines, which serve as authoritative resources for technicians in maintaining seal integrity.
Trustworthiness in hydraulic seal replacement is built upon reliable products and skilled labor. Partnering with reputable seal manufacturers who adhere to high-quality standards ensures that the products in use are robust and capable of delivering optimal performance. Ensuring technicians are trained and certified reinforces trust, guaranteeing that the replacement process meets the highest industry standards.
Real-world experience highlights several common pitfalls in hydraulic seal replacement. One key issue is the improper installation of seals, which can result in immediate failure or reduced system efficiency. Therefore, training on specific installation techniques and the use of specialized tools is necessary to avoid such setbacks. Additionally, understanding the maintenance schedule and conducting regular checks can prevent unexpected failures and prolong the lifespan of hydraulic systems.
In conclusion, hydraulic seal replacement is an integral facet of maintaining hydraulic machinery that demands a blend of real experience, deep expertise, authoritative practices, and trustworthy operations. Following rigorous procedures, selecting appropriate materials, and relying on established standards will not only ensure the optimal performance of hydraulic systems but also instill confidence in their long-term reliability. By emphasizing the importance of quality products and skilled technicians, industries can safeguard their machinery and continue to reap the benefits of efficient hydraulic operations.