Hydraulic ram oil seals are crucial components in the hydraulic systems used across various industries, known for their reliability and durability. These seals play a pivotal role in ensuring the efficiency and longevity of hydraulic equipment by preventing oil leakage and contamination, which, if unchecked, could lead to costly repairs and system downtimes.
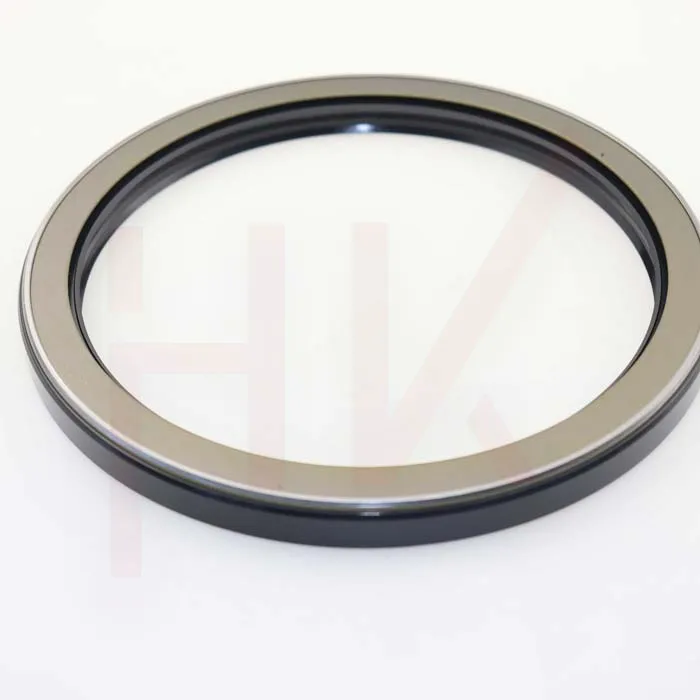
One of the main reasons hydraulic ram oil seals are so vital is their ability to maintain the integrity of the hydraulic system. They are designed to endure high pressure and varying temperatures, attributes that make them essential in ensuring that the oil retains its properties, and the system operates smoothly. Due to their critical function, the selection of hydraulic ram oil seals requires consideration of several factors including material compatibility, environmental conditions, and pressure levels.
Materials used for hydraulic ram oil seals vary, including nitrile rubber, polyurethane, Viton, and PTFE, each offering unique benefits. Nitrile rubber seals are favored for their excellent resistance to petroleum-based oils, while polyurethane seals provide exceptional durability and abrasion resistance. Viton seals, on the other hand, are known for their superior heat resistance and compatibility with a wide range of chemicals. PTFE seals offer outstanding chemical and temperature resistance, making them ideal for extreme environments. Choosing the right material aligns with optimizing system performance and extending the service life of seals.
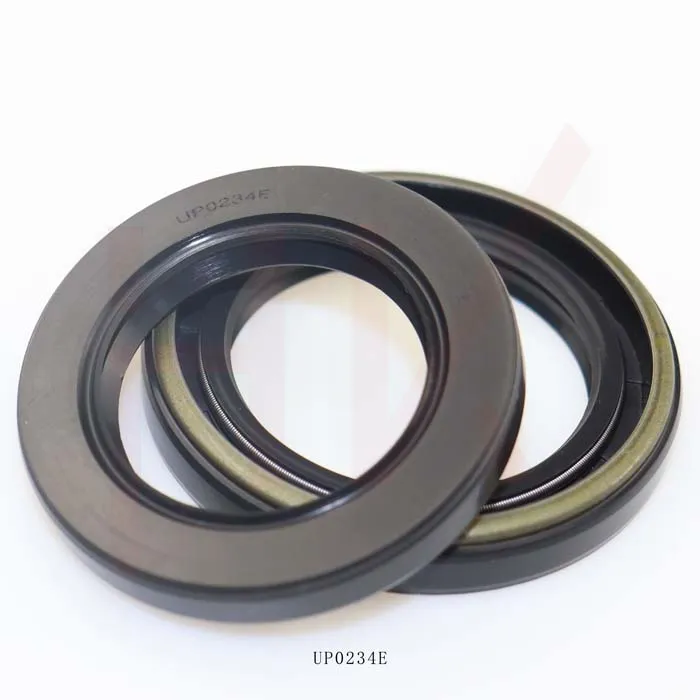
Furthermore, understanding the specific environmental conditions wherein the hydraulic system operates is essential for seal selection. For instance, systems exposed to extreme temperatures or harsh chemicals require seals with enhanced resistance features. Seals need to be engineered not only for the operational pressure but also to accommodate fluctuations that occur during the hydraulic cycle. This ensures that the seals maintain a tight barrier under different operating conditions, preventing leakage and maintaining system pressure.
hydraulic ram oil seals
Installation and maintenance of hydraulic ram oil seals are equally important to ensure their performance and lifespan. Proper installation involves ensuring the seals are correctly aligned and properly seated within their housing. A misaligned seal can cause uneven pressure distribution, leading to premature wear and potential system failure. Regular inspection and maintenance are necessary to monitor the condition of these seals, checking for signs of wear, damage, or hardening. Replacing seals at the first indication of wear can prevent larger system failures and reduce downtime.
In addition to regular inspection, implementing routine cleaning of the hydraulic system can prevent contamination from compromising the seals. Contaminants such as dirt, metal particles, and other foreign materials can lead to abrasion and degradation of the seal material, undermining system efficiency.
Employing high-quality hydraulic oil with additives that enhance seal life can also be effective. These oils often contain anti-wear additives and corrosion inhibitors that reduce friction and protect the system components, including the seals.
Finally, leveraging the expertise of specialists in hydraulic systems can improve the selection and maintenance of oil seals. Professionals with a deep understanding of hydraulic dynamics and seal technology can provide valuable insights, from selecting the most suitable seal material for a specific application to advice on best maintenance practices. This expertise is invaluable in optimizing system uptime and reducing unexpected failures.
To wrap up, hydraulic ram oil seals are integral to the reliability and efficiency of hydraulic systems. Selecting the right seals, ensuring proper installation and maintenance, and leveraging professional expertise are crucial strategies in maintaining system performance and longevity. Investing in high-quality seals and proper upkeep not only extends the life of the hydraulic equipment but also safeguards against unexpected operational halts, enhancing overall productivity in industrial settings.