In the realm of fluid power systems, hydraulic seals play a pivotal role. Those who have navigated the intricacies of these systems understand the critical function these seals serve. Their ability to prevent fluid leakage, maintain pressure, and stave off contamination is akin to the linchpin of an engine. This vital component warrants discussion, particularly when one delves into the nuanced experience and expertise required to choose the optimal hydraulic seal for specific applications.
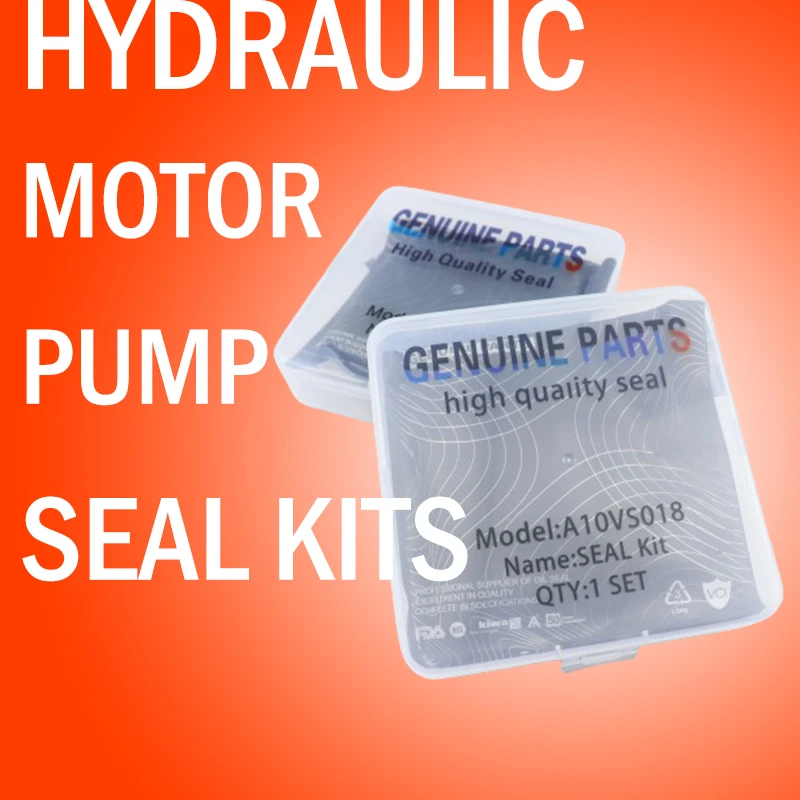
Hydraulic seals are employed in a multitude of industrial applications, ranging from construction machinery to aerospace engineering. Their primary function is to facilitate the smooth transition of fluid power into mechanical force. One of the distinguishing characteristics of hydraulic seals is their adaptability across varied environments, which demands a profound understanding of both material science and engineering specifications.
An experience-driven insight reveals that the longevity and efficiency of hydraulic seals hinge on numerous factors. The material composition, for instance, must align with the fluid type and temperature it is exposed to. Common materials include nitrile rubber, polyurethane, and polytetrafluoroethylene (PTFE), each offering unique properties that suit specific operational conditions. In environments characterized by high temperatures or aggressive chemicals, advanced elastomers or composite materials may be employed to enhance durability.
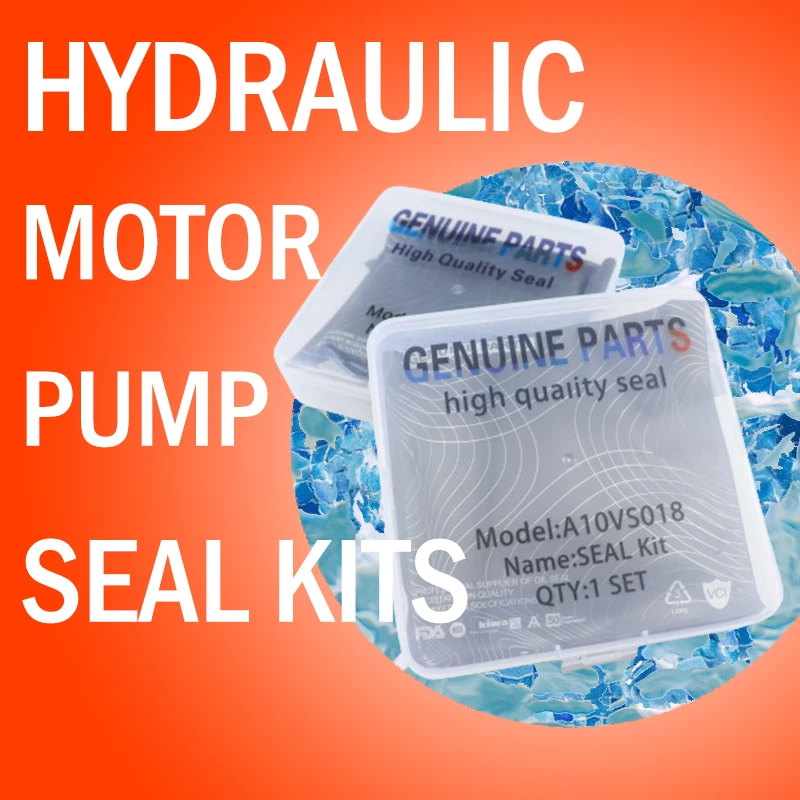
Another layer of expertise involves comprehending the different types of hydraulic seals available. Essentially, they can be categorized into piston seals, rod seals, wipers, and rotary seals. Each type exhibits a distinct functionality and necessitates precise design considerations. For instance, rod seals are critical in preventing leakage from within the cylinder, while piston seals are crucial for separating different pressure zones within a cylinder. Selecting the right type of seal requires an authoritative understanding of system mechanics and operational objectives.
Trustworthiness in the hydraulic seal domain is often evinced by a commitment to rigorous testing and validation. Manufacturers and suppliers that uphold high standards are typically those that earn industry trust. They conduct extensive testing to ensure seals can withstand extreme pressure, temperature fluctuations, and dynamic stresses.
By prioritizing quality over cost, they establish themselves as reliable partners in the lifecycle of hydraulic systems.
hydraulic seal
A testament to the expertise required in the field of hydraulic seals is the continuous innovation and development upheld by leading companies. These entities invest in research and development to produce seals that not only meet but exceed industry standards. Incorporating advanced manufacturing techniques, such as computer-aided design and finite element analysis, they push the boundaries of what hydraulic seals can achieve.
Furthermore, authoritative industry players often cultivate partnerships with academic institutions to facilitate the exchange of knowledge and drive innovation. Such collaborations foster an environment where new materials and technologies can be explored, propelling the industry forward. By integrating academic research with practical engineering, these entities are at the forefront of advancing the capabilities of hydraulic seals.
Real-life experiences shared by seasoned engineers underscore the importance of precise installation and maintenance of hydraulic seals. A seemingly simple error during installation, such as improper alignment or incorrect sizing, can lead to premature failure, affecting the overall system performance. Regular maintenance, including inspection and timely replacement of seals, is crucial in minimizing downtime and enhancing operational efficacy.
Thus, hydraulic seals are not merely passive components; they are active contributors to the success of a myriad of industrial applications. With the right mix of experience, expertise, authoritativeness, and trustworthiness, these seals continue to drive advancements in fluid power technology. For those entrenched in this field, understanding and optimizing the performance of hydraulic seals is a testament to both professional competency and dedication to engineering excellence.