Selecting the right hydraulic piston seal kit is paramount for ensuring the efficiency, longevity, and safety of any hydraulic system. In industrial applications where precision and reliability are non-negotiable, an expertly chosen hydraulic seal kit not only enhances performance but also prevents potential downtime due to maintenance issues.
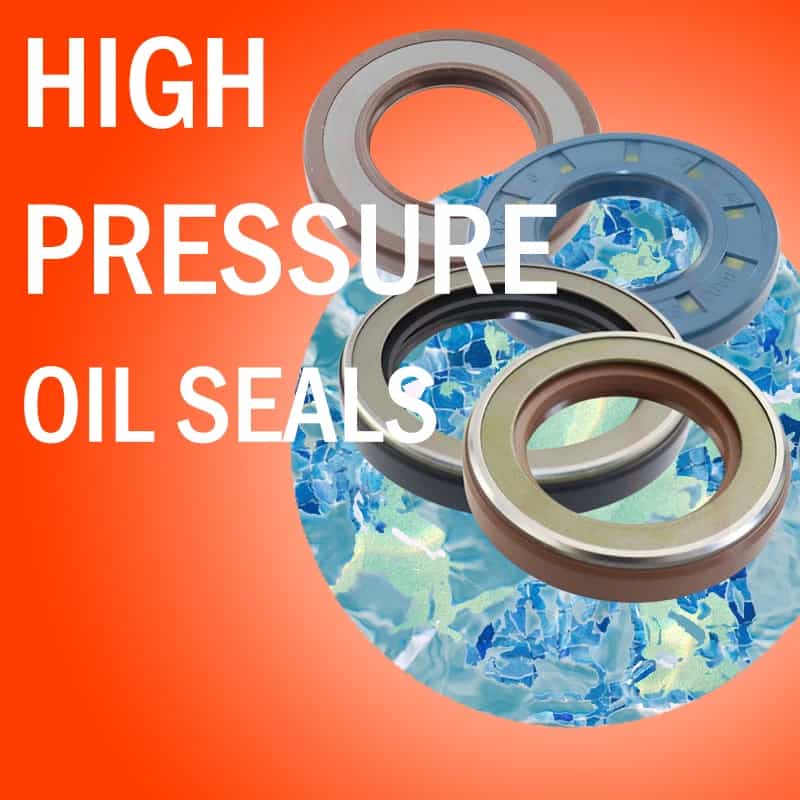
A hydraulic piston seal kit primarily works to prevent any fluid leakage within a hydraulic cylinder, which can impair the system's performance or even lead to operational failure. Given the critical role these seals play, relying on expert knowledge and practical experience is essential for making an informed purchase.
When choosing a hydraulic piston seal kit, the first crucial consideration is the material composition of the seals. Seal materials are typically determined by the specific application environment, temperature range, and types of fluids involved. Common materials include nitrile rubber, polyurethane, and PTFE, each offering distinct advantages. Nitrile rubber stands out for its resistance to low temperatures and compatibility with a broad spectrum of fluids, whereas polyurethane is known for its wear resistance and robust performance in high-pressure systems. PTFE seals, on the other hand, offer exceptional chemical resistance and can operate effectively over a wide temperature range, making them ideal for more demanding applications.
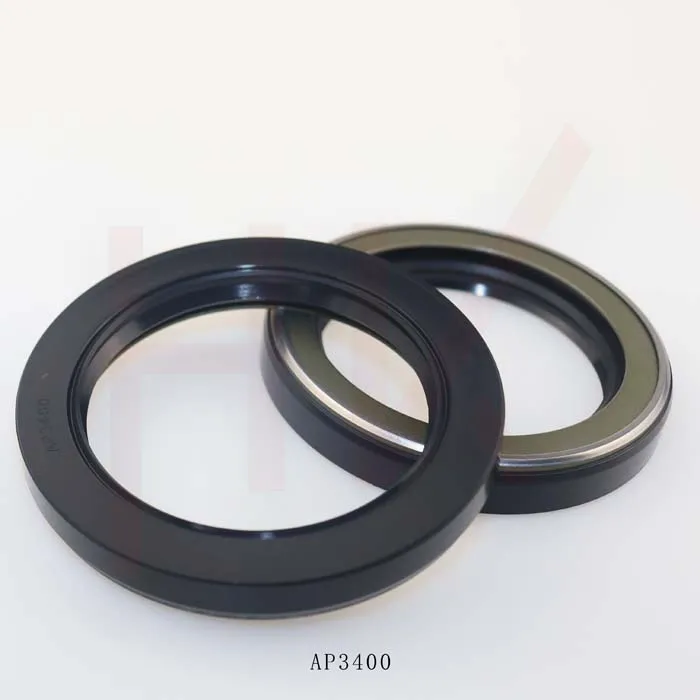
Expert recommendations highlight the significance of the seal design in optimizing a hydraulic system's performance. Single-acting piston seals, double-acting piston seals, and tandem seals are the primary types, each serving unique functions. Single-acting piston seals are used when pressure is applied from only one side, whereas double-acting seals accommodate pressure from both sides, providing an ideal solution for bi-directional arrangements. Tandem seals, which consist of two or more seals arranged in sequence, are preferred for high-pressure applications to enhance their reliability and efficiency.
hydraulic piston seal kit
The feedback from industry veterans stresses the importance of meticulous maintenance and regular inspections of the piston seals to ensure their optimal performance. Early detection of wear, extrusion, or chemical degradation can forestall potential failures. Furthermore, operators should be equipped with proper tools and knowledge to handle seal replacements to maintain existing system integrity.
In building trust with a brand or supplier, the expertise they offer regarding customization of seal kits plays a crucial role.
Some hydraulic applications demand tailored solutions due to specific operational constraints or environmental factors. Manufacturers that provide bespoke solutions demonstrate not only their authority in the field but also their commitment to accommodating niche customer requirements. Such tailored options may include custom geometries, proprietary materials, or specialized coatings that enhance the seals' operation under unique conditions.
When discussing the authority and credibility of seal kit manufacturers, independent testing and compliance with industry standards become distinguishing traits. Leading manufacturers subject their products to rigorous testing regimes to certify their ability to meet or exceed specific benchmarks for performance and durability. Aligning with international standards such as ISO 6194 for rotary shaft lip seal dimensions or ISO 3601 for classifying different types of seals signifies a manufacturer's adherence to global best practices, reinforcing their reputation.
To conclude, choosing a hydraulic piston seal kit requires a blend of expert knowledge, practical experience, and a stringent assessment of product quality and credibility. The right seal kit is a symbiosis of material selection, design appropriateness, and manufacturer reliability. These factors together ensure that the hydraulic system operates smoothly, safely, and efficiently, ultimately achieving superior performance and minimal downtime.