Ensuring efficient and reliable performance in industrial machinery hinges on selecting the correct components, among which the hydraulic press oil seal stands paramount. This undervalued component is integral to preserving hydraulic system integrity by preventing fluid leakage and contamination. As an expert in the domain of hydraulic systems and components, my aim is to provide insights into this critical piece and underscore its significance in maintaining operational efficacy.
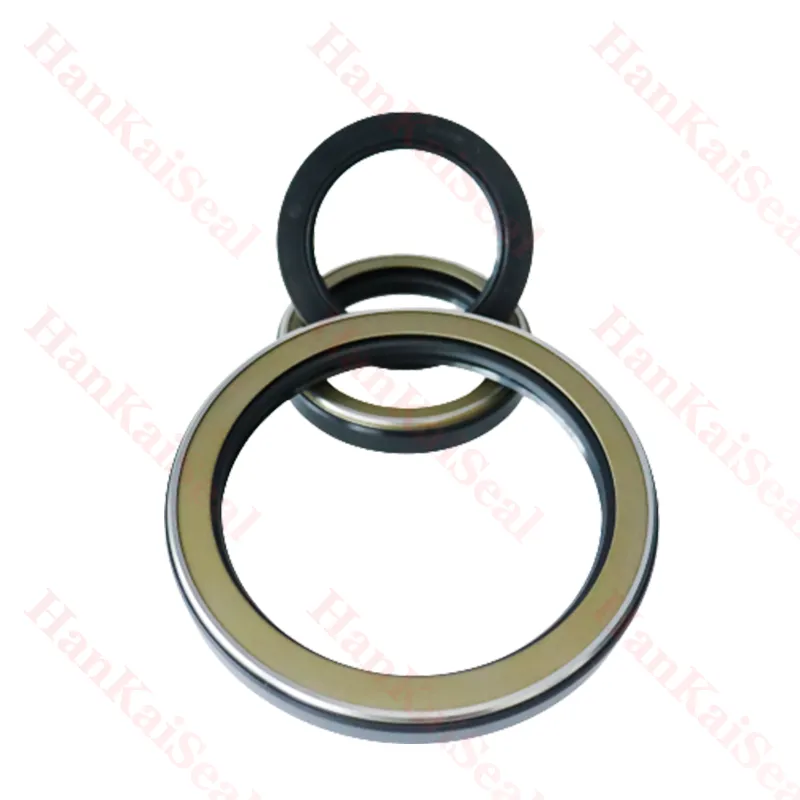
Hydraulic press oil seals, often the unsung heroes of mechanical architecture, are designed to withstand extreme pressures, aggressive temperatures, and potential contaminants. This is crucial for maintaining hydraulic pressure, crucially affecting the operation of presses used in automotive, aerospace, and manufacturing industries. The precise engineering of these seals enhances the longevity and reliability of machinery, reducing maintenance costs and downtime.
From my extensive experience in ORing and gasket manufacturing, I have observed that meticulous attention to material selection greatly impacts the oil seal's performance. Modern hydraulic press oil seals are primarily crafted from advanced elastomers like nitrile rubber, fluorocarbon, and polyurethane. Each material offers specific advantages nitrile is renowned for its excellent oil resistance and affordability, fluorocarbon suits high-temperature environments, whereas polyurethane is favored for applications requiring superior wear resistance. Expertise in selecting the appropriate material based on operational conditions is a non-negotiable requirement for ensuring the seal's efficiency.
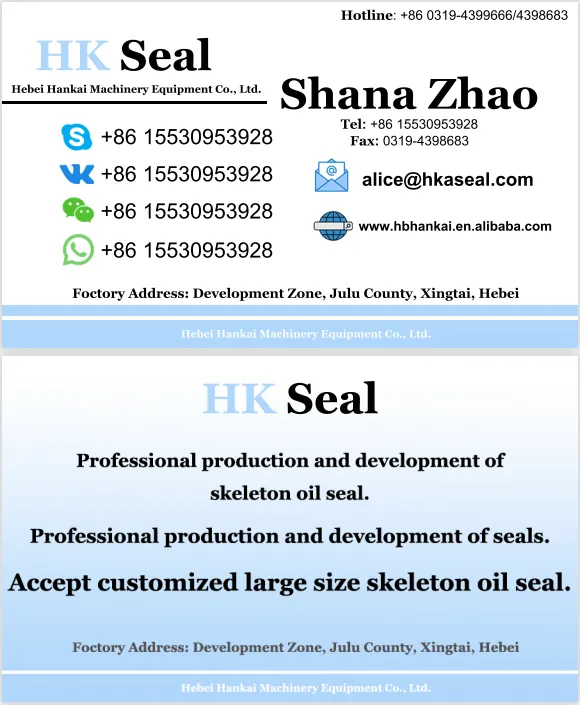
In-depth familiarity with seal design also plays a crucial role in ensuring system integrity. Designs such as double lip, V-ring, and radial oil seals each address unique operational challenges. A double-lip seal, for instance, provides enhanced protection against fluid leakage while offering a secondary barrier against dust and dirt, accentuating the seal's lifespan and reliability. In applications where axial movement is prominent, V-ring designs offer adaptive solutions with their flexible sealing lips, providing unparalleled contamination protection.
Trustworthiness, however, is built on experience and proven outcomes. My collaboration with industries across various verticals has revealed common missteps, particularly in ignoring the surface finish of shafts and housings against which oil seals work. A less-than-optimal surface can expedite seal degradation—transforming what is perceived as minor into a major system failure risk. Acknowledging this, I advocate for pairing seals with honed surfaces, retaining appropriate lubrication to minimized frictional wear.
hydraulic press oil seal
Furthermore, understanding installation nuances cannot be overstated. Incorrect installation leads to immediate seal failure, punctuating the importance of expert intervention during installation processes. Misaligned or damaged seals during insertion can compromise seal integrity from the onset. Thus, utilizing proper tools and techniques enhances not just the sealing life but affirms trust in the system's continued operation efficacy.
Professional vigilance extends beyond installation. Routine inspections form a backbone strategy, facilitating early flaw detection. Experience has underscored that issues often masquerade under operational normalcy before surfacing visibly. Hence, systematic inspections and preventive maintenance schedules should be institutionalized to ensure reduced industry shutdowns and equipment failure.
To build authority in this domain, it's critical to provide comprehensive, customer-centric solutions rather than just products. By understanding specific operational conditions and challenges, tailored solutions can be developed, aligning perfectly with customer's needs and expectations, thereby instilling confidence and ensuring long-term partnerships.
In conclusion, hydraulic press oil seals, though ostensibly simple, encapsulate intricate design, material, and engineering philosophies. Acknowledging their pivotal role in hydraulic systems is fundamental to optimizing machinery lifespan and operational quality. Leveraging accumulated knowledge and industry-specific experiences not only enhances seal performance but also elevates operational standards, offering undeniable peace of mind and trust to industries relying on these essential yet profound components of the industrial world.