Hydraulic piston oil seals play a crucial role in the efficient operation of hydraulic systems, ensuring leak prevention and maintaining the integrity of the system under various pressures and temperatures. These small yet mighty components are fundamental to ensuring seamless function and longevity of hydraulic equipment, which is integral across various industries such as manufacturing, automotive, and aerospace.

Understanding the construction and function of hydraulic piston oil seals is essential for anyone involved in hydraulic systems. These seals are typically made from a combination of materials including nitrile rubber, fluorocarbon, and silicone, each selected based on its compatibility with hydraulic fluids, resistance to temperature fluctuations, and durability under high pressure. The choice of material directly influences the performance and service life of the oil seal. Nitrile rubber, for example, is often used for its excellent resistance to oil and wear, while fluorocarbon seals are favored in high-temperature applications.
The design of hydraulic piston oil seals involves precision engineering. Seals are structured to fit snugly within the grooves of hydraulic cylinders, creating a seal that keeps hydraulic fluids contained while preventing contaminants from entering the system. This dual function is critical any leakage or infiltration can lead to system failure, resulting in costly downtime and repairs.
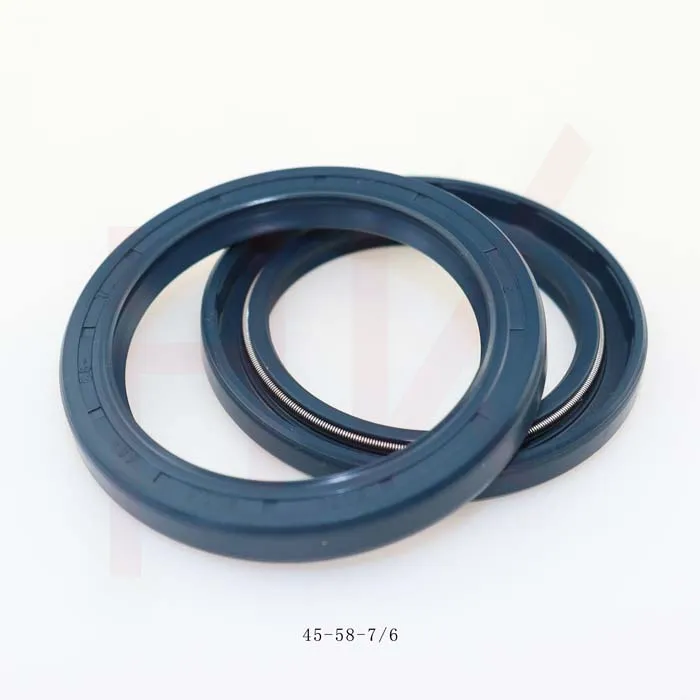
From an expert's perspective, the selection of the right hydraulic piston oil seal involves understanding the specific demands of the application. This includes evaluating factors such as pressure levels, temperatures, and the type of hydraulic fluid used. For instance, seals used in outdoor construction equipment might require enhanced resistance to harsh environments, while those in a controlled factory setting may prioritize temperature stability.
Trustworthiness in hydraulic piston oil seals is achieved through rigorous testing and quality control. Reliable manufacturers subject their seals to extensive testing protocols that simulate real-world conditions, ensuring adaptability and resilience. Consumers should seek seals that are not only compliant with industry standards but also pass additional quality benchmarks set by reputable testing organizations. Certifying authorities often evaluate these components for factors such as tensile strength, elongation, and compression set, which are crucial indicators of performance.
hydraulic piston oil seals
Expert advice encourages routine inspection and maintenance of hydraulic piston oil seals. Regular checks for signs of wear, such as cracking or deformation, can preempt failure and extend the life of the seal and the system it serves. During maintenance, it’s advisable to replace seals in pairs—this ensures that both the piston and rod seals are equally effective, maintaining balance and consistency in the hydraulic operation.
In the vast spectrum of hydraulic systems, oil seals are unsung heroes. Without them, the efficiency of fluid power systems would be severely compromised. Therefore, it’s important for procurement professionals and technical personnel responsible for maintenance to prioritize seal quality and compatibility over cost. Investing in high-quality seals may have a higher upfront cost, but it pays dividends in terms of system reliability and reduced maintenance expenses over time.
Additionally, the future of hydraulic piston oil seals looks promising, with innovations driven by advancements in material science. Fewer friction seals are being developed to reduce energy consumption and increase the lifespan of hydraulic machinery. Moreover, the integration of smart technology into seal design could enable real-time monitoring of seal integrity, allowing for predictive maintenance and reducing unexpected failures.
In conclusion, hydraulic piston oil seals are fundamental components that require thoughtful consideration and judicious selection. Their role in ensuring the efficiency and reliability of hydraulic systems cannot be understated. By focusing on high-quality, appropriately designed seals and implementing regular maintenance checks, industries can safeguard their equipment against failure, supporting longer, more reliable service life. For anyone invested in the optimal performance of hydraulic systems, staying informed about developments in seal technology and best practices in maintenance is not just beneficial—it's imperative.